Welcome to My Blog! 🌟
Before we dive into the content, I’d love for you to join me on my social media platforms. It’s where I share more insights, engage with our vibrant community, and post regular updates. Here’s how you can stay connected:
📘 Facebook: Connect with me on Facebook
Now, let’s embark on this journey together. I hope you find the content here insightful, engaging, and most importantly, valuable. Let’s explore, learn, and grow together! 🚀
Table of Contents
Introduction
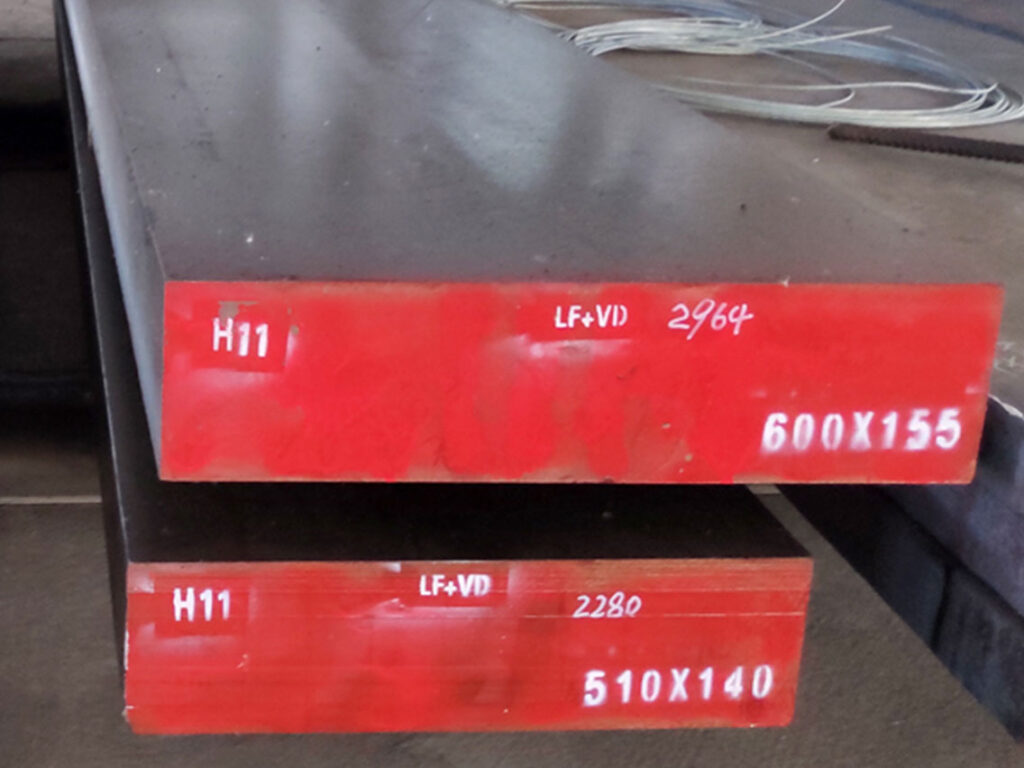
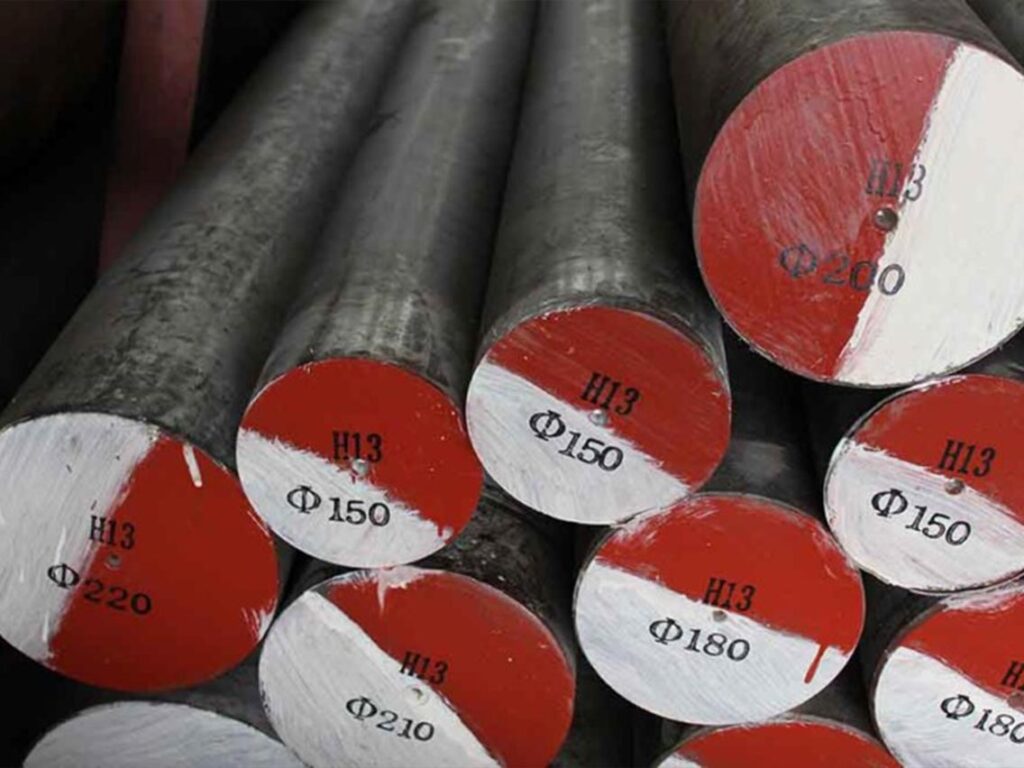
Tool steels are essential in manufacturing and engineering, especially in high-stress applications like forging, extrusion, and die-casting. Among them, H11 and H13 tool steels are two popular choices, both known for their durability and performance under heat and pressure.
However, understanding the difference between H11 and H13 tool steel is crucial when selecting the right material. Although they belong to the same hot work steel family, their compositions, heat resistance, and machinability vary in ways that significantly affect their applications and results.
This guide explores the difference between H11 and H13 tool steel through six key comparisons to help engineers and decision-makers choose the best fit for their production needs.
Comparison 1: Chemical Composition and Alloying Elements
The most basic but vital difference between H11 and H13 tool steel lies in their chemical makeup. Both belong to the H-series of tool steels, designed to withstand high temperatures and repeated thermal cycles. However, subtle variations in elements like chromium, molybdenum, and vanadium greatly impact their behavior in service.
H11 generally contains around 4.75-5.50% chromium and has lower vanadium content compared to H13. H13, with slightly higher chromium and vanadium levels, offers better wear resistance and heat retention. These differences are critical in tooling applications where temperature stability and wear play major roles.
Why This Matters:
- H13 offers better thermal fatigue resistance due to its enhanced alloying.
- H11 is more ductile, making it easier to machine and fabricate.
Comparison 2: Mechanical Properties in Real-World Use
When selecting materials for industrial tools, tensile strength, hardness, and impact resistance are key criteria. Let’s explore the difference between H11 and H13 tool steel through these performance parameters.
Property | H11 Tool Steel | H13 Tool Steel |
---|---|---|
Hardness (HRC) | 48–52 | 50–56 |
Tensile Strength (MPa) | ~1500 | ~1700 |
Impact Resistance | Excellent | Very Good |
Heat Resistance | Good | Excellent |
Toughness | High | Moderate-High |
Wear Resistance | Moderate | High |
Key Takeaways:
- H13 excels in environments requiring prolonged exposure to high heat.
- H11 offers slightly better toughness, which is ideal for shock-loading scenarios.
Comparison 3: Heat Treatment and Machinability
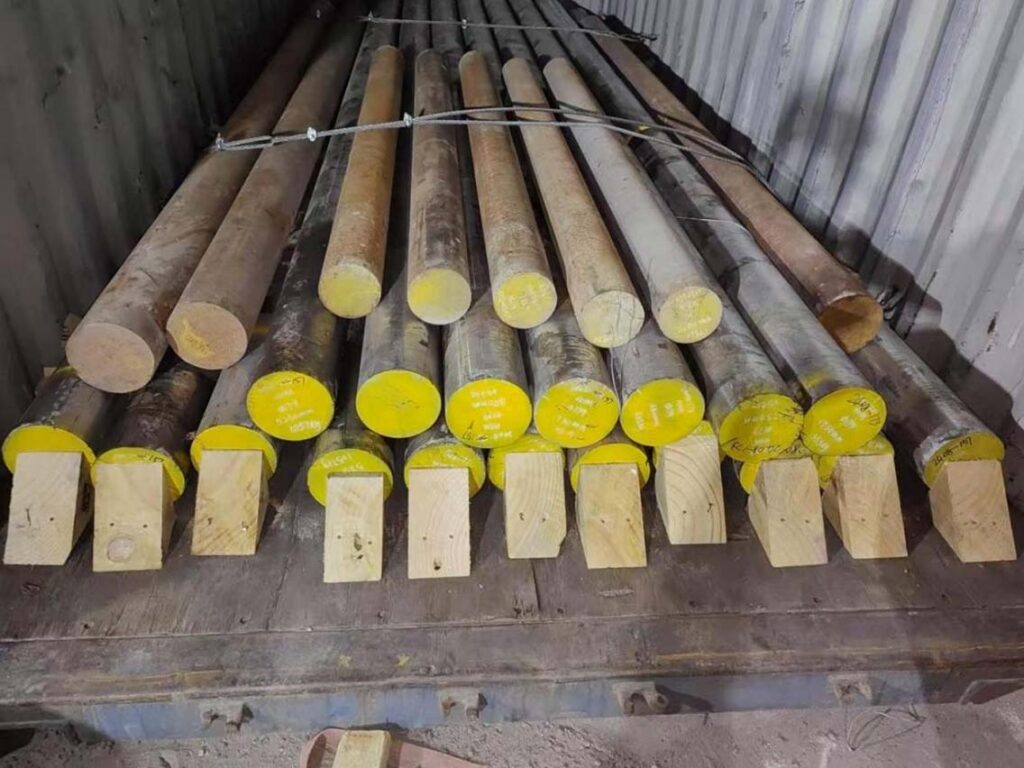
Heat treatment significantly influences how tool steels perform in different industrial settings. The difference between H11 and H13 tool steel becomes even more noticeable during thermal processes such as annealing, quenching, and tempering.
H11 tool steel can be hardened and tempered at lower temperatures. This quality contributes to its greater ease of machining, especially in its pre-hardened state. Industries that require precise shaping and easier cutting often choose H11 because it allows for simplified machining without compromising too much on strength.
In contrast, H13 tool steel requires a more controlled and extended heat treatment process. While this may result in higher processing costs and longer lead times, the benefits include superior thermal stability and reduced distortion during high-temperature applications. For precision tools that must maintain shape under repeated heating, H13 becomes a more viable solution.
The difference between H11 and H13 tool steel in machinability and heat response can directly influence production strategies. Choosing the right one depends on whether your process demands short-term flexibility or long-term thermal reliability.
Industrial Application Insight:
H11 is frequently selected for hot forging dies and die-casting tools where the ability to shape complex geometries is essential. Its machinability before hardening offers more manufacturing freedom.
H13 is better suited for high-volume die casting, especially aluminum, where thermal resistance, minimal deformation, and dimensional accuracy are crucial over prolonged usage.
Understanding how each material responds to heat treatment is key to grasping the deeper difference between H11 and H13 tool steel in manufacturing contexts.
Comparison 4: Application Suitability in Manufacturing
Selecting the appropriate tool steel is not a one-size-fits-all decision. The difference between H11 and H13 tool steel becomes evident when evaluating the real-world performance requirements in manufacturing.
Each steel grade has a specialized role depending on how much heat, impact, and wear a component is exposed to. Application suitability is directly tied to mechanical properties, which vary between H11 and H13.
Common Uses of H11 Tool Steel:
- Aircraft landing gear and structural aerospace components
- Hot forging dies and mechanical tooling
- Hydraulic tools and high-load shafts
- Industrial parts subject to repetitive impact and flexing
H11’s excellent ductility and impact resistance make it an ideal choice where shock loads and structural reliability are major concerns. The material holds up well under dynamic forces, even if thermal exposure is moderate.
Common Uses of H13 Tool Steel:
- Extrusion dies that demand tight tolerances and long tool life
- Die-casting molds that face repeated heating and cooling cycles
- Injection molds for plastic manufacturing
- Cutting blades and wear tools requiring surface hardness and dimensional stability
H13 is the preferred material in high-temperature environments where maintaining accuracy and strength over time is critical. For manufacturers focused on product longevity and heat cycling performance, the difference between H11 and H13 tool steel becomes a deciding factor.
This practical understanding helps engineers and procurement teams align tool steel selection with specific production needs.g enhanced ductility.
Comparison 5: Cost and Availability in the Global Market
When evaluating the difference between H11 and H13 tool steel, cost and availability are key factors. H13 tool steel is generally more expensive due to its higher alloy content, including chromium, molybdenum, and vanadium, which contribute to its superior hardness and thermal resistance. The extended heat treatment cycles required for H13 further increase its cost. However, its longer lifespan often results in a lower cost-per-use in high-demand applications, such as die-casting and mold-making.
In contrast, H11 is more affordable and easier to procure, making it a practical choice for mid-scale production with less demanding conditions. Its simpler alloy composition and more straightforward heat treatment process contribute to its lower cost, making it ideal for impact-heavy applications with shorter tool life cycles.
When considering the difference between H11 and H13 tool steel, the choice largely depends on your budget and production needs. For high-temperature, long-life applications, investing in H13 may offer a better return on investment. However, for simpler, lower-cost operations, H11 offers a cost-effective solution.
Budgeting Tip:
For short-run production and impact-heavy tasks, H11 is an efficient and affordable choice. For high-temperature environments with tight tolerances, H13 provides the durability and performance needed to reduce downtime.
Comparison 6: Performance in High-Temperature Environments
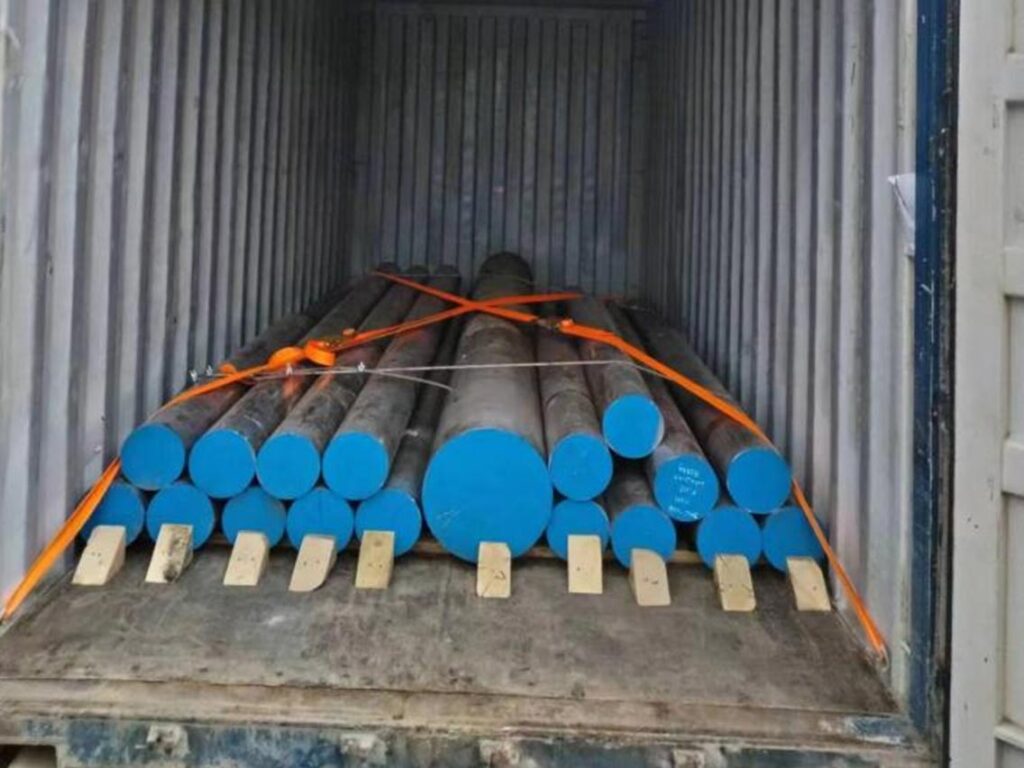
Both H11 and H13 are part of the hot work steel family, but their performance varies under thermal cycling and extended exposure to high temperatures. This comparison helps clarify the long-term behavior of each steel.
H13 retains its hardness and resistivity better at higher temperatures than H11. This makes it ideal for die-casting or any application where the steel remains hot for prolonged periods. H11, while still effective, may suffer from reduced performance in similar scenarios unless specially treated.
Best Practices:
- Opt for H13 when working with molten metals and plastics.
- H11 remains ideal for intermittent heating and mechanical load bearing.
Conclusion
The difference between H11 and H13 tool steel comes down to toughness versus heat resistance. If your tools face high temperatures and wear, H13 is the better option. If you need impact resistance and easier machining, H11 may be more suitable.
Understanding the difference between H11 and H13 tool steel helps ensure you choose the right material for your budget and application—leading to longer-lasting and more efficient performance.
FAQ
Is H13 always better than H11?
Not necessarily. While H13 tool steel is well-known for its superior performance in high-temperature environments and for maintaining hardness under heat, it doesn’t automatically make it the better choice in every application. The difference between H11 and H13 tool steel becomes evident when toughness and ductility are a priority. In such cases, H11 has the edge due to its higher impact resistance. So, choosing H13 over H11—or vice versa—should depend entirely on the operational environment and design requirements. Always consider both mechanical needs and thermal loads when evaluating the difference between H11 and H13 tool steel.
Can H11 and H13 be welded easily?
Both H11 and H13 tool steels can be welded, but they require careful thermal management during the process. Due to the high hardenability and alloying elements in H13, it’s especially sensitive to cracking. Therefore, preheating and post-weld heat treatment are strongly recommended to avoid microstructural damage. The difference between H11 and H13 tool steel also comes into play here—H11, while still requiring thermal precautions, is typically more forgiving during welding due to its enhanced ductility. Whether you choose H11 or H13, proper welding procedures are essential to maintain structural integrity.
Which tool steel is easier to machine?
The difference between H11 and H13 tool steel includes variations in machinability. H11 is generally regarded as easier to machine, mainly because it has slightly lower hardness compared to H13. This makes it a preferred choice for projects that involve a high amount of machining or custom shaping. While H13 offers excellent wear resistance, its added chromium and vanadium content contribute to increased hardness, which can reduce machining efficiency unless specialized tools and coolants are used. If machining time and cost are critical factors, H11 may offer advantages over H13.
Are H11 and H13 interchangeable in all applications?
No, H11 and H13 tool steels are not universally interchangeable. The difference between H11 and H13 tool steel lies in their unique compositions and thermal capabilities, which tailor them to specific roles. For instance, H13’s superior heat resistance makes it a top choice for high-pressure die-casting and extrusion applications, while H11 may be more suitable for impact tools and hammer dies where toughness is more valuable than heat retention. Always consult detailed engineering specifications before making substitutions between these two grades, as incorrect usage can result in premature failure or suboptimal performance.
Which tool steel lasts longer in die-casting applications?
In die-casting operations, longevity is typically linked to a material’s ability to withstand repeated thermal cycling and exposure to molten metals. In this context, H13 usually outperforms H11 due to its enhanced heat resistance, superior wear characteristics, and excellent thermal fatigue resistance. This is a significant factor in the difference between H11 and H13 tool steel. While H11 offers good performance, H13’s ability to maintain its hardness and structural integrity under prolonged exposure to high temperatures makes it the more durable option for die-casting molds, cores, and inserts.