Welcome to My Blog! 🌟
Before we dive into the content, I’d love for you to join me on my social media platforms. It’s where I share more insights, engage with our vibrant community, and post regular updates. Here’s how you can stay connected:
📘 Facebook: Connect with me on Facebook
Now, let’s embark on this journey together. I hope you find the content here insightful, engaging, and most importantly, valuable. Let’s explore, learn, and grow together! 🚀
Table of Contents
Introduction
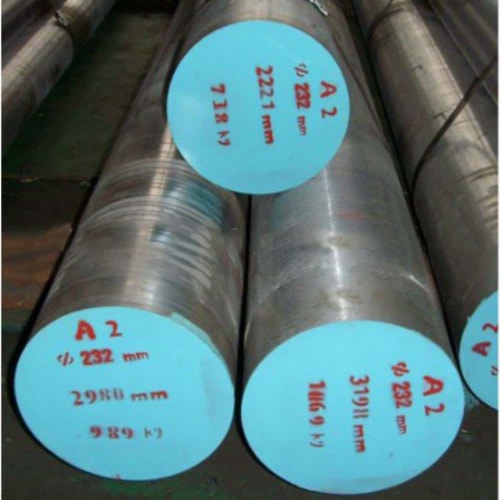
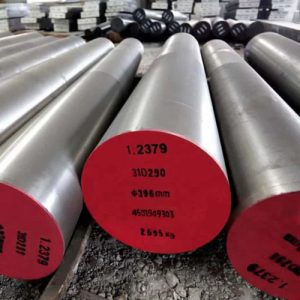
When selecting tool steel for high-performance applications, two of the most debated options are D2 vs A2 tool steel. Both are cold-work tool steels known for their hardness, wear resistance, and toughness, but they differ significantly in composition, heat treatment, and real-world performance.
This in-depth comparison will analyze D2 vs A2 tool steel in terms of durability, edge retention, corrosion resistance, machinability, and cost-effectiveness. By the end, you’ll know which steel is best suited for your specific needs—whether for knives, dies, punches, or industrial tooling.
NO 1. Composition and Metallurgy: D2 vs A2 Tool Steel
Understanding the chemical makeup of D2 vs A2 tool steel is crucial because it directly impacts durability and performance.
D2 Tool Steel Composition
D2 is a high-carbon, high-chromium tool steel (semi-stainless) with the following key elements:
- Carbon (1.5%) – Provides hardness and wear resistance
- Chromium (12%) – Enhances corrosion resistance and hardenability
- Molybdenum (1%) & Vanadium (1%) – Improve toughness and grain refinement
A2 Tool Steel Composition
A2 is an air-hardening, medium-alloy tool steel with a balanced composition:
- Carbon (1%) – Lower than D2, making it slightly tougher
- Chromium (5%) – Less corrosion-resistant than D2 but still durable
- Molybdenum (1%) & Vanadium (0.3%) – Aid in wear resistance and stability
Key Differences in Metallurgy
Property | D2 Tool Steel | A2 Tool Steel |
---|---|---|
Carbon Content | 1.5% (Higher) | 1% (Lower) |
Chromium % | 12% (Semi-Stainless) | 5% (Less Corrosion-Resistant) |
Primary Strengths | Extreme wear resistance, good corrosion resistance | Better toughness, easier to machine |
Hardness Potential | 60-62 HRC | 58-60 HRC |
Grain Structure | Larger carbides | Finer grain |
NO 2. Hardness and Wear Resistance: D2 vs A2 Tool Steel
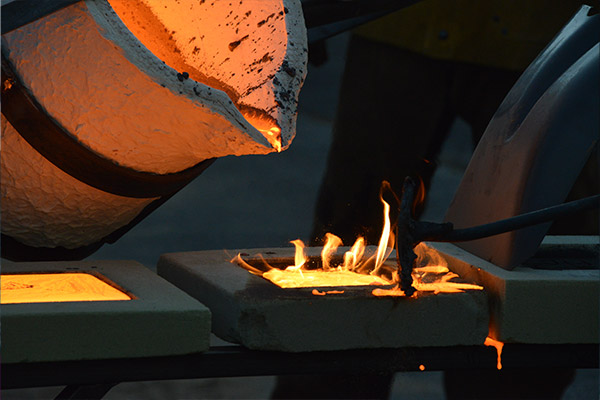
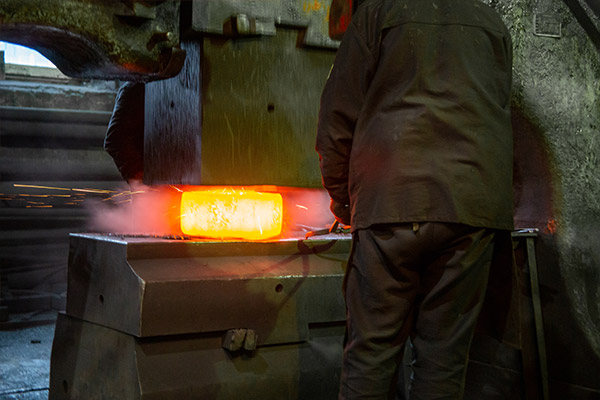
When comparing D2 vs A2 tool steel for durability, hardness and wear resistance are critical factors.
Hardness Capabilities
D2 tool steel typically achieves higher hardness levels (60-62 HRC) compared to A2 (58-60 HRC) when properly heat treated. This gives D2 superior resistance to abrasive wear, making it ideal for applications involving:
- Long-term cutting operations
- High-abrasion environments
- Applications requiring extended edge retention
A2 tool steel, while slightly softer, offers better impact resistance due to its finer grain structure and lower carbon content. This makes it preferable for:
- Punches and dies subject to shock loading
- Tooling that requires some deformation resistance
- Applications where chipping is a concern
Wear Resistance Comparison
In standardized wear tests (ASTM G65), D2 consistently outperforms A2 in abrasive wear scenarios. However, A2 demonstrates better performance in situations involving:
- Combined abrasion and impact
- Cyclic loading conditions
- Applications requiring repeated sharpening
NO 3. Toughness and Impact Resistance: D2 vs A2 Tool Steel
The debate between D2 vs A2 tool steel often centers around toughness – the steel’s ability to withstand impact without fracturing.
Charpy Impact Test Results
Testing shows A2 tool steel generally exhibits 20-30% better impact resistance than D2 at equivalent hardness levels. This difference becomes particularly important for:
- Cold work tooling applications
- Punches and dies
- Woodworking tools subject to lateral forces
Fracture Toughness
A2‘s finer grain structure and lower carbide volume contribute to:
- Better resistance to crack propagation
- Improved performance in fatigue applications
- Reduced likelihood of catastrophic failure
D2’s larger carbides can act as stress concentrators, making it more prone to chipping in high-impact scenarios despite its excellent wear resistance.
NO 4. Corrosion Resistance: D2 vs A2 Tool Steel
When evaluating D2 vs A2 tool steel for applications exposed to moisture or corrosive environments, their chromium content plays a significant role.
Rust Resistance Comparison
D2’s higher chromium content (12% vs 5%) gives it noticeably better corrosion resistance. In salt spray tests:
- D2 shows first signs of rust after 48-72 hours
- A2 typically begins showing oxidation within 24 hours
Practical Implications
This difference means D2 is better suited for:
- Marine applications
- Food processing equipment
- Tools used in humid environments
A2 requires more frequent maintenance and protective coatings when used in corrosive environments.
NO 5. Machinability and Heat Treatment: D2 vs A2 Tool Steel
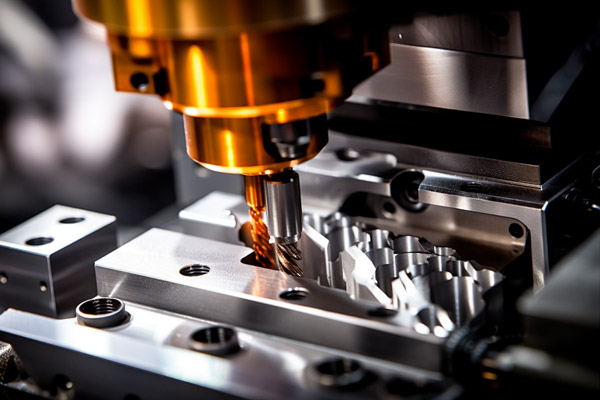
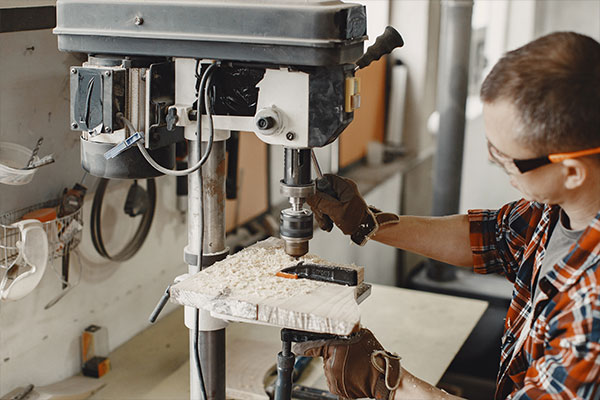
The differences between D2 vs A2 tool steel become particularly apparent during manufacturing and heat treatment processes.
Machinability Ratings
A2 is generally easier to machine, with approximately:
- 20% better machinability in annealed condition
- Lower tool wear during machining operations
- Better surface finish capabilities
D2’s higher alloy content and carbide volume make it more challenging to machine, requiring:
- Slower speeds and feeds
- More frequent tool changes
- Careful attention to tool geometry
Heat Treatment Considerations
Both steels require precise heat treatment, but with key differences:
Process | D2 Tool Steel | A2 Tool Steel |
---|---|---|
Hardening Temp | 1850-1925°F | 1750-1850°F |
Quench Medium | Oil or air | Air |
Tempering Range | 350-1000°F | 350-1000°F |
Dimensional Stability | More sensitive | More stable |
Conclusion
After examining D2 vs A2 tool steel across multiple performance categories, the “winner” depends entirely on your specific application requirements.
Choose D2 tool steel when:
- Maximum wear resistance is critical
- Corrosion resistance is important
- Extreme hardness is needed
- Edge retention is paramount
Opt for A2 tool steel when:
- Impact resistance is crucial
- Machinability is a concern
- Better toughness is required
- Cost is a significant factor
Both steels offer excellent performance when properly selected and heat treated. Consider your operational environment, expected stresses, and maintenance capabilities when making your final decision between D2 vs A2 tool steel.
FAQ
Can D2 and A2 tool steel be welded?
Both can be welded with proper precautions, but A2 is generally easier to weld due to its lower carbon content. Post-weld heat treatment is recommended for both.
Which holds an edge longer – D2 or A2 tool steel?
D2 typically maintains a sharp edge longer due to its higher hardness and wear resistance, making it preferable for cutting applications.
Is D2 tool steel stainless?
While D2 contains 12% chromium, it’s technically semi-stainless. It offers better corrosion resistance than A2 but less than true stainless steels like 440C.
Which is more cost-effective – D2 or A2 tool steel?
A2 is generally less expensive both in material cost and machining costs, making it more economical for many applications.
Can these steels be used for knife making?
Yes, both are popular for knives. D2 is favored for its edge retention while A2 is preferred for its toughness and ease of sharpening.