Welcome to My Blog! 🌟
Before we dive into the content, I’d love for you to join me on my social media platforms. It’s where I share more insights, engage with our vibrant community, and post regular updates. Here’s how you can stay connected:
📘 Facebook: Connect with me on Facebook
Now, let’s embark on this journey together. I hope you find the content here insightful, engaging, and most importantly, valuable. Let’s explore, learn, and grow together! 🚀
Table of Contents
Introduction
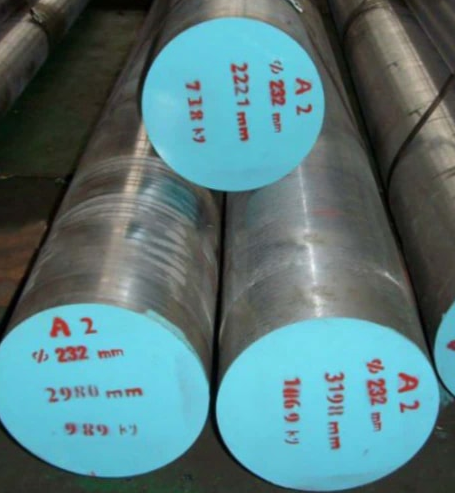
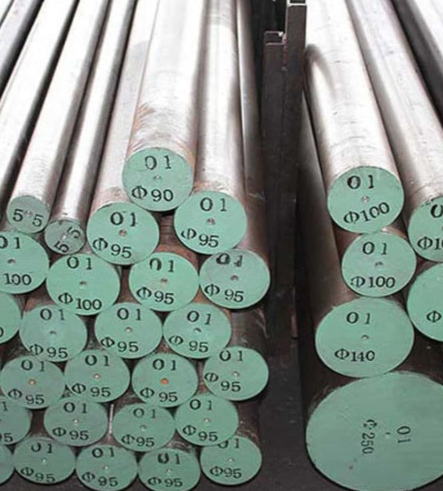
When it comes to tool steels, one of the most commonly asked questions among machinists, knife makers, and metalworkers is the difference between A2 vs O1 steel. These two high-performance steels serve similar purposes but come with distinct properties that make each better suited to different tasks. Whether you’re crafting a precision cutting instrument or a rugged workshop tool, understanding their strengths and limitations can save you time, money, and frustration.
In this comprehensive guide, we’ll explore everything you need to know about a2 vs o1 steel—covering their compositions, hardness, wear resistance, ease of sharpening, and more. We’ve also gathered expert tips that will help you make an informed decision based on your specific needs.
Understanding A2 and O1 Tool Steels
What Is A2 Steel?
A2 is an air-hardening, cold-work tool steel known for its toughness and dimensional stability. Due to its ability to harden in air and resist warping, it’s often used in applications requiring precision and durability. It contains higher chromium content compared to O1, which adds to its corrosion resistance and overall strength.
What Is O1 Steel?
O1, on the other hand, is an oil-hardening tool steel with excellent edge retention and wear resistance. It’s been a favorite in the knife-making community for decades due to its ease of sharpening and clean cuts. However, it requires oil quenching, which may lead to dimensional changes if not handled carefully.
Understanding these basics is essential to comparing a2 vs o1 steel and selecting the one that aligns with your work conditions and performance goals.
A2 vs O1 Steel: Key Differences That Matter
Now let’s look at a comparative overview of the two steels. The following table presents the core differences in performance and characteristics, helping clarify which applications they best serve.
Performance Comparison Table: A2 vs O1 Steel
Feature | A2 Steel | O1 Steel |
---|---|---|
Hardening Method | Air-hardened | Oil-hardened |
Wear Resistance | Moderate to High | High |
Toughness | Very High | Moderate to High |
Dimensional Stability | Excellent | Good |
Ease of Sharpening | Slightly Harder to Sharpen | Very Easy |
Edge Retention | Good | Excellent |
Corrosion Resistance | Better than O1 | Low |
Ideal Uses | Precision tools, dies, punches | Knives, chisels, hand tools |
Cost | Generally Higher | Generally Lower |
Availability | Widely Available | Widely Available |
Expert Tips on Choosing Between A2 and O1
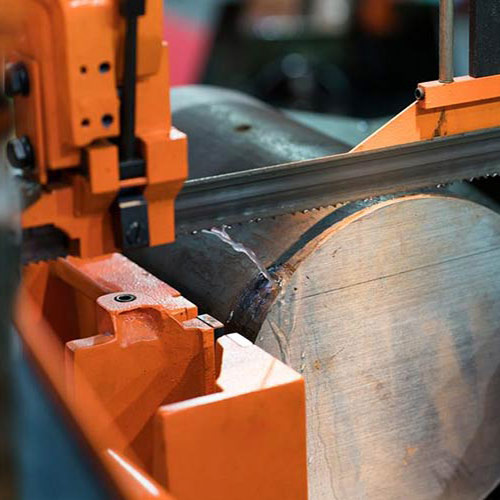
1. Match the Steel to Your Use Case
One of the first and most crucial steps in selecting the right tool steel is aligning your choice with its end-use. This is especially important in the case of a2 vs o1 steel, as their properties serve different functional roles. A2 steel is well-suited for high-impact applications such as punches, shears, stamping dies, and other tools that endure repetitive stress. Its exceptional toughness allows it to resist chipping and cracking, even under significant loads, making it ideal for industrial environments where reliability is paramount.
In contrast, O1 steel shines in applications requiring fine, precise edges. This includes woodworking chisels, straight razors, and culinary knives where sharpness and control are essential. For those who prioritize edge retention and a clean finish in their tools, O1 is often considered the go-to option in the a2 vs o1 steel debate.
Ultimately, the choice hinges on the function of your tool. If you need durability and strength under strain, A2 provides a long-lasting solution. If you’re crafting blades that demand razor-like sharpness, O1 delivers a cutting performance that’s hard to beat.
2. Factor in the Heat Treatment Process
Heat treatment plays a pivotal role in determining a tool’s mechanical properties, and understanding this aspect is key when comparing a2 vs o1 steel. A2 steel is air-hardened, which means it can cool in open air without the need for oil or water quenching. This feature minimizes the risk of warping or dimensional instability during the hardening process, which is especially important for precision tooling or parts that require tight tolerances.
O1 steel, however, must be quenched in oil to achieve proper hardness. While this allows for excellent edge retention and structural strength, it also introduces the risk of slight distortions if the process isn’t executed carefully. This makes O1 more sensitive to improper heat treatment setups, especially in amateur or home workshops.
If your manufacturing environment lacks the capability for controlled oil quenching, or if you’re working with parts that require minimal shape deviation, A2 might be the more practical choice in the context of a2 vs o1 steel.
3. Consider Edge Retention vs. Toughness
In the long-standing comparison of a2 vs o1 steel, the question often comes down to edge retention versus toughness. O1 steel is engineered to hold an extremely sharp edge, making it perfect for tools used in cutting, slicing, and fine detailing. Whether you’re sharpening wood by hand or preparing a delicate cut of meat, the fine grain structure of O1 helps maintain a razor-sharp edge for extended use.
On the other side, A2 is built to endure physical stress and harsh conditions. It may not hold an edge as long as O1 in low-stress applications, but its toughness enables it to withstand abuse that would damage other steels. This makes A2 a superior candidate for impact tools, where micro-fracturing or breakage is a concern.
Therefore, when choosing between a2 vs o1 steel, evaluate your priorities carefully. Do you need a blade that slices cleanly for hours on end, or a tool that can take a beating without failure?
4. Sharpening Tools and Skill Level
O1 is easier to sharpen, making it suitable for beginners or those who need to frequently maintain their edges without specialized equipment. A2 is a bit tougher to sharpen due to its hardness, but that also means it won’t dull as quickly during rugged use.
5. Evaluate Environmental Exposure
While neither A2 nor O1 is stainless, A2 contains more chromium, offering slightly better corrosion resistance. If your tools will be exposed to moisture or humid environments, A2 is a safer pick. Still, both steels should be regularly maintained and protected with oil or coatings.
Real-World Applications: Which One Performs Better?
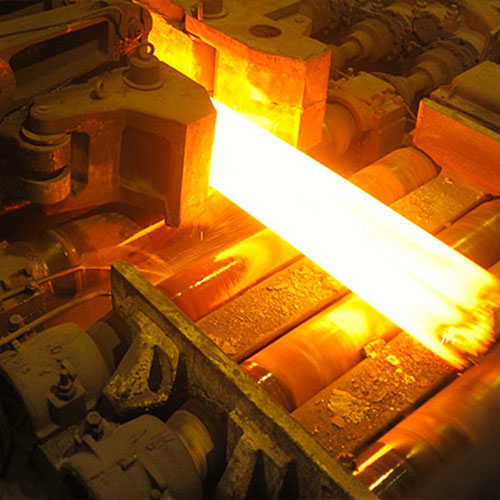
A2 Steel in Industrial Settings
When assessing real-world applications, the comparison of a2 vs o1 steel becomes especially relevant. These two tool steels perform differently depending on the task, and understanding these differences can help users make informed decisions for their specific industries and needs.
O1 Steel in Knife-Making and Woodworking
O1 steel’s sharpness and ease of honing make it a top-tier choice for knife makers, carpenters, and craftsmen. It has long been used for chef knives, bushcraft blades, and precision hand tools.
In the debate of a2 vs o1 steel, the application truly determines the winner.
Long-Term Maintenance and Cost Efficiency
Maintenance is another major point of difference. O1 steel, with its lower corrosion resistance, requires more upkeep—regular oiling, careful storage, and consistent sharpening.
A2 is more durable in the long run and can take more abuse without the need for frequent maintenance, making it more cost-effective in industrial or high-wear settings.
Ultimately, the choice between a2 vs o1 steel in terms of maintenance and cost depends on your specific priorities—whether you value ease of upkeep, long-term durability, or initial affordability.
Conclusion
When selecting between a2 vs o1 steel, the best choice depends on your priorities. If you need a tough, stable, and durable material for high-impact applications, A2 is likely the better option. If sharpness, edge retention, and easy sharpening are essential, O1 might be your go-to.
Both steels offer excellent performance when used correctly. Understanding their unique properties allows you to align your tool steel with your specific needs—whether you’re a machinist, craftsman, or knife maker.
FAQ
What is the main difference between A2 and O1 steel?
The biggest difference lies in their hardening methods and toughness. A2 is air-hardened and offers better toughness, while O1 is oil-hardened with superior edge retention and easier sharpening.
Which steel is better for knife making?
O1 steel is often preferred for knives due to its ability to hold a sharp edge and easy maintenance. However, some knife makers still choose A2 for its toughness in bushcraft or heavy-duty knives.
Does A2 steel rust less than O1?
Yes, A2 has slightly better corrosion resistance due to its higher chromium content, but both are not stainless and require protective care.
Is it easier to heat treat O1 or A2?
O1 is generally easier to heat treat at home due to its oil-hardening process. A2 may require more controlled heat and air cooling.
Can I sharpen A2 steel as easily as O1?
Not quite. A2 is harder, so it takes more time and effort to sharpen, especially if you’re using manual sharpening tools.
Which one lasts longer in industrial use?
A2 often outlasts O1 in heavy-duty, high-impact environments thanks to its toughness and resistance to wear and cracking.