Welcome to My Blog! 🌟
Before we dive into the content, I’d love for you to join me on my social media platforms. It’s where I share more insights, engage with our vibrant community, and post regular updates. Here’s how you can stay connected:
📘 Facebook: Connect with me on Facebook
Now, let’s embark on this journey together. I hope you find the content here insightful, engaging, and most importantly, valuable. Let’s explore, learn, and grow together! 🚀
Table of Contents
Introduction
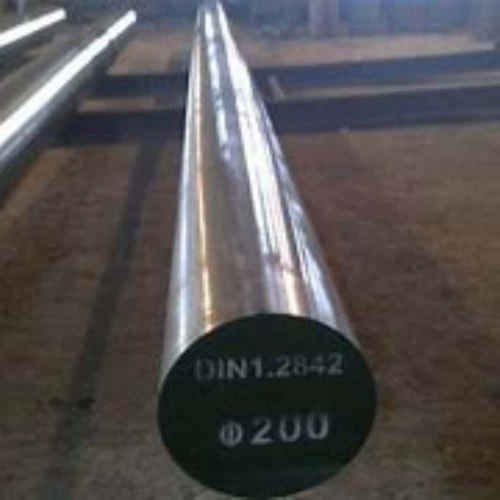
O2 tool steel, a versatile alloy revered in manufacturing and tool – making, strikes a unique balance between hardness and toughness. Its medium – carbon, oil – hardening composition makes it ideal for applications ranging from cutting tools to die – making. However, achieving peak durability requires more than just selecting the right material. This blog reveals eight expert – approved strategies to enhance the lifespan of O2 tool steel, ensuring it withstands the rigors of demanding operations.
Hack 1: Optimal Heat Treatment
Understanding the Basics of Heat Treatment for O2 Tool Steel
Heat treatment is the cornerstone of unlocking O2 tool steel’s full potential. This process manipulates the steel’s internal structure through controlled heating, soaking, and cooling, altering its mechanical properties. For O2 tool steel, improper heat treatment can lead to brittleness or softness, severely shortening its service life.
Step – by – Step Heat Treatment Process
- Preheating: Begin by slowly heating the steel to 1200 – 1300°F (650 – 700°C) to eliminate internal stresses and ensure even heating.
- Austenitization: Raise the temperature to 1550 – 1650°F (845 – 900°C) and hold it for 10 – 20 minutes, allowing the steel to transform into austenite.
- Quenching: Rapidly cool the steel in oil to 400 – 500°F (205 – 260°C) to achieve the desired hardness.
- Tempering: Temper at 350 – 1000°F (175 – 540°C) based on the required hardness – toughness balance. Multiple tempering cycles can further refine the structure.
Hack 2: Precise Machining Techniques
The Impact of Machining on Durability
Machining operations significantly influence O2 tool steel’s durability. Excessive cutting forces, improper speeds, and feeds can introduce surface defects and internal stresses, acting as initiation points for cracks and wear. A meticulous approach to machining minimizes these risks.
Recommended Machining Parameters
Operation | Cutting Speed (ft/min) | Feed Rate (in/rev) | Depth of Cut (in) |
Roughing | 50 – 80 | 0.005 – 0.015 | 0.02 – 0.06 |
Finishing | 30 – 50 | 0.002 – 0.005 | 0.005 – 0.015 |
Hack 3: Proper Surface Finishing
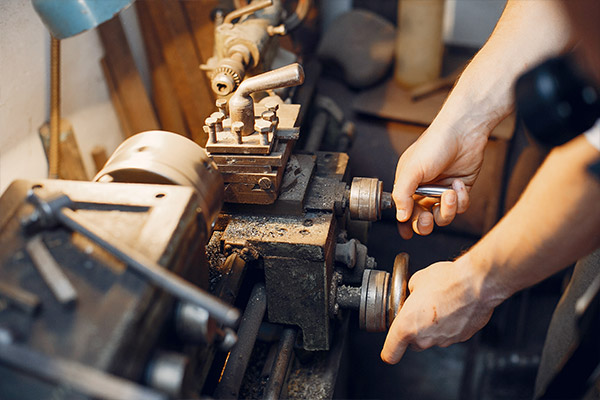
Different Surface Finishing Methods for O2 Tool Steel
Surface finishing not only improves the aesthetic appeal but also enhances the functional performance of O2 tool steel. Common methods include:
- Grinding: Removes material to achieve a precise dimension and surface finish.
- Polishing: Produces a smooth, reflective surface, reducing friction and wear.
- Shot Peening: Introduces compressive stresses on the surface, improving fatigue resistance.
How Surface Finishing Enhances Durability
A smoother surface reduces the likelihood of debris adhesion and corrosion, while shot peening strengthens the surface layer, making it more resistant to impact and cyclic loading.
Hack 4: Lubrication Secrets
The Role of Lubrication in O2 Tool Steel Performance
Lubrication is essential for minimizing friction, reducing wear, and dissipating heat during operation. Inadequate lubrication can lead to excessive wear, overheating, and premature failure of O2 tool steel components.
Choosing the Right Lubricant
Select a lubricant based on the operating conditions, such as temperature, load, and speed. For high – temperature applications, synthetic lubricants offer better thermal stability, while extreme – pressure lubricants are suitable for heavy – load scenarios.
Hack 5: Storage Strategies
Ideal Storage Conditions for O2 Tool Steel
Proper storage preserves the integrity of O2 tool steel. Store it in a dry, clean environment with a relative humidity below 40% and a temperature range of 60 – 70°F (15 – 21°C). Avoid direct contact with moisture, chemicals, and other corrosive substances.
Storage Precautions to Prevent Damage
Use protective covers or wraps to shield the steel from scratches and contaminants. Store it in a vertical position to prevent warping and ensure proper air circulation.
Hack 6: Quality Control in Material Selection
Identifying High – Quality O2 Tool Steel
Inspect the steel for consistent color, smooth surface finish, and clear markings. Request a material certificate to verify its chemical composition and mechanical properties.
The Risks of Using Low – Quality Material
Low – quality O2 tool steel may contain impurities or have an inconsistent microstructure, resulting in reduced performance and durability. This can lead to unexpected failures, costly downtime, and safety hazards.
Hack 7: Regular Maintenance and Inspection
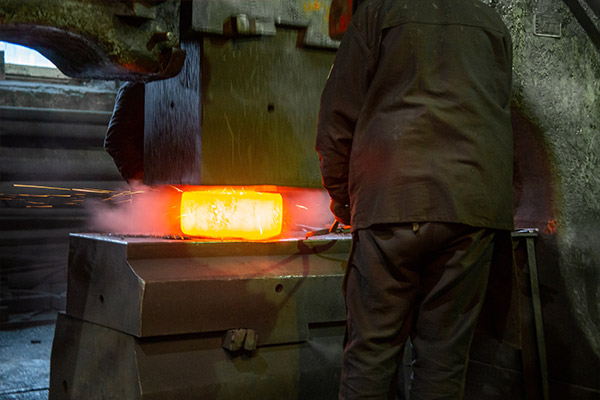
Setting Up a Maintenance Schedule
Establish a routine maintenance schedule based on the usage frequency and severity of the application. Inspect the components for wear, cracks, and deformation, and perform cleaning, lubrication, and adjustment as needed.
What to Look for During Inspections
Pay close attention to high – stress areas, such as edges, corners, and transitions. Use non – destructive testing methods, such as magnetic particle inspection or ultrasonic testing, to detect internal defects.
Hack 8: Complementary Material and Design Considerations
Selecting Complementary Materials
When O2 tool steel interacts with other materials, choose combinations that minimize wear and corrosion. For example, pair it with materials of similar hardness to prevent galling.
Design Optimization for Durability
Design components with smooth transitions, fillets, and radii to reduce stress concentrations. Consider the load distribution and operating conditions to optimize the geometry for maximum durability.
Conclusion
By implementing these eight expert hacks, you can significantly enhance the durability of O2 tool steel, ensuring it delivers reliable performance over an extended lifespan. From precise heat treatment and machining to proper maintenance and storage, each strategy plays a crucial role in unlocking the full potential of this versatile alloy.
FAQ
Q1: Can I use O2 tool steel for high – speed cutting applications?
O2 tool steel is not the ideal choice for high – speed cutting due to its relatively low hot – hardness. For such applications, high – speed steels or carbide tools are more suitable. However, for moderate – speed cutting operations, O2 tool steel can provide excellent performance when properly heat – treated and maintained.
Q2: How often should I perform heat treatment on my O2 tool steel tools?
The frequency of heat treatment depends on the usage conditions and the desired performance. In general, heat treatment is performed during the initial manufacturing process and may be repeated if the tool undergoes significant wear or damage. Regular inspection and testing can help determine when heat treatment is necessary.
Q3: What is the best way to repair a damaged O2 tool steel component?
The repair method depends on the type and extent of the damage. Minor surface defects can often be repaired through grinding, polishing, or welding. For more severe damage, such as cracks or fractures, it may be necessary to replace the component. Consult a professional or refer to the manufacturer’s guidelines for specific repair procedures.