Die casting is a manufacturing process that demands precision, durability, and the ability to withstand extreme heat and pressure. At the heart of this intricate process lies the choice of material, and one material that consistently stands out for its exceptional properties is hot work tool steel. In this comprehensive article, we will explore why hot work tool steel is a crucial material for die casting, delving deep into its composition, properties, applications, and the advantages it brings to this critical manufacturing technique.
1. Introduction
Die casting is a manufacturing process known for its precision and efficiency in producing complex, high-quality parts. Choosing the right material for the die casting molds and tooling is paramount, as it directly impacts the outcome of the process. Hot work tool steel has emerged as a top choice in die casting for its unique set of properties.
2. Hot Work Tool Steel: An Overview
Composition and Alloying Elements
Hot work tool steel is meticulously engineered with a blend of alloying elements, including chromium, tungsten, molybdenum, and vanadium. These elements bestow specific characteristics upon the steel, with heat resistance being a primary focus.
Heat Resistance: The Cornerstone of Its Utility
The exceptional heat resistance of hot work tool steel allows it to maintain its structural integrity even at temperatures exceeding 600°C (1112°F). This property is essential for die casting applications where extreme heat is generated.
3. The Die Casting Process
Understanding the Intricacies of Die Casting
Die casting involves injecting molten metal into a mold cavity under high pressure to create intricate, detailed parts. The precision and speed of this process make it a cornerstone in industries such as automotive, aerospace, and electronics.
Role of Hot Work Tool Steel in Die Casting
Hot work tool steel is used to create the molds and tooling required for die casting. Its ability to withstand the extreme temperatures and pressures of the process ensures that the molds maintain their shape, precision, and durability.
4. Advantages of Hot Work Tool Steel in Die Casting
Exceptional Heat Resistance
The primary advantage of hot work tool steel in die casting is its ability to endure the intense heat generated during the process. This heat resistance prevents softening or deformation of the molds, ensuring consistent part quality.
Wear and Abrasion Resistance
Hot work tool steel offers excellent wear and abrasion resistance, increasing the longevity of the molds and tooling. This durability translates to cost savings and reduced downtime for maintenance.
Dimensional Stability
Die casting requires high precision, and hot work tool steel’s dimensional stability ensures that the molds maintain the exact specifications needed for accurate part production.
Extended Tool Life
The wear resistance and heat resistance of hot work tool steel extend the lifespan of the molds and tooling, reducing the need for frequent replacements and enhancing overall efficiency.
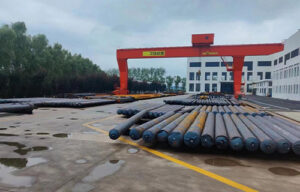
5. Applications of Hot Work Tool Steel in Die Casting
Automotive Industry
Die casting is widely used in the automotive sector for manufacturing components such as engine blocks, transmission cases, and structural parts. Hot work tool steel ensures the precision and durability of these critical components.
Aerospace Sector
In aerospace manufacturing, precision and reliability are paramount. Hot work tool steel is used to create molds for producing intricate aerospace components with exceptional heat resistance.
Consumer Electronics
The consumer electronics industry relies on die casting for producing components like smartphone casings and computer parts. Hot work tool steel ensures the high precision and durability required for these applications.
Medical Devices
Precision and hygiene are essential in the medical device industry. Hot work tool steel molds enable the production of intricate and reliable medical components.
6. Challenges and Solutions
Heat-Related Challenges in Die Casting
Die casting generates substantial heat, which can lead to material softening, mold deformation, and reduced tool life. These challenges can result in production delays and increased costs.
How Hot Work Tool Steel Addresses These Challenges
Hot work tool steel addresses heat-related challenges by maintaining its structural integrity at high temperatures. Its exceptional heat resistance, wear resistance, and dimensional stability make it the ideal choice for ensuring the efficiency and precision of the die casting process.
7. FAQs
Frequently Asked Questions About Hot Work Tool Steel in Die Casting
Q1. Can hot work tool steel be used for low-temperature die casting processes?
Yes, hot work tool steel can be used for low-temperature die casting processes, but its exceptional heat resistance is most beneficial in high-temperature die casting applications.
Q2. Are there specific grades of hot work tool steel for different types of die casting?
Yes, there are various grades of hot work tool steel tailored for specific die casting applications, depending on the type of metal being cast and the process conditions.
Q3. How does hot work tool steel compare to other materials, such as cold work tool steel, for die casting?
Hot work tool steel excels in die casting due to its exceptional heat resistance, which is crucial for withstanding the extreme temperatures generated during the process. Cold work tool steel is not suitable for high-temperature die casting applications.
Q4. Can hot work tool steel molds be reused for multiple die casting cycles?
Yes, hot work tool steel molds are designed for durability and can be reused for multiple die casting cycles, provided they are properly maintained and cleaned between cycles.
Q5. Are there alternative materials to hot work tool steel for die casting applications?
While there are alternative materials, hot work tool steel remains a top choice for die casting due to its unique combination of heat resistance, durability, and machinability.
In conclusion, hot work tool steel is an indispensable material for die casting, enabling the production of high-precision, durable components in industries where efficiency and reliability are paramount. Its exceptional heat resistance, wear resistance, and dimensional stability ensure that die casting processes run smoothly, reducing costs and enhancing the overall quality of manufactured parts.