Introduction
In the world of manufacturing, performance is the ultimate measure of success. Whether you’re forging intricate components, extruding metal profiles, or die-casting precision parts, the choice of materials plays a pivotal role in achieving exceptional results. Hot work tool steel alloys have emerged as the unsung heroes of the metallurgical realm, elevating performance to new heights. In this comprehensive guide, we will embark on a journey through the realm of hot work tool steel alloys, exploring their composition, properties, and the transformative impact they have on various industrial applications. From enhancing heat resistance to bolstering wear resistance, these alloys are the keys to unlocking unparalleled performance in the world of manufacturing.
Unraveling Hot Work Tool Steel Alloys<a name=”unraveling-hot-work-tool-steel-alloys”
Hot work tool steel alloys are a class of high-performance materials engineered to thrive in extreme conditions. They are meticulously crafted to endure high temperatures, mechanical stress, and wear, making them indispensable in manufacturing processes.
The Composition of Excellence<a name=”composition-of-excellence”
1. Alloy Components
Hot work tool steel alloys consist of a precise blend of alloying elements, including chromium, tungsten, molybdenum, and vanadium. This unique composition forms the foundation for their exceptional properties.
Heat Resistance: The Crucial Factor<a name=”heat-resistance-crucial-factor”
2. Exceptional Heat Tolerance
The hallmark of hot work tool steel alloys is their remarkable heat resistance. They can withstand temperatures well above 1000°C (1832°F) without losing structural integrity, making them ideal for processes involving extreme heat.
Wear Resistance: Defying Abrasion<a name=”wear-resistance-defying-abrasion”
3. Prolonged Tool Life
In manufacturing, tools and dies are subjected to continuous wear and abrasion. Hot work tool steel alloys offer exceptional wear resistance, significantly extending the life of these crucial components.
Toughness: Resilience Under Pressure<a name=”toughness-resilience-under-pressure”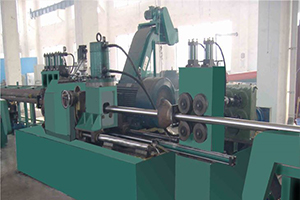
4. Resilience in Adverse Conditions
Beyond heat resistance, hot work tool steel alloys boast remarkable toughness. This resilience ensures that tools and dies can withstand the intense mechanical stress and impact they encounter during manufacturing processes.
Precision in Dimensional Stability<a name=”precision-in-dimensional-stability”
5. Consistent Precision
In industries where dimensional accuracy is paramount, hot work tool steel alloys shine. They maintain dimensional stability even under high temperatures, ensuring that each component adheres to strict tolerances.
Machinability: Shaping the Future<a name=”machinability-shaping-the-future”
6. Versatile Machining
Hot work tool steel alloys’ versatility extends to their machinability. They can be precisely machined into intricate shapes and forms, making them ideal for a wide range of manufacturing applications.
Applications That Soar with Alloys<a name=”applications-that-soar-with-alloys”
7. Thriving in Diverse Industries
Hot work tool steel alloys find applications in various industries, including automotive, aerospace, construction, and more. They are the backbone of manufacturing processes that demand precision and durability.
Tailoring Alloys to Your Needs<a name=”tailoring-alloys-to-your-needs”
In some cases, it may be necessary to customize hot work tool steel alloys to meet specific requirements. This can involve altering the alloy composition or applying specific heat treatments to achieve desired characteristics.
Challenges in Alloy Selection<a name=”challenges-in-alloy-selection”
Choosing the right hot work tool steel alloy can be challenging due to the myriad of options and the need to balance multiple factors. Making an informed choice is essential to ensure optimal performance in your manufacturing processes.
FAQ<a name=”faq”
1. Can hot work tool steel alloys be used for cold work applications?
While hot work tool steel alloys are primarily designed for high-temperature applications, they may not perform optimally in cold work conditions.
2. Are there specific alloy grades for different applications?
Yes, various alloy grades of hot work tool steel are tailored to meet the demands of specific applications. Common grades include H13, H11, and H21, each with its unique properties.
3. Can hot work tool steel alloys be reconditioned or refurbished after use?
In some cases, hot work tool steel alloys can be reconditioned or refurbished through processes like rehardening and retempering.
4. What safety precautions should be taken when working with hot work tool steel alloys?
Safety precautions are essential when handling these alloys, including protective gear and safe handling practices to minimize risks.
5. Can hot work tool steel alloys be recycled after use?
Yes, hot work tool steel alloys are recyclable, but the extent of recycling depends on factors such as the extent of wear and the specific application.
Conclusion<a name=”conclusion”
Hot work tool steel alloys are the unsung heroes of manufacturing, silently elevating performance and precision in various industrial applications. Their exceptional heat resistance, wear resistance, toughness, and dimensional stability make them indispensable in shaping metals with unrivaled accuracy and durability. Understanding the pivotal role of these alloys in manufacturing is essential for achieving optimal results and ensuring the longevity of tools and dies. In a world where precision and performance are paramount, hot work tool steel alloys stand as a testament to the enduring pursuit of excellence in metallurgy and manufacturing.