Introduction
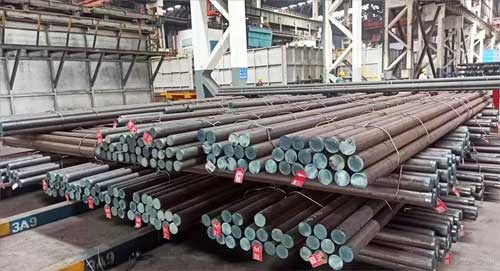
Tool steel is a crucial material in various industries, valued for its exceptional hardness, wear resistance, and toughness. However, selecting the right type of tool steel can be challenging due to the diverse range of options available. In this comprehensive guide, we’ll compare the properties of different tool steel types to help you make an informed decision.
Understanding Tool Steel:tool steel properties
Before diving into the intricacies of specific types of tool steel, it’s crucial to grasp the foundational properties that define this versatile alloy. Tool steel stands as a stalwart in various industries, revered for its remarkable ability to endure rigorous conditions while preserving its structural integrity. Let’s delve deeper into the fundamental properties that make tool steel indispensable in the world of manufacturing and engineering:
Hardness: At the core of tool steel’s resilience lies its exceptional hardness. This property denotes the material’s resistance to indentation, abrasion, and penetration under applied pressure. The hardness of tool steel is often measured on the Rockwell scale, with higher values indicating greater resistance to deformation. This characteristic ensures that tool steel can withstand the high stresses and abrasive forces encountered during machining, cutting, and forming operations.
Toughness: While hardness fortifies tool steel against wear and deformation, toughness complements this attribute by imbuing the material with resilience and durability. Toughness refers to the ability of a material to absorb energy and withstand sudden impacts or shocks without fracturing. In the realm of tooling, where tools are subjected to dynamic forces and mechanical stresses, toughness is paramount for preventing catastrophic failure and prolonging tool life.
Wear Resistance: Another critical property of tool steel is its wear resistance, which determines its ability to withstand surface degradation and erosion over time. As tools interact with workpieces and encounter abrasive materials, they are prone to wear, which can diminish their effectiveness and precision. Tool steel’s inherent wear resistance mitigates this degradation, ensuring prolonged tool life and consistent performance even in demanding machining environments.
Common Types of Tool Steel
There are several common types of tool steel, each with its unique properties and applications. These include:
A2 Tool Steel: Known for its excellent wear resistance and toughness, making it suitable for cold work applications such as cutting and forming dies.
D2 Tool Steel: Offers high hardness and abrasion resistance, ideal for applications requiring precision cutting and shaping.
M2 High-Speed Steel: Recognized for its superior hardness and heat resistance, making it suitable for cutting tools, drills, and taps.
S7 Tool Steel: Exhibits exceptional impact resistance and machinability, often used for forging dies and impact tools.
Comparative Analysis of Tool Steel Properties
To facilitate decision-making, let’s compare the properties of these four common types of tool steel:
Property | A2 Tool Steel | D2 Tool Steel | M2 High-Speed Steel | S7 Tool Steel |
---|---|---|---|---|
Hardness (HRC) | 60-62 | 58-62 | 60-65 | 54-60 |
Wear Resistance | High | High | High | Moderate |
Toughness | High | Moderate | Moderate | High |
Machinability | Fair | Poor | Fair | Excellent |
Heat Resistance | Moderate | Moderate | High | Moderate |
Factors to Consider in Selection
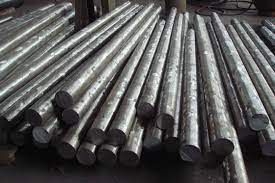
Certainly! When selecting the right tool steel for your needs, several factors need to be carefully considered to ensure optimal performance and longevity. Let’s explore these factors in more detail:
Application Requirements: Understand the specific requirements of your application, including the type of tooling operation (e.g., cutting, forming, stamping), the material being processed, and the desired precision and surface finish. Different tool steel grades are optimized for specific applications, so matching the steel’s properties to the application is crucial for achieving optimal results.
Operating Conditions: Evaluate the environmental conditions and stresses that the tool will be subjected to during operation. Consider factors such as temperature variations, abrasion, impact, and corrosion. Certain tool steel grades offer better resistance to these conditions, ensuring durability and performance under challenging operating environments.
Tool Life Expectancy: Determine the desired tool life expectancy for your application. Some tool steel grades are known for their exceptional wear resistance and longevity, while others may excel in toughness and impact resistance. By selecting a tool steel grade with the appropriate balance of hardness and toughness, you can maximize tool life and minimize the frequency of tool replacement or maintenance.
Machinability and Fabrication: Assess the machinability and ease of fabrication of the tool steel. Machinability refers to how easily the material can be machined, drilled, or shaped into the desired form. Factors such as hardness, alloy composition, and grain structure influence the machinability of tool steel. Choose a grade that offers good machinability while maintaining the desired mechanical properties for your application.
FAQ
Q: Can tool steel be welded?
A: Yes, some types of tool steel can be welded using appropriate welding techniques and procedures. However, not all tool steels are readily weldable, so it’s essential to consult with a metallurgical expert before attempting welding.
Q: What is the difference between tool steel and carbon steel?
A: While both tool steel and carbon steel are alloys of iron and carbon, tool steel contains additional alloying elements such as chromium, vanadium, or tungsten to enhance its properties, whereas carbon steel typically contains only carbon and iron.
Q: How can I improve the performance of tool steel?
A: Performance can be enhanced through proper heat treatment, surface treatments such as nitriding or coating, and selecting the appropriate grade of tool steel for your specific application requirements.
Conclusion
In conclusion, selecting the right tool steel involves a careful assessment of properties, applications, and operating conditions. By comparing the properties of different types of tool steel and considering factors such as hardness, wear resistance, toughness, and machinability, you can choose the type that best suits your needs and ensures optimal performance in your applications.