Introduction
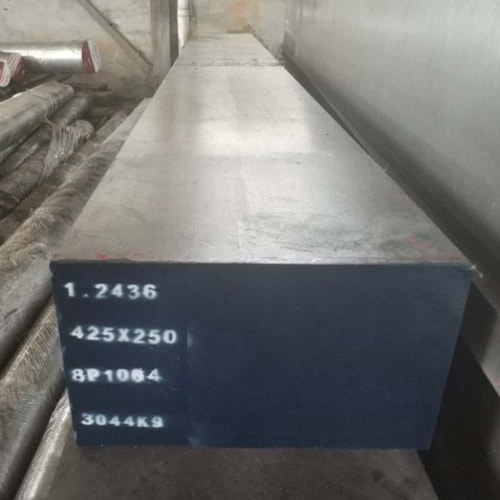
In the dynamic world of manufacturing and industrial applications, the choice of tool steel holds paramount importance. Tool steels are engineered to withstand extreme conditions such as high temperatures, heavy loads, and abrasive environments. Understanding tool steel specifications enables engineers and designers to select materials that meet specific performance criteria, ensuring optimal tool performance and longevity.
Tool Steel Composition
Tool steels are alloyed with various elements to achieve specific mechanical and physical properties. The composition of tool steels typically includes elements such as carbon, chromium, vanadium, molybdenum, and tungsten. These elements play crucial roles in determining the hardness, toughness, wear resistance, and heat resistance of the steel.
For example, H13 tool steel is renowned for its excellent combination of hardness, toughness, and heat resistance due to its composition of approximately 5% chromium, 1.5% molybdenum, and 1% vanadium. On the other hand, D2 tool steel, with its high chromium content (12%) and moderate amounts of molybdenum and vanadium, excels in wear resistance and dimensional stability, making it ideal for cutting tools and dies.
The following table illustrates the compositions and corresponding properties of some commonly used tool steels:
Steel Type | Composition | Properties |
---|---|---|
H13 | 5% Cr, 1.5% Mo, 1% V | High toughness, hot hardness |
D2 | 12% Cr, 1% Mo, 1% V | Excellent wear resistance |
M2 | 0.85% C, 4.2% Cr, 5% Mo, 6.5% W | High-speed cutting tools |
Understanding these compositions helps engineers select the right tool steel for specific applications, balancing performance requirements with cost considerations.
Tool Steel Specifications
Tool steel specifications encompass a range of parameters crucial for performance evaluation and material selection. These specifications are standardized by organizations such as ASTM (American Society for Testing and Materials) and AISI (American Iron and Steel Institute), ensuring consistency and reliability in material properties. Key specifications include:
- Hardness: Typically measured on the Rockwell C scale (HRC), hardness indicates the steel’s resistance to deformation and wear.
- Toughness: The ability of the steel to absorb energy and withstand shock without fracturing.
- Dimensional Stability: Minimal changes in size or shape under varying temperature and stress conditions.
- Machinability: Ease of shaping and forming the steel without excessive wear on cutting tools.
For instance, tool steels used for high-speed cutting tools like M2 are characterized by high hardness (up to 65 HRC) and excellent wear resistance, allowing for prolonged tool life and enhanced productivity in machining operations.
Applications of Tool Steels
Tool steels find extensive applications across various industries, including automotive, aerospace, mold-making, and general manufacturing. Their specific properties make them suitable for critical components such as:
- Cutting Tools: Drill bits, end mills, and taps.
- Molds and Dies: Injection molds, forging dies, and extrusion tools.
- Tooling Components: Punches, chisels, and gauges.
Each application demands specific properties from the tool steel, such as high wear resistance for cutting tools or excellent polishability for molds and dies. Selecting the right tool steel ensures optimal performance, durability, and cost-effectiveness in production processes.
Selection Considerations
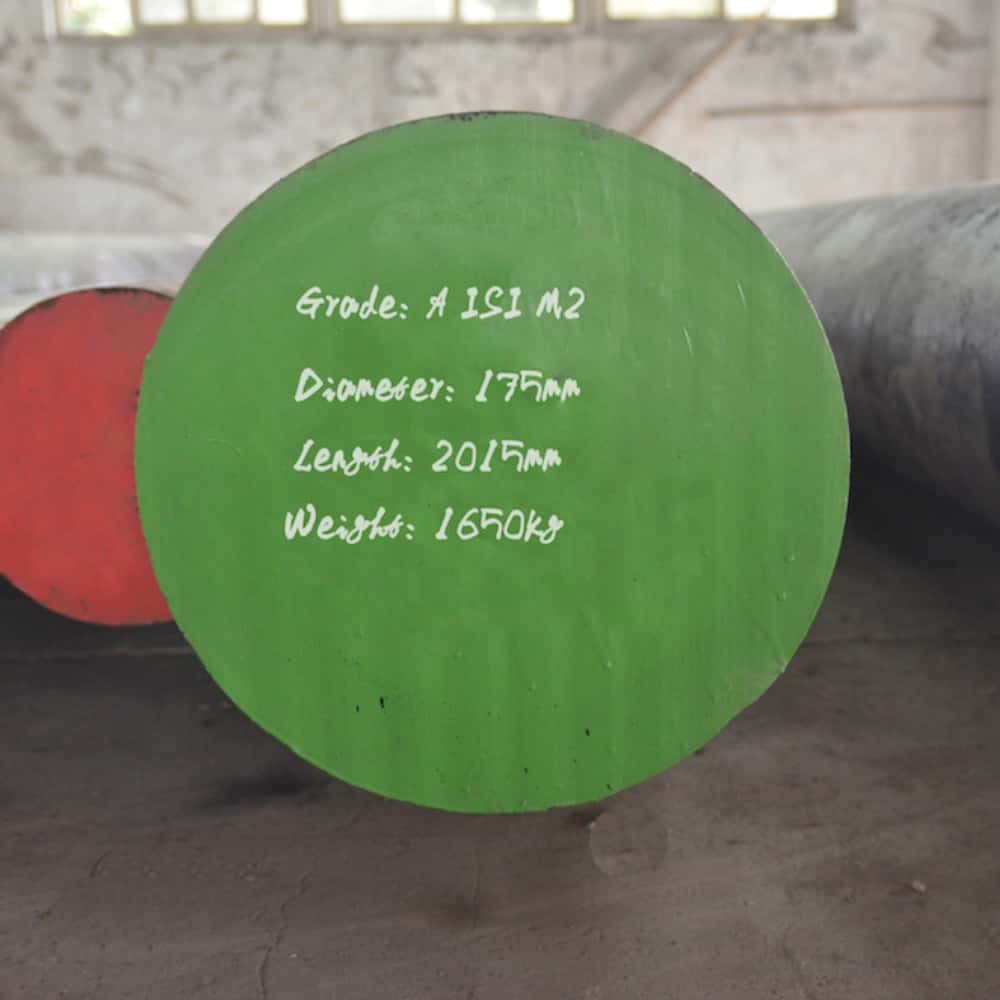
Choosing the appropriate tool steel involves a thorough evaluation of operational factors and performance requirements:
- Operating Conditions: Consider temperature variations, exposure to chemicals, and mechanical stresses.
- Production Volume: Evaluate batch sizes, production frequency, and tool life expectations.
- Cost and Availability: Balance material costs with long-term performance benefits and availability.
By carefully weighing these considerations, engineers and designers can make informed decisions that maximize tool performance and minimize operational downtime.
Conclusion
Tool steel specifications are a cornerstone of modern manufacturing, influencing the performance and longevity of tools and components across diverse industries. By understanding the nuances of tool steel composition, specifications, and applications, professionals can optimize material selection to meet specific project requirements effectively. This comprehensive guide serves as a valuable resource in navigating the complexities of tool steel selection and application.
FAQ
Q: What role does carbon play in tool steel composition?
A: Carbon content significantly influences hardness and wear resistance in tool steels. Higher carbon content generally increases hardness but may reduce toughness.
Q: How can I determine the optimal hardness for a tool steel?
A: The optimal hardness depends on the specific application and operational conditions. Conducting hardness tests and consulting with materials experts can help determine the suitable hardness level.
Q: Are environmental factors important when selecting tool steels?
A: Yes, environmental considerations such as corrosion resistance and stability in varying temperatures are crucial for long-term tool performance. Choose tool steels with appropriate alloying elements to meet environmental challenges.