Welcome to My Blog!
Before we dive into the content, I’d love for you to join me on my social media platforms where I share more insights, engage with the community, and post updates. Here’s how you can connect with me:
Facebook:https://www.facebook.com/profile.php?id=100087990137347
LinkedIn:https://www.linkedin.com/company/89825762/admin/dashboard/
YouTube:www.youtube.com/@carbonsteelsupply-kj9lw
TikTok:www.tiktok.com/@carbonsteelsupply
Now, let’s get started on our journey together. I hope you find the content here insightful, engaging, and valuable.
Introduction
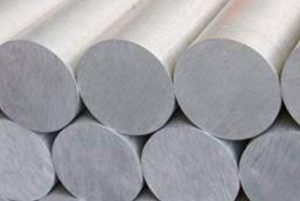
Tool steel A11 is renowned for its exceptional wear resistance and toughness, making it one of the most sought-after materials in demanding industrial applications. This premium, high-alloy steel is specifically engineered to withstand extreme conditions and maintain durability even under high-stress environments. In this blog post, we will dive deep into the properties, applications, and advantages of tool steel A11, providing valuable insights into why this material is so widely used. Whether you are involved in manufacturing, machining, or tool making, understanding1 tool steel A1 is essential for optimizing performance and longevity in your tools.
What is A11 Tool Steel?
Tool steel A11 is a high-alloy, air-hardening steel that belongs to the family of cold work steels. It contains significant amounts of vanadium, molybdenum, and chromium, which give it superior wear resistance, hardness, and toughness. A11 tool steel is particularly known for its ability to resist abrasion, making it ideal for tooling and machining applications where surface wear and tear are a concern.
Key Composition of A11 Tool Steel
- Carbon (C): 2.45%
- Vanadium (V): 9.75%
- Molybdenum (Mo): 1.30%
- Chromium (Cr): 5.25%
- Other elements: Small amounts of tungsten, manganese, and silicon
This unique composition results in tool steel A11 being an extremely wear-resistant material, particularly suitable for high-performance cutting, shaping, and molding tools.
Properties of A11 Tool Steel
Tool steel A11 is known for its impressive mechanical properties, which make it ideal for a variety of applications. Below are some of its most notable characteristics:
Wear Resistance
Tool steel A11 stands out for its superior wear resistance. The high vanadium content contributes to the formation of vanadium carbides, which are extremely hard and provide excellent protection against abrasive wear.
Toughness
Despite its high hardness, A11 tool steel exhibits good toughness, allowing it to endure high-impact applications without fracturing or chipping. This toughness makes it a versatile material for tools that encounter extreme forces.
Hardness
Tool steel A11 can achieve hardness levels in the range of 60-65 HRC after heat treatment, making it one of the hardest cold work steels available. This high hardness translates into prolonged tool life and reduced downtime for replacements.
Dimensional Stability
When heat-treated correctly, A11 tool steel offers excellent dimensional stability, ensuring that tools retain their shape and precision even after long-term use under extreme conditions.
Heat Treatment of A11 Tool Steel
The performance of A11 tool steel largely depends on proper heat treatment, which enhances its hardness, toughness, and wear resistance. The heat treatment process for A11 tool steel typically involves the following steps:
Preheating
Preheat the steel in two stages—first at 900°F (480°C) and then at 1450°F (790°C) to relieve internal stresses.
Austenitizing
Heat the steel to 1875-1950°F (1025-1065°C) for austenitizing. The steel is held at this temperature until it reaches uniformity throughout its structure.
Quenching
Tool steel A11 is air-quenched, allowing it to cool at room temperature. For certain applications, quenching in an inert gas or oil may be preferred.
Tempering
Temper the steel at 1000°F (540°C) to 1050°F (565°C) to achieve the desired balance between hardness and toughness. Multiple tempering cycles are often recommended to ensure optimum properties.
Proper heat treatment is essential for unlocking the full potential of A11 tool steel and ensuring that the material performs at its best.
Applications of A11 Tool Steel
Tool steel A11 is widely used in industries where high wear resistance, toughness, and longevity are essential. Some of the most common applications of A11 tool steel include:
Cutting Tools
Tool steel A11’s wear resistance and hardness make it an excellent choice for manufacturing cutting tools such as shears, punches, and industrial blades. These tools benefit from the steel’s ability to retain sharpness and resist wear over extended use.
Mold and Die Casting
In mold-making and die-casting applications, A11 tool steel is highly valued for its ability to withstand repeated cycles of molding without deformation or wear. Its toughness ensures that molds maintain their precision even after extended use in high-stress environments.
Extrusion Tools
Extrusion tools, especially those used in metalworking and plastics industries, require materials that can endure extreme forces and temperatures. A11 tool steel’s resistance to wear and thermal stress makes it ideal for this application.
Powder Compaction Dies
Tool steel A11 is commonly used in powder metallurgy applications for making powder compaction dies. The steel’s wear resistance allows these dies to maintain dimensional accuracy even after compressing large quantities of abrasive powder materials.
Forming Tools
Forming tools, such as bending and stamping dies, benefit from A11 tool steel’s combination of wear resistance and toughness, which allows them to handle the stresses involved in forming metal and other hard materials.
Advantages of A11 Tool Steel
The following table highlights some of the key advantages of using A11 tool steel in various industrial applications:
Advantage | Description |
---|---|
High Wear Resistance | Excellent resistance to abrasive wear, reducing the need for frequent tool replacement. |
Superior Toughness | Good toughness allows the steel to withstand high-impact forces without breaking. |
Longer Tool Life | Tools made from A11 tool steel last longer due to their durability and resistance to wear. |
Reduced Downtime | Fewer tool replacements mean less downtime for maintenance, improving productivity. |
Consistent Performance | A11 tool steel maintains its performance over time, ensuring consistent results. |
Heat Resistance | The steel’s ability to retain hardness at high temperatures makes it suitable for thermal applications. |
A11 Tool Steel vs Other Cold Work Steels
While A11 tool steel is often compared with other cold work tool steels such as D2 and M2, it offers unique advantages in terms of wear resistance and longevity. Here are some key differences:
- Wear Resistance: A11 tool steel provides superior wear resistance compared to D2 and M2, making it ideal for applications that involve constant abrasion.
- Toughness: A11 tool steel offers a balance between hardness and toughness, whereas some other cold work steels may be either too brittle or too soft for demanding applications.
- Application-Specific Benefits: While D2 is known for its machinability, A11’s outstanding wear resistance gives it an edge in applications where longevity is crucial.
Conclusion
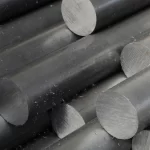
Tool steel A11 is a high-performance material that excels in applications requiring exceptional wear resistance and toughness. Its versatility across industries—from cutting tools to die-casting—demonstrates its value as a reliable and durable tool steel. Proper heat treatment unlocks its full potential, making it a top choice for demanding industrial environments. Understanding the properties, applications, and advantages of A11 tool steel can help you make informed decisions when selecting materials for your tooling needs.
FAQ
1. What makes A11 tool steel different from other tool steels?
Tool steel A11 stands out due to its high vanadium content, which provides superior wear resistance compared to many other tool steels like D2 or M2. It also balances toughness and hardness better than most, making it ideal for high-wear applications.
2. Can A11 tool steel be used for knife-making?
Yes, tool steel A11 can be used for knife-making, especially for knives designed for heavy-duty use, as it offers excellent edge retention and abrasion resistance.
3. What industries commonly use A11 tool steel?
Tool steel A11 is used across a variety of industries, including metalworking, plastic molding, powder metallurgy, and automotive sectors where high wear resistance is needed.
4. How does the heat treatment process affect A11 tool steel?
Proper heat treatment enhances A11 tool steel’s hardness, toughness, and wear resistance, ensuring the material performs optimally in demanding applications.
5. Is A11 tool steel easy to machine?
Due to its high hardness and wear resistance, A11 tool steel can be more challenging to machine than lower alloy steels. However, it can still be machined effectively with the right equipment and cutting conditions.