Welcome to My Blog! 🌟
Before we dive into the content, I’d love for you to join me on my social media platforms. It’s where I share more insights, engage with our vibrant community, and post regular updates. Here’s how you can stay connected:
📘 Facebook: Connect with me on Facebook
Now, let’s embark on this journey together. I hope you find the content here insightful, engaging, and most importantly, valuable. Let’s explore, learn, and grow together! 🚀
Table of Contents
Introduction
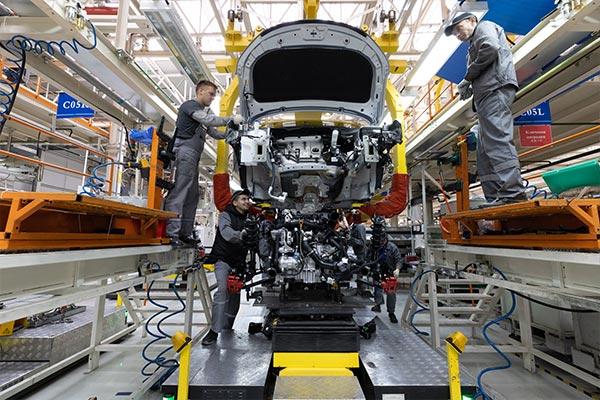
Even as alternative materials like aluminum and composites gain traction, steel remains the backbone of automotive construction. Its unmatched strength, cost efficiency, recyclability, and ongoing innovation make it essential for building safer, greener, and smarter vehicles. Steel supports emerging mobility trends global OEMs embrace.
Wear‑Resistant steel for Engine Durability
In the heart of every vehicle lies the engine—a complex assembly of high-precision components operating under intense heat, pressure, and mechanical load. To ensure longevity and uninterrupted performance, manufacturers rely on wear-resistant steel grades such as D2, D3, A2, and D6.
These tool steels are renowned for their exceptional hardness, resistance to deformation, and ability to withstand thermal cycling. For instance:
- D2 steel, a high-carbon, high-chromium cold-work steel, provides outstanding abrasion resistance, making it ideal for valve seats and injection parts.
- A2 steel offers a balanced profile of toughness and wear resistance, allowing for flexibility in parts that encounter variable loads, such as timing gears.
- D6, known for its high carbon and chromium content, handles extreme wear environments, making it suitable for parts like camshaft lobes that endure high-friction contact.
The result? Engines built with these wear-resistant materials last longer, require fewer repairs, and deliver consistent performance even under aggressive driving conditions. Additionally, using steel in these contexts allows for precise machining, essential in achieving the tight tolerances required for internal combustion systems.
High‑Strength steel in Chassis, Safety, and Structural Integrity
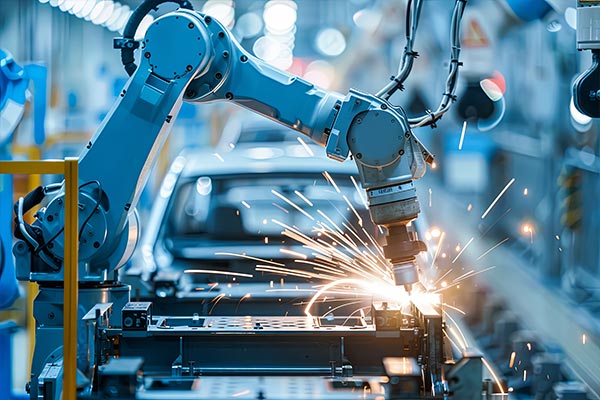
Beyond the engine bay, the structural core of the vehicle—its chassis and safety cell—demands materials that can absorb impact energy, prevent cabin intrusion, and maintain frame integrity during collisions. This is where high-strength steel becomes indispensable.
Grades such as H11, H13, and the M-series steels (M2, M4, M7) have emerged as go-to choices for automotive engineers. Here’s why:
- H11 and H13 are hot-work steels capable of maintaining mechanical stability under repeated thermal and mechanical shocks. This is critical in components exposed to braking heat, such as control arms and support brackets.
- M-series tool steels deliver excellent toughness and tensile strength, with M2 being particularly common in load-bearing chassis elements where lightweight construction meets crashworthiness demands.
These steels are forged or formed into impact-critical parts like side intrusion beams, crash boxes, and crumple zones. Their mechanical behavior ensures maximum energy absorption, protecting occupants and adhering to international crash test regulations such as Euro NCAP and NHTSA standards.
Moreover, high-strength steel’s weldability and formability make it ideal for automated production lines, enabling precise component shaping without sacrificing material integrity.
Advanced High‑Strength Steel (AHSS) Trends
As automakers navigate the dual challenge of lightweighting and safety optimization, Advanced High-Strength Steels (AHSS) have revolutionized vehicle design. These modern steel categories offer superior strength-to-weight ratios, enabling significant mass reduction while maintaining—or even improving—structural integrity.
Common AHSS types include:
- Dual-Phase (DP) steel: Combines soft ferrite and hard martensite to create high tensile strength with good elongation, ideal for B-pillars and crash reinforcement beams.
- Transformation-Induced Plasticity (TRIP) steel: Offers energy-absorbing capacity under dynamic loads, perfect for use in crumple zones and bumper beams.
- Martensitic steel: Extremely high strength and hardness, often used in safety-critical parts such as side-impact door beams or floor cross members.
According to automotive industry research, switching from traditional steel to AHSS in body-in-white (BIW) structures can reduce vehicle mass by 25–40%, directly contributing to:
- Improved fuel economy
- Lower CO₂ emissions
- Greater acceleration and braking efficiency
The integration of AHSS also supports platform modularization, allowing automakers to design multiple vehicle types from a shared lightweight architecture.
TRIP Steel: Strength with Flexibility
Among the most promising AHSS types, TRIP steel stands out for its unique ability to combine rigidity and ductility—two properties typically considered trade-offs.
This is achieved through the presence of retained austenite in the steel’s microstructure, which transforms into martensite under mechanical strain. This transformation enhances the material’s strength dynamically during deformation, a process known as strain hardening.
Key benefits of TRIP steel include:
- Superior crash energy absorption, critical in side-impact and frontal collisions
- Weight savings compared to conventional steels, enhancing fuel efficiency
- Excellent elongation properties, allowing complex forming without cracking
Applications of TRIP steel span from A-pillar reinforcements and door impact beams to subframe structures and front-end modules. Its usage aligns with stringent safety regulations while also meeting OEM goals for reducing vehicle weight.
TRIP steel is also well-suited for electric vehicles (EVs), where energy management and occupant safety are paramount, and where lighter structures can compensate for the added weight of battery systems.
Table: Steel Grades vs. Typical Vehicle Use
Grade | Category | Application | Primary Advantage |
---|---|---|---|
D2, D3, A2, D6 | Wear-resistant steel | Camshafts, valve seats, gears | High hardness, wear resistance |
H11, H13, M2–M7 | Hot-work/HS steels | Brakes, chassis files | Toughness at high temps |
Dual‑Phase, TRIP | AHSS | Crash structures, subframes | Strength + ductility |
P20, H13 | Mold steel | Injection molds, body panels | Precision & thermal fatigue resistance |
Steel E‑Motive—Steel in EVs & Autonomous Vehicles
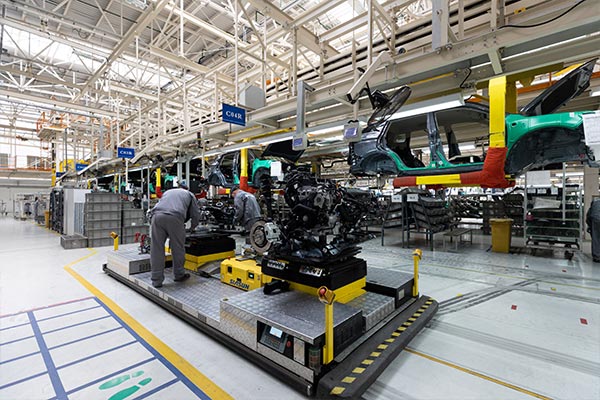
As the global automotive industry transitions toward electric mobility and autonomous driving, steel continues to play a pivotal role in shaping the design, safety, and sustainability of future vehicles. One of the most notable initiatives in this space is the Steel E‑Motive project, led by WorldAutoSteel, which demonstrates how advanced steel applications support next-generation electric and self-driving vehicle architectures.
Unlike past assumptions that lightweighting required replacing steel with expensive composites or aluminum, Steel E‑Motive proves that high-strength and ultra-high-strength steel (UHSS) can achieve comparable or superior results in terms of:
- Weight reduction
- Crash safety performance
- Cost-effectiveness
- Sustainability targets, including CO₂ reductions
The project’s digital vehicle models showed that efficient structural design using steel can reduce the overall body weight of autonomous EVs by up to 20%, while still achieving global crash safety standards such as Euro NCAP, IIHS, and FMVSS. This makes steel not only relevant but indispensable for future-forward vehicle engineering.
Steel in Electric Vehicle (EV) Battery Enclosures
One of the most structurally demanding areas in EV design is the battery enclosure, which must protect high-voltage lithium-ion battery packs from impacts, thermal events, and water ingress. These battery packs often weigh over 400 kilograms, adding substantial mass to the vehicle and posing new safety challenges.
Ultra-high-strength steel (UHSS)—often rated at 1500 MPa or higher—is increasingly used for battery enclosure systems. These steels provide:
- Superior impact resistance in case of side or underbody collisions
- Thermal stability, helping manage runaway events
- Cost-efficiency, compared to aluminum or carbon composites
Additionally, innovations in dual-phase (DP) steel allow manufacturers to reduce subframe weight by 15–20%, helping to offset the mass of the battery system and improve overall vehicle efficiency. The formability and weldability of these steels also enable seamless integration into mass production lines, unlike more exotic materials that require specialized handling.
As a result, EV manufacturers can achieve structural safety, minimize costs, and reduce emissions associated with vehicle weight—all through optimized use of advanced steel solutions.
Europe & Germany Leading the Green Steel Revolution
Europe is at the forefront of decarbonizing steel production, spearheading a global push toward low-emission manufacturing through hydrogen-based processes and electrification.
Germany in particular is making bold strides:
- Major German steelmakers such as Thyssenkrupp, Salzgitter, and Benteler are investing in green hydrogen infrastructure and direct-reduced iron (DRI) plants powered by renewable electricity.
- Over €7 billion in public funding is supporting projects that aim to reduce CO₂ emissions by up to 95%, compared to conventional blast furnace operations.
- The integration of electric arc furnaces (EAF) into production lines is enabling greater use of scrap steel, contributing to a more circular and less carbon-intensive supply chain.
This transformation aligns with the EU’s Fit for 55 and Green Deal targets, establishing a framework where automotive-grade steel can meet both performance and sustainability criteria. Such developments also secure Europe’s leadership in supplying high-quality green steel to EV manufacturers both domestically and globally.
Global Market Outlook for Advanced Steel
The demand for advanced high-strength steel (AHSS) in the automotive sector is booming. According to market forecasts, the global AHSS market, valued at USD 27 billion in 2025, is expected to grow to USD 44.5 billion by 2032, representing a compound annual growth rate (CAGR) of 7.8%.
Key drivers behind this growth include:
- Stricter global fuel economy and emissions regulations
- The proliferation of EVs, which require high-strength lightweight materials
- A focus on crash safety and occupant protection
- Increased investments in automotive lightweighting technologies
This sustained demand is reshaping global steel production priorities, encouraging suppliers to pivot toward grades suitable for hot stamping, roll forming, and complex shaping—all necessary for EV and autonomous vehicle applications.
AHSS now makes up a growing share of body-in-white (BIW) materials in both internal combustion and electric vehicles. Companies that invest in AHSS technologies today are well-positioned to meet OEM demand over the next decade.
Sustainability and Circular Steel Economy
In the race toward net-zero emissions, steel recycling and circular manufacturing are gaining significant traction. One of steel’s greatest advantages is its infinite recyclability without loss of quality, making it a cornerstone of a circular economy.
Environmental and resource-saving benefits of steel recycling include:
- 1.5 tonnes of CO₂ saved per tonne of recycled steel
- Conservation of 1.4 tonnes of iron ore and 740 kg of coal
- Energy savings of up to 75% compared to primary steelmaking
Globally, nearly 90% of steel used in the automotive sector is eventually recycled, especially in regions like Europe and the United States, where legislation and infrastructure support high recycling rates.
Countries are also ramping up the use of electric arc furnaces (EAF), which can operate entirely on scrap steel and renewable electricity. These efforts are reinforced by regulatory frameworks such as:
- EU’s Circular Economy Action Plan
- U.S. Infrastructure Investment and Jobs Act, which promotes low-carbon materials in public projects
Together, these initiatives are transforming steel from a linear to a circular industry model, directly supporting the environmental goals of automotive manufacturers.
Challenges – Cost & Energy
Despite promising progress, transitioning to green steel is not without its challenges. Technologies like hydrogen-based direct reduced iron (H2-DRI) and electrified steel furnaces require substantial capital investment, and in some regions, energy availability remains a barrier.
Specific hurdles include:
- High upfront costs for retrofitting existing blast furnaces or building H2-compatible infrastructure
- Volatile energy prices, particularly electricity, which can make EAF operation cost-prohibitive during peak periods
- Supply chain limitations in sourcing green hydrogen at scale and cost
Furthermore, the intermittency of renewable energy means that electric steel plants may need to modulate production, especially when grid capacity is constrained. This affects output consistency and can deter smaller producers from adopting greener technologies.
That said, many governments are introducing carbon border taxes and incentives to support the adoption of low-emission steel, which will accelerate wider adoption despite the initial cost curve.
The U.S. & Asia: Regional Steel Dynamics
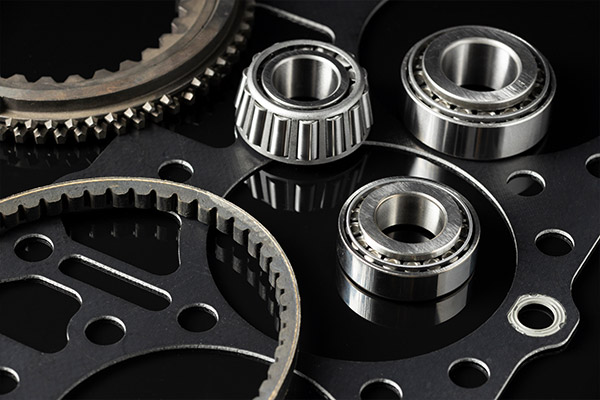
In the United States, investment in EAF modernization is breathing new life into traditional manufacturing regions, particularly in the Rust Belt. Companies such as BlueScope and Nucor are leading this transformation, delivering high-quality automotive steel with a lower carbon footprint.
Key trends in the U.S. include:
- Expansion of mini-mills, which use scrap and renewable energy
- Growth in localized steel supply chains, reducing logistics emissions
- Policy support for green infrastructure and EV production incentives
In contrast, the Asia-Pacific region, particularly China, remains the largest consumer of AHSS, accounting for over 50% of global demand. The rapid rise of electric vehicles in China is driving massive investments in both automotive production and next-generation steel processing facilities.
Asian steelmakers are also actively researching green steel production, with pilot programs for hydrogen-based furnaces in Japan, South Korea, and India. As these initiatives mature, the region is expected to play a central role in shaping the future global supply of sustainable automotive steel.
Conclusion
Whether in driverless EVs, crash-safe structures, or sustainable battery systems, steel holds irreplaceable value. With continual innovation—from green production and AHSS advances to circular economy integration—it will remain central in building the vehicles of tomorrow.
FAQ
What makes steel superior for automotive structures?
Steel, especially AHSS, combines light weight, cost efficiency, high strength, and ease of recycling—essential for safety and sustainability.
Why is green steel important?
The industry emits ~7–9% of global CO₂. Green methods like hydrogen‑DRI and recycled EAFs drastically cut emissions, enabling cleaner production.
Can steel replace aluminum in EVs?
Yes. AHSS offers similar weight savings, greater recyclability, and cost benefits compared to aluminum, making it ideal for EV frameworks.
How much steel is recycled globally?
Over 85–90% steel is recycled at end-of-life. Each tonne recycled prevents 1.5 t CO₂ and saves natural resources.
What steel developments are coming next?
Emerging alloys like Fe-Mn-Al-C lightweight blends and nano-carbide steels promise further gains in strength and weight reduction .