Welcome to My Blog! 🌟
Before we dive into the content, I’d love for you to join me on my social media platforms. It’s where I share more insights, engage with our vibrant community, and post regular updates. Here’s how you can stay connected:
📘 Facebook: Connect with me on Facebook
Now, let’s embark on this journey together. I hope you find the content here insightful, engaging, and most importantly, valuable. Let’s explore, learn, and grow together! 🚀
Table of Contents
Introduction
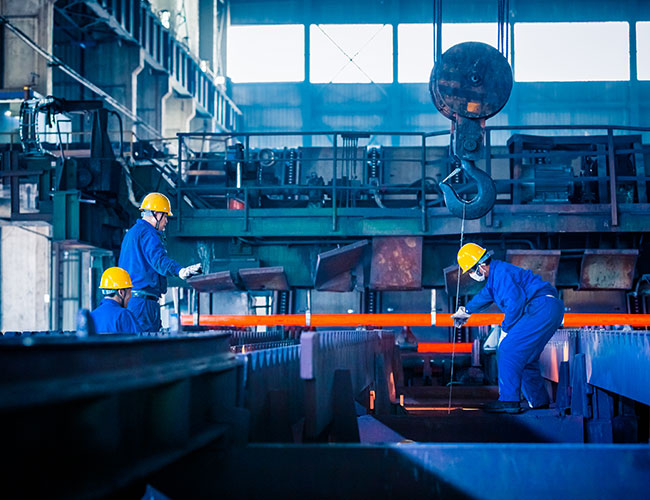
When it comes to choosing the right tool steel for precision tooling and industrial applications, the comparison between d2 vs a2 tool steel continues to be a hot topic in 2025. These two cold work tool steels, although similar in their usage categories, differ significantly in their chemical composition, mechanical performance, wear resistance, and toughness. This blog will delve deeply into their pros and cons, enabling manufacturers, engineers, and procurement professionals to make more informed decisions for their tooling needs.
Chemical Composition and Mechanical Properties
Understanding the fundamental differences in chemical makeup and physical performance helps to distinguish how d2 vs a2 tool steel operate under various industrial conditions.
Chemical Composition Comparison
Element | D2 Tool Steel (1.2379) | A2 Tool Steel (1.2363) |
---|---|---|
Carbon (C) | 1.4 – 1.6% | 0.95 – 1.05% |
Chromium (Cr) | 11.0 – 13.0% | 4.75 – 5.5% |
Molybdenum (Mo) | 0.7 – 1.2% | 0.9 – 1.4% |
Vanadium (V) | 0.5 – 1.1% | 0.15 – 0.5% |
Silicon (Si) | 0.1 – 0.6% | 0.4 – 1.0% |
Manganese (Mn) | 0.1 – 0.6% | 0.03 max |
Phosphorus (P) | 0.03 max | 0.1 – 0.5% |
Sulfur (S) | 0.03 max | 0.03 max |
Mechanical Properties Overview
The mechanical properties of each tool steel influence their usability across different industrial processes. Below is a side-by-side comparison:
- D2 Tool Steel:
- Tensile Strength: ≥2000 MPa — Extremely high strength, ideal for wear-intensive applications
- Yield Strength: ≥1800 MPa — Maintains structural integrity under heavy loads
- Elongation: 11% — Modest flexibility, allowing some resilience to impact
- Impact Energy: 24 J — Decent resistance to sudden force
- A2 Tool Steel:
- Tensile Strength: 670-710 MPa — More suitable for medium-load applications
- Yield Strength: 345-350 MPa — Lower threshold for permanent deformation
- Elongation: 41% — Excellent flexibility, highly tolerant of bending and shock
- Impact Energy: 12 J — Moderate resistance to direct impacts
These values show that D2 is significantly harder and stronger, making it more durable in abrasive environments. In contrast, A2 offers superior flexibility and impact resistance, making it favorable for dynamic or high-impact applications.
Performance: Toughness vs Wear Resistance
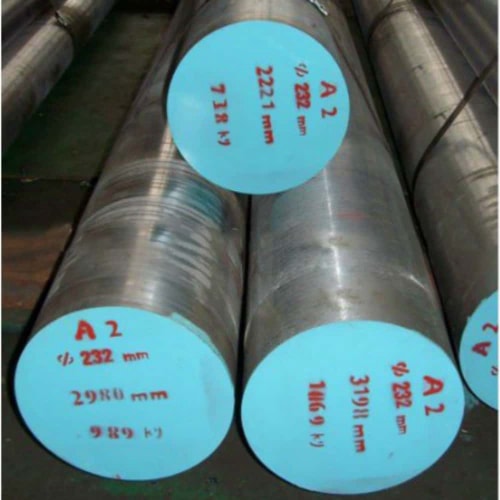
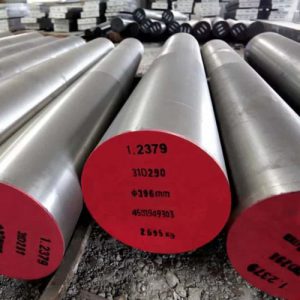
A2 Tool Steel Strengths
A2 tool steel is an air-hardening, cold-work tool steel that stands out for its high toughness and dimensional stability after heat treatment. Its composition allows it to perform admirably in scenarios where impact resistance and the ability to absorb shock are paramount. A2 is particularly valued for the following:
- Cold Forming Tools: It maintains structure even under repetitive deformation.
- Blades and Punches: Offers durability without fracturing when subjected to impact loads.
- Die-Casting Tools: Performs under high thermal and mechanical stress.
- Woodworking Tools: A2’s edge retention and toughness make it ideal for enduring abrasive hardwoods and repetitive motion.
Thanks to its ability to resist cracking and deformation, A2 is the preferred choice in applications where repeated impact and mechanical stress are the norm. It is also easier to machine than D2, reducing production time and tool wear during manufacturing.
D2 Tool Steel Advantages
In contrast, D2 steel is known for its superior hardness D2 steel, on the other hand, is a high-carbon, high-chromium tool steel with exceptional hardness and wear resistance. It is oil or air-hardened and holds a high level of compression strength. Notable for its ability to stay sharp, it thrives in high-production environments. Key uses include:
- Industrial Blades and Cutting Tools: Maintains a razor-sharp edge even with prolonged use.
- Stamping and Forming Dies: Exceptional durability in forming operations with high abrasiveness.
- Injection Molds: Withstands repeated exposure to hot, flowing plastic without deformation.
- Extrusion Dies: Resists stress and heat cycling over long runs.
- Food Processing Knives: D2’s corrosion resistance and edge durability make it suitable for hygienic, high-usage applications.
D2’s outstanding wear resistance is often unmatched in cold work tool steels. Though less tough than A2, it compensates with extended service life and low maintenance needs in abrasive environments.
Applications and Industry Use
Where A2 Tool Steel Excels
Due to its shock absorption capacity and machinability, A2 finds favor in industries that involve:
- Die Casting Tools: Its resilience against cracking and dimensional consistency at high temperatures make it invaluable in die casting.
- Stamping Dies: It retains shape and edge sharpness in high-speed stamping operations, especially on thin gauge metals.
- Cold Forming Tools: Performs well under the pressures of bending, shaping, and pressing operations.
- Woodworking Applications: Particularly effective in tools used for carving, turning, or cutting hardwoods and composites.
- General Tooling in Job Shops: Its versatility, ease of machining, and reduced risk of breakage make it the steel of choice for many custom fabricators.
Where D2 Tool Steel Dominates
D2’s high carbon and chromium content deliver superior edge retention and abrasion resistance, positioning it as a premium solution for:
- Cutting Tools: From shears to slitters, D2 holds a sharp edge even when cutting abrasive materials.
- Injection Molds: Offers long life and maintains accuracy despite thermal cycling in mold operations.
- Extrusion Dies: Endures heavy loads and long durations without deformation.
- Aerospace and Automotive Components: Excellent for tooling components requiring tight dimensional tolerances and surface finish.
- Industrial Food Processing: D2’s semi-stainless nature allows it to be used in food-grade applications while resisting acid-based corrosion.
Its lower machinability compared to A2 can be a drawback during manufacturing but is outweighed by reduced downtime and tooling replacement in long-term operations.
Customer Feedback and Use Cases
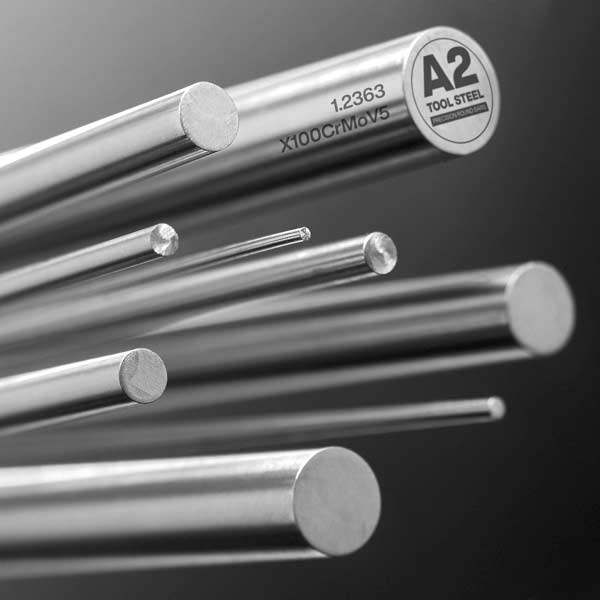
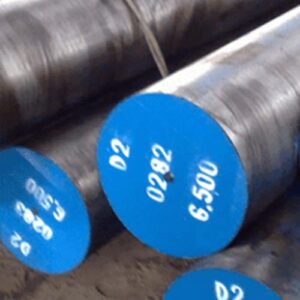
Testimonials for A2 Steel
- “Exceptional Toughness: Withstands heavy impacts and stresses without cracking.”
- “Dimensional Stability: Offers precise and consistent measurements post heat-treatment.”
- “Easy to Work With: Machines beautifully and saves tool life during fabrication.”
Testimonials for D2 Steel
- “Unbeatable Wear Resistance: Stays sharper for longer and minimizes tool change.”
- “Minimal Distortion: Excellent surface finish post hardening with low dimensional change.”
- “Perfect for High Volume: Our cutting tools last 3x longer with D2.”
Comparison Summary of D2 vs A2 Tool Steel
Strengths at a Glance
Feature | D2 Tool Steel | A2 Tool Steel |
Wear Resistance | Excellent | Good |
Toughness | Moderate | High |
Dimensional Stability | Good | Excellent |
Hardness | Very High | Moderate |
Edge Retention | Excellent | Good |
Heat Treat Distortion | Low | Very Low |
Ease of Machining | Moderate | Good |
Conclusion
The decision of choosing between d2 vs a2 tool steel in 2025 ultimately comes down to your application priorities. If your work requires extreme wear resistance and edge retention, D2 is your go-to option. However, if impact toughness, dimensional accuracy, and lower distortion during heat treatment are more critical, then A2 offers a better solution.
Each steel type brings a distinct advantage to the table, and many manufacturers often use both materials for different tools in the same production line. Always evaluate your operational conditions, production volume, and precision needs before making the final choice.
FAQ
What is the main difference between D2 and A2 tool steel?
The main difference lies in hardness vs toughness. D2 offers superior wear resistance and edge retention, while A2 is known for higher toughness and better impact resistance.
Is D2 tool steel more wear-resistant than A2?
Yes, D2 has significantly better wear resistance due to its higher carbon and chromium content.
Can A2 be used in high-impact applications?
Absolutely. A2 is specifically engineered for cold work applications that involve frequent impact and require high toughness.
Which steel is better for woodworking tools?
A2 tool steel is generally preferred for woodworking tools due to its toughness and ability to retain shape after multiple impacts.
Does D2 distort more during heat treatment?
While D2 exhibits low distortion, A2 has even better dimensional stability, making it ideal for high-precision tooling.
Is D2 harder to machine than A2?
Yes. D2’s higher hardness makes it tougher to machine, especially in its hardened state.
Which tool steel is more cost-effective?
A2 is often more cost-effective for medium-duty applications, while D2 justifies its cost in high-wear applications.
Can I use both D2 and A2 in the same project?
Yes. Many manufacturers use both steels strategically depending on the specific tool requirements in a project.
What industries commonly use D2 and A2?
D2 is widely used in aerospace, automotive, and metal forming, while A2 is common in die casting, woodworking, and general manufacturing.
Is one steel better for precision machining?
A2 is typically preferred in applications where high dimensional stability and precision are required after heat treatment.