Introduction
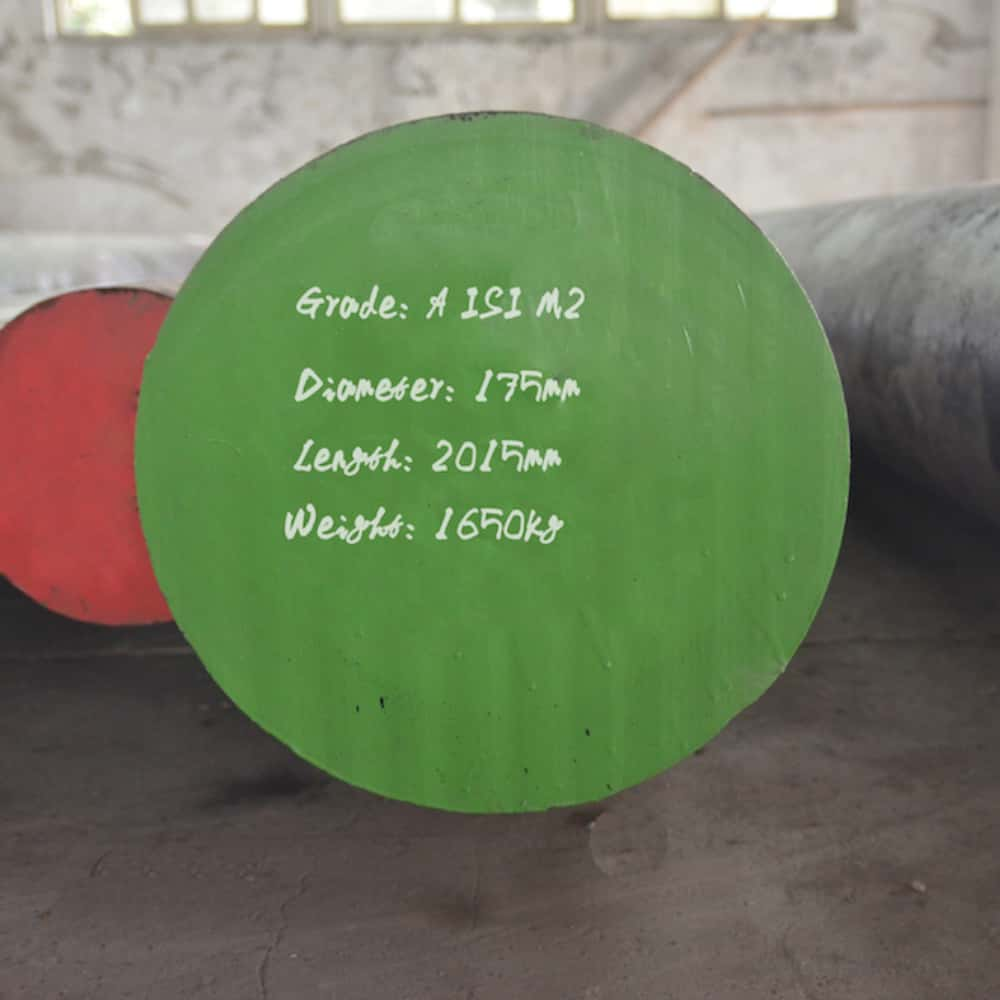
In the world of metallurgy, the hardening of tool steel is a fundamental process that profoundly impacts the performance and longevity of tools and components across various industries. This blog aims to delve deep into the intricacies of different tool steel hardening processes, examining their methods, advantages, disadvantages, and practical applications.
Understanding Tool Steel Hardening Process
Tool steel hardening involves transforming the microstructure of steel to enhance its hardness, strength, and wear resistance. This process is critical for tools used in cutting, shaping, and forming applications where durability and precision are paramount. The selection of the hardening method depends on factors such as the steel composition, desired properties, and the specific application requirements.
Types of Tool Steel
Tool steels are classified into several categories based on their alloy composition and intended use:
- High-Speed Steels (HSS): Known for their high hardness and heat resistance, ideal for cutting tools.
- Cold-Work Steels: Designed for applications involving cutting and forming at low temperatures.
- Hot-Work Steels: Resistant to heat and wear, suitable for operations at elevated temperatures.
- Plastic Mold Steels: Optimized for molding and forming plastic materials, requiring high hardness and polishability.
Each type of tool steel requires tailored tool steel hardening processes to achieve optimal performance characteristics.
Heat Treatment Fundamentals
Heat treatment is a crucial aspect of tool steel hardening, involving controlled heating, quenching, and tempering processes:
- Austenitizing: Heating the steel to a temperature where its microstructure becomes austenitic, allowing for the dissolution of carbides.
- Quenching: Rapidly cooling the steel in a medium such as oil, water, or air to achieve desired hardness.
- Tempering: Reheating the hardened steel to a lower temperature to improve toughness and reduce brittleness.
The choice of quenching medium significantly influences the final hardness, toughness, and dimensional stability of the tool steel.
Comparison of Tool Steel Hardening Processes
- Oil Quenching
- Process: Involves immersing heated steel into oil to control the cooling rate.
- Advantages: Provides a slower and more uniform cooling rate, reducing the risk of cracking and distortion. Suitable for large and complex-shaped components.
- Disadvantages: Slower cooling can lead to lower hardness compared to water quenching. Oil residues may require additional cleaning processes.
- Applications: Commonly used for tool steel grades requiring a balance between hardness and toughness, such as in aerospace and automotive applications.
- Water Quenching
- Process: Steel is quenched in water for rapid cooling.
- Advantages: Achieves high hardness quickly, cost-effective due to readily available quenching medium.
- Disadvantages: High cooling rates increase the risk of cracking and distortion, necessitating careful control and post-quenching treatments.
- Applications: Ideal for tool steels where maximum hardness and wear resistance are critical, such as in cutting tools and dies.
- Air Quenching
- Process: Allowing the steel to cool in still air after heating.
- Advantages: Minimizes distortion and cracking due to the slower cooling rate. Simple process requiring less equipment.
- Disadvantages: Limited hardening capability compared to oil or water quenching. Achieves lower hardness levels.
- Applications: Suitable for low alloy steels or components where extreme hardness is not required, such as in structural applications and low-load tools.
Case Studies and Practical Applications
To illustrate the effectiveness of different tool steel hardening processes, case studies from various industries provide insights into real-world applications:
- Automotive Manufacturing: High-speed and cold-work steels hardened using water quenching for precision cutting tools and dies.
- Aerospace Industry: Oil quenching used for heat-resistant alloys in turbine components and structural parts.
- Tool Production: Air quenching applied to low alloy steels for general-purpose tools and equipment.
Each case study demonstrates the tailored approach to selecting the optimal hardening process based on material requirements and performance criteria.
Experimental Results and Data Analysis
Experimental data, including hardness tests, microstructure analysis, and mechanical property evaluations, provide quantitative insights into the effects of different tool steel hardening processes on tool steel performance. These analyses help validate the suitability of each method for specific applications and inform process optimization strategies.
Comparative Analysis of Tool Steel Hardening Processes
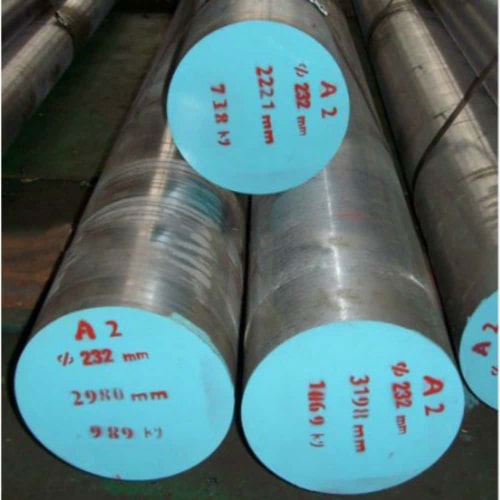
Tool Steel Hardening Process | Advantages | Disadvantages | Applications |
---|---|---|---|
Oil Quenching | Slower cooling rate reduces cracking, suitable for large parts | Lower hardness compared to water quenching, requires cleaning | Aerospace, automotive |
Water Quenching | Rapid high-hardness achievement, cost-effective | High risk of cracking, distortion | Cutting tools, dies |
Air Quenching | Minimal distortion, simple process | Limited hardening capability, lower hardness | Structural applications, low-load tools |
Conclusion
Selecting the appropriate tool steel hardening process is crucial for achieving desired mechanical properties and performance characteristics. While each method offers unique advantages and challenges, understanding their implications on steel microstructure and final product performance is essential for informed decision-making in industrial applications.
FAQ
Q:Which tool steel is best suited for oil quenching?
A:Oil quenching is effective for medium to high carbon steels and alloy steels where controlled cooling rates are critical to minimize cracking and distortion.
Q:How does water quenching affect tool steel properties?
A:Water quenching achieves maximum hardness quickly but requires careful control to prevent cracking and distortion, making it suitable for high-demand applications.
Q:Why choose air quenching over other methods?
A:Air quenching is preferred for its simplicity and minimal distortion effects, suitable for low alloy steels or components not requiring extreme hardness.