Welcome to My Blog! 🌟
Before we dive into the content, I’d love for you to join me on my social media platforms. It’s where I share more insights, engage with our vibrant community, and post regular updates. Here’s how you can stay connected:
📘 Facebook: Connect with me on Facebook
Now, let’s embark on this journey together. I hope you find the content here insightful, engaging, and most importantly, valuable. Let’s explore, learn, and grow together! 🚀
Table of Contents
Introduction
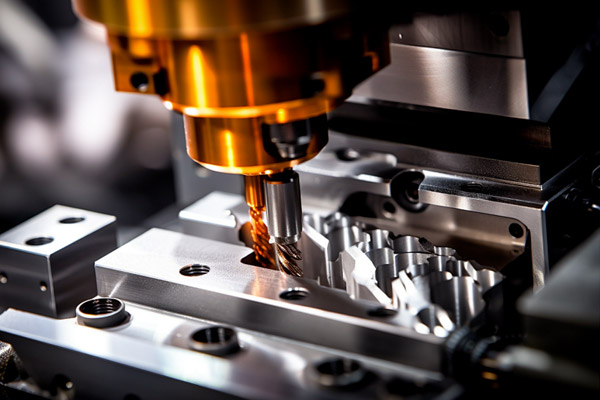
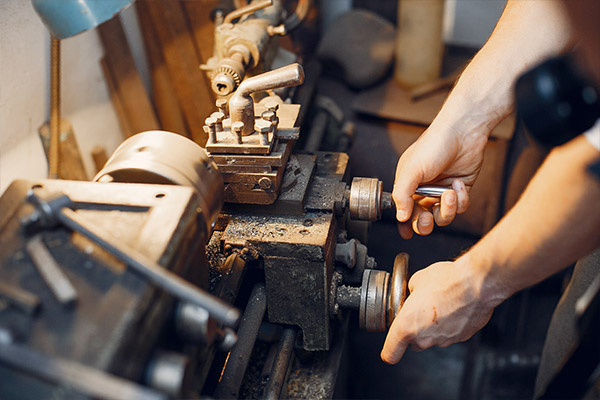
When it comes to selecting tool steels for manufacturing applications, the comparison between dc53 steel vs d2 is one that frequently arises among engineers and toolmakers. Both steels offer excellent performance characteristics, but understanding their key differences is essential for making the right material selection that will impact tool life, production efficiency, and overall costs.
At Shandong Qilu Industrial Co., Ltd., we have extensive experience supplying both dc53 and d2 steel to manufacturers across various industries. Through this article, we aim to provide a comprehensive yet straightforward comparison of these two popular tool steel grades to help you make informed decisions for your tooling applications.
NO 1. Composition and Metallurgy of DC53 vs D2 Steel
The fundamental differences between DC53 vs D2 Steel begin at the chemical composition level. In the DC53 vs D2 Steel comparison, D2 steel is classified as a high-carbon, high-chromium tool steel containing approximately 1.5% carbon and 12% chromium. This composition in the DC53 vs D2 Steel matchup gives D2 steel its characteristic hardness and wear resistance but also contributes to certain limitations in toughness.
When examining DC53 vs D2 Steel, DC53 represents an improved version of D2, with a modified chemical composition that includes slightly lower carbon content (around 1.0%) and chromium levels (about 8%), but with increased molybdenum content. This refined chemistry in the DC53 vs D2 Steel comparison results in a more balanced microstructure that maintains good wear resistance while significantly improving toughness compared to conventional D2 steel.
The metallurgical structure difference in DC53 vs D2 Steel shows that D2 contains large primary carbides that provide excellent wear resistance but can act as stress concentrators, making the material more prone to chipping under impact loading. DC53’s microstructure in the DC53 vs D2 Steel analysis features finer, more evenly distributed carbides due to its optimized composition, resulting in better toughness and fatigue resistance while still maintaining sufficient wear characteristics for most tooling applications.
NO 2. Hardness and Heat Treatment in DC53 vs D2 Steel
Both DC53 vs D2 Steel can achieve high surface hardness levels suitable for demanding tooling applications, but their responses to heat treatment differ in important ways. In the DC53 vs D2 Steel hardness comparison, D2 steel typically reaches levels between 58-62 HRC after proper heat treatment, while DC53 can achieve slightly higher hardness in the range of 60-63 HRC with greater stability.
The heat treatment process difference in DC53 vs D2 Steel shows that D2 requires careful control to avoid cracking and excessive distortion. The DC53 vs D2 Steel heat treatment comparison reveals D2 typically involves preheating at two intermediate temperatures (around 650°C and 850°C) before reaching the final hardening temperature between 1010-1030°C. The cooling process in DC53 vs D2 Steel must be carefully managed for D2, often using air cooling or salt baths to prevent thermal shock that could lead to cracking.
DC53 offers more forgiving heat treatment characteristics in the DC53 vs D2 Steel evaluation. It can be hardened at slightly higher temperatures (1020-1040°C) and shows better resistance to cracking during quenching. The DC53 vs D2 Steel analysis shows DC53’s refined carbide structure also results in lower distortion during heat treatment, which can be particularly beneficial for complex tool geometries where dimensional stability is critical.
At Qilu Tool Steel, we perform precise heat treatment processes for both DC53 vs D2 Steel grades to ensure optimal performance characteristics are achieved. Our controlled atmosphere furnaces and experienced metallurgists guarantee consistent results in DC53 vs D2 Steel processing that meet the exacting requirements of modern tooling applications. The DC53 vs D2 Steel comparison clearly shows DC53’s advantages in heat treatment stability and consistency.
NO 3. Toughness and Impact Resistance
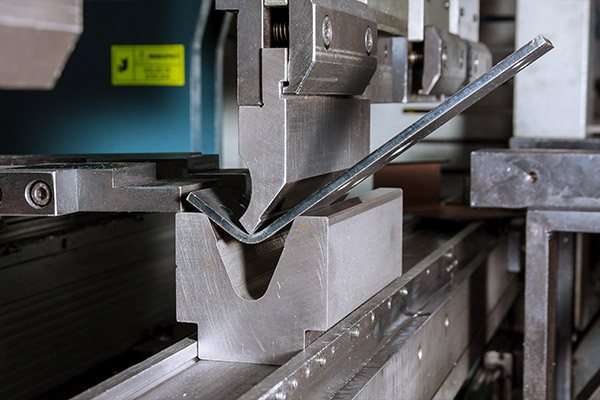
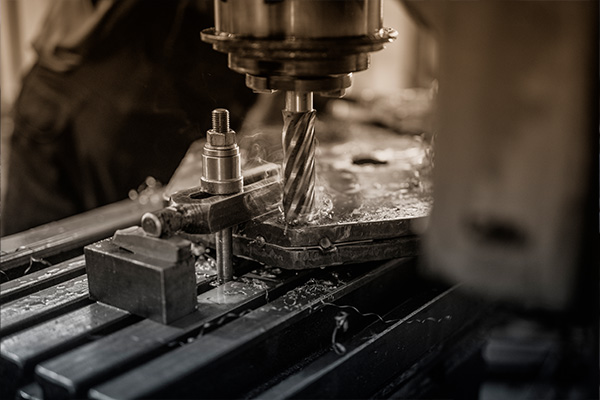
When evaluating dc53 steel vs d2 for applications involving impact or shock loading, toughness becomes a critical factor. Standardized Charpy impact tests consistently show dc53 steel outperforming d2 by a significant margin, with impact energy values typically 2-3 times higher than those of conventional d2 steel.
This superior toughness translates directly to improved performance in real-world tooling applications. Tools made from dc53 steel demonstrate significantly reduced chipping and cracking in demanding operations like punching, blanking, and forming. The enhanced toughness allows tools to withstand higher shock loads and provides better resistance to catastrophic failure in service.
D2 steel remains an excellent choice for applications where pure wear resistance is the primary requirement and impact loading is minimal. Its high hardness and wear characteristics make it well-suited for long-run stamping operations, blanking dies for thin materials, and applications involving abrasive wear without significant impact forces.
For manufacturers dealing with thicker materials, intermittent cutting operations, or applications where tools experience variable loading conditions, dc53 steel often provides better overall performance and longer tool life despite its slightly higher initial material cost. The reduced frequency of tool failures and associated production downtime can result in significant cost savings over the tool’s service life.
NO 4. Machinability and Grinding
The manufacturing process for tooling components involves various machining and grinding operations, where the differences between dc53 steel vs d2 become particularly noticeable. DC53’s refined microstructure provides distinct advantages in both machining and grinding compared to conventional d2 steel.
During machining operations, dc53 steel typically offers 20-30% better machinability than d2. This improved machinability manifests in several ways: reduced cutting forces, lower tool wear rates, better surface finish potential, and generally more stable machining conditions. These factors contribute to lower manufacturing costs and faster production times for dc53 tooling components.
D2 steel’s high carbide content and hardness make it more challenging to machine efficiently. Machining d2 requires rigid machine setups, appropriate cutting tool materials, and careful attention to cutting parameters to avoid excessive tool wear or workpiece damage. The heat generated during machining d2 can also be more difficult to manage, sometimes requiring special cutting fluids or reduced cutting speeds.
Grinding operations similarly benefit from dc53’s material characteristics. The steel allows for 15-20% faster grinding rates compared to d2, with reduced risk of grinding burns and better dimensional stability during the grinding process. Wheel wear is typically lower when grinding dc53, contributing to additional cost savings in tool manufacturing.
These machining and grinding advantages make dc53 particularly suitable for complex tool geometries or applications requiring precision ground surfaces. While the raw material cost of dc53 is higher than d2, the savings in manufacturing costs can often offset this difference, especially for intricate or high-precision tooling components.
NO 5. Cost Considerations and Applications
When making final material selection decisions between dc53 steel vs d2, cost considerations inevitably come into play. At first glance, d2 steel appears more economical with its lower initial material cost. However, a comprehensive evaluation should consider total cost of ownership, which includes factors like tool life, manufacturing costs, and production efficiency.
DC53 steel typically commands a 15-25% higher base price than d2, but this premium often proves justified in many applications. The combination of longer tool life, reduced machining costs, lower heat treatment expenses, and fewer production stoppages due to tool failures can result in significant overall savings. Manufacturers should carefully evaluate their specific application requirements to determine which steel provides the better value proposition.
In terms of application suitability, our experience at Qilu Tool Steel shows clear patterns for each material’s strengths. D2 steel excels in applications where maximum wear resistance is paramount and impact loading is minimal. This includes blanking dies for thin materials, long-run stamping tools, wear plates and guides, and cutting knives for non-metallic materials.
DC53 performs best in more demanding applications where toughness and impact resistance are critical. This includes high-impact punching dies, forming tools for thick materials, complex shaped tools, and applications requiring frequent regrinding. The steel’s balanced properties also make it well-suited for tools that experience variable loading conditions or intermittent use.
About Our Company
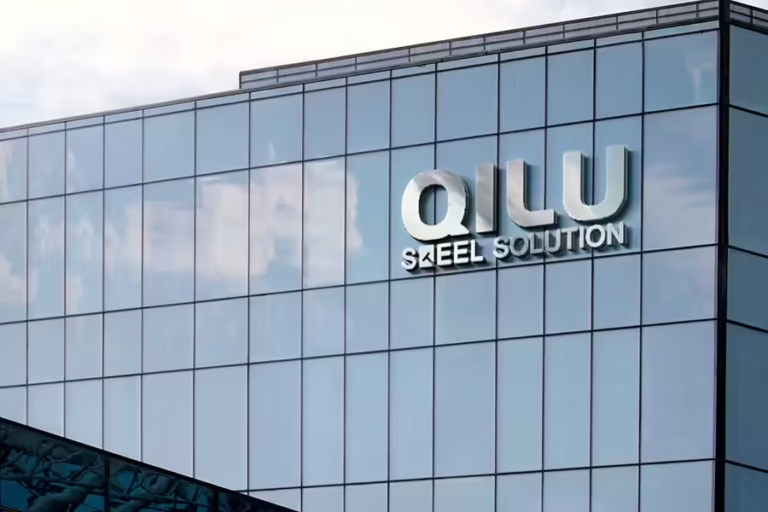
Shandong Qilu Industrial Co., Ltd. is a wholly-owned subsidiary of Qilu Steel Group, specializing in the production of high-quality tool steels. With our specialized factory and extensive industry experience, we’ve established ourselves as a leading supplier of tool and mold steels, including P20, H13, D2, DC53, and S7 grades.
Our vision is to be the world’s premier supplier of tool steels, helping customers succeed through superior product quality and innovative technology. We maintain strict quality control throughout our production processes and offer comprehensive technical support to ensure our materials perform as expected in your applications.
For more information about our products or assistance with material selection between dc53 steel vs d2, please don’t hesitate to contact our sales team. We’re committed to providing practical solutions that deliver maximum value for your manufacturing operations.
Conclusion
The choice between dc53 steel vs d2 ultimately depends on careful consideration of your specific application requirements. D2 steel remains the go-to choice for applications prioritizing maximum wear resistance where impact loading is not a significant factor. Its proven performance and lower initial cost make it a reliable option for many conventional tooling applications.
DC53 steel represents a significant advancement in tool steel technology, offering substantially improved toughness while maintaining sufficient wear characteristics for most applications. For manufacturers dealing with challenging forming operations, thick materials, or high-impact conditions, dc53 often provides better overall performance and cost-effectiveness despite its higher initial price.
At Shandong Qilu Industrial Co., Ltd., we supply both steel grades with guaranteed quality and performance. Our technical team can provide expert guidance to help you select the optimal material for your specific tooling requirements. We understand that material selection decisions have far-reaching implications for production efficiency and product quality, and we’re committed to helping our customers make informed choices.
FAQ
Can DC53 replace D2 in all applications?
While DC53 offers better toughness, D2 remains preferable for pure wear applications where impact resistance isn’t critical.
How does the corrosion resistance compare?
Both steels offer similar corrosion resistance due to their chromium content, though neither is considered stainless.
Which steel is better for plastic injection molds?
For most plastic mold applications, D2 is preferred for its wear resistance, though DC53 may be better for molds experiencing high stresses.
What about dimensional stability during heat treatment?
DC53 generally shows better dimensional stability with less distortion during heat treatment compared to D2.
Where can I get technical assistance in selecting between these steels?
Our technical team at Qilu Tool Steel is available to help you choose the right material for your specific application needs.