Introduction
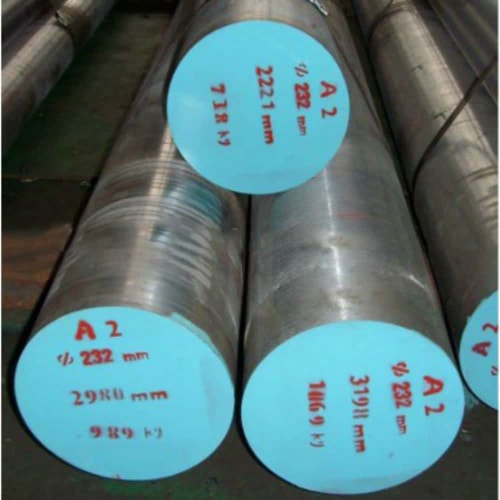
A2 steel hardness is a key property that makes this steel alloy a popular choice for various industrial applications, particularly in the manufacturing of cutting tools and dies. Its exceptional hardness, a result of its unique chemical composition and heat treatment processes, makes it a reliable and durable material. This guide will delve deep into the world of A2 steel hardness, exploring its properties, applications, and the factors that influence its hardness. By the end of this comprehensive guide, you will have a thorough understanding of what makes A2 steel so hard and why it is so widely used.
Understanding A2 Steel
A2 steel is classified as an air-hardening, high-carbon, high-chromium tool steel. This specific combination of elements gives it a remarkable balance of hardness, toughness, and wear resistance. Let’s break down the key alloying elements that contribute to these properties:
- Carbon: The high carbon content is a primary factor in A2 steel hardness and wear resistance. Carbon atoms form strong bonds with iron atoms in the steel’s microstructure, increasing its resistance to deformation. The carbon content typically ranges from 0.85% to 1.00%.
- Chromium: Chromium enhances the steel’s corrosion resistance and contributes to its hardening ability. It forms chromium carbides, which further strengthen the steel’s microstructure. Chromium also improves the steel’s resistance to oxidation at high temperatures. The chromium content in A2 steel is typically around 5%.
- Molybdenum and Vanadium: These elements are added to improve the steel’s toughness and red hardness. Molybdenum enhances the steel’s hardenability, allowing it to achieve a uniform A2 steel hardness throughout its cross-section, even in large sections. Vanadium refines the grain structure of the steel, improving its toughness and resistance to impact. The molybdenum content in A2 steel is typically around 1%, and the vanadium content is around 0.2%.
Heat Treatment and A2 Steel Hardness
The heat treatment process is crucial in determining the final A2 steel hardness. The most common heat treatment for A2 steel involves two primary steps:
- Austenitizing: In this step, the steel is heated to a specific temperature, typically between 1450°F and 1550°F (788°C and 843°C), to form austenite, a single-phase, face-centered cubic structure. Austenitizing allows the alloying elements to dissolve uniformly into the iron matrix. During this process, the steel is heated in a furnace until it reaches the desired temperature. Once the desired temperature is reached, the steel is held at that temperature for a specific period of time to allow the austenite to form completely.
- Quenching: After austenitizing, the steel is rapidly cooled, usually in oil or water, to transform the austenite into martensite. Martensite is a hard and brittle phase that forms when the carbon atoms are trapped in the iron lattice during rapid cooling. The rapid cooling rate prevents the carbon atoms from diffusing out of the iron lattice, resulting in a supersaturated solid solution. This supersaturated solid solution is highly strained, which contributes to the high A2 steel hardness of martensite.
The hardness of the final product can be further adjusted through a process called tempering. Tempering involves reheating the quenched steel to a lower temperature, typically between 300°F and 1200°F (149°C and 649°C), to relieve some of the internal stresses and improve its toughness. During tempering, the martensite undergoes a phase transformation, resulting in the formation of tempered martensite, which is less brittle but still retains a significant amount of A2 steel hardness.
Hardness Testing and A2 Steel Hardness
The A2 steel hardness is typically measured using the Rockwell hardness test. This test involves indenting the steel’s surface with a diamond cone or steel ball and measuring the depth of the indentation. The resulting number is the Rockwell hardness value, expressed in HRC (Rockwell C scale). A higher HRC value indicates greater A2 steel hardness.
Typical Rockwell Hardness Values for A2 Steel
Heat Treatment | Rockwell Hardness (HRC) |
---|---|
As-quenched | 62-64 |
Tempered at 400°F | 58-60 |
Tempered at 600°F | 55-57 |
Factors Affecting A2 Steel Hardness
Several factors can influence the final A2 steel hardness:
- Carbon content: As mentioned earlier, higher carbon content generally results in greater A2 steel hardness. However, excessive carbon can also make the steel more brittle. The optimal carbon content for A2 steel is typically around 1%.
- Alloying elements: The specific alloying elements and their concentrations can significantly affect the A2 steel hardness and other properties of the steel. For example, chromium and molybdenum contribute to the steel’s hardenability and wear resistance. Vanadium refines the grain structure of the steel, improving its toughness and resistance to impact.
- Cooling rate: A faster cooling rate during quenching produces a harder martensite structure. Oil quenching is typically used for A2 steel to achieve optimal A2 steel hardness. Water quenching can be used for smaller sections, but it can lead to distortion and cracking.
- Tempering temperature: The tempering temperature determines the balance between A2 steel hardness and toughness. Higher tempering temperatures reduce A2 steel hardness but improve toughness.
Applications of A2 Steel Hardness
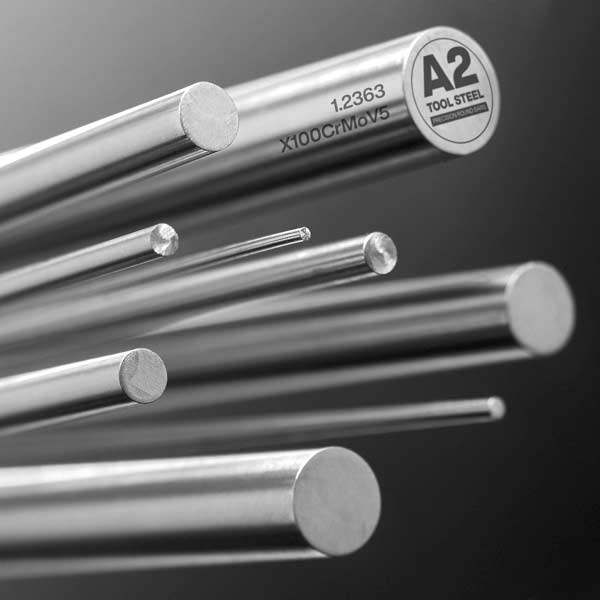
Due to its exceptional A2 steel hardness and wear resistance, A2 steel is widely used in various applications, including:
- Cutting tools: Drills, reamers, taps, and milling cutters made from A2 steel can withstand high loads and maintain sharp cutting edges for extended periods. These tools are used in a variety of industries, including automotive, aerospace, and manufacturing.
- Dies: Stamping dies, drawing dies, and forging dies made from A2 steel can withstand high pressures and temperatures without deformation or cracking. These dies are used to shape metal parts into various shapes and sizes.
- Molds: Injection molds and die casting molds made from A2 steel can produce high-quality parts with precise dimensions and smooth surfaces. These molds are used to create plastic and metal parts for a wide range of products.
- Bearings: Roller bearings and ball bearings made from A2 steel can handle heavy loads and high speeds with minimal wear. These bearings are used in a variety of applications, including automotive, aerospace, and industrial machinery.
Conclusion
A2 steel is a versatile and high-performance tool steel that is prized for its exceptional A2 steel hardness, toughness, and wear resistance. By understanding the factors that influence its hardness and the various heat treatment processes involved, you can select the appropriate A2 steel grade for your specific application.
FAQ
What is A2 steel?
A2 steel is a type of tool steel known for its exceptional hardness and wear resistance. It’s commonly used in manufacturing cutting tools and dies.
Why is A2 steel so hard?
A2 steel’s hardness is primarily due to its high carbon content and specific heat treatment processes. The carbon content contributes to the formation of hard carbides, while heat treatment processes like quenching and tempering further enhance hardness.
How is A2 steel hardened?
A2 steel is hardened through a process called heat treatment. This involves heating the steel to a high temperature, followed by rapid cooling (quenching) and then tempering to relieve internal stresses and improve toughness.
Can A2 steel be welded?
While A2 steel can be welded, it requires specialized welding techniques and post-weld heat treatment to maintain its hardness and prevent cracking. It’s generally recommended to use welding methods like TIG or MIG welding with appropriate filler metals.