Welcome to My Blog! 🌟
Before we dive into the content, I’d love for you to join me on my social media platforms. It’s where I share more insights, engage with our vibrant community, and post regular updates. Here’s how you can stay connected:
📘 Facebook: Connect with me on Facebook
Now, let’s embark on this journey together. I hope you find the content here insightful, engaging, and most importantly, valuable. Let’s explore, learn, and grow together! 🚀
Table of Contents
Introduction
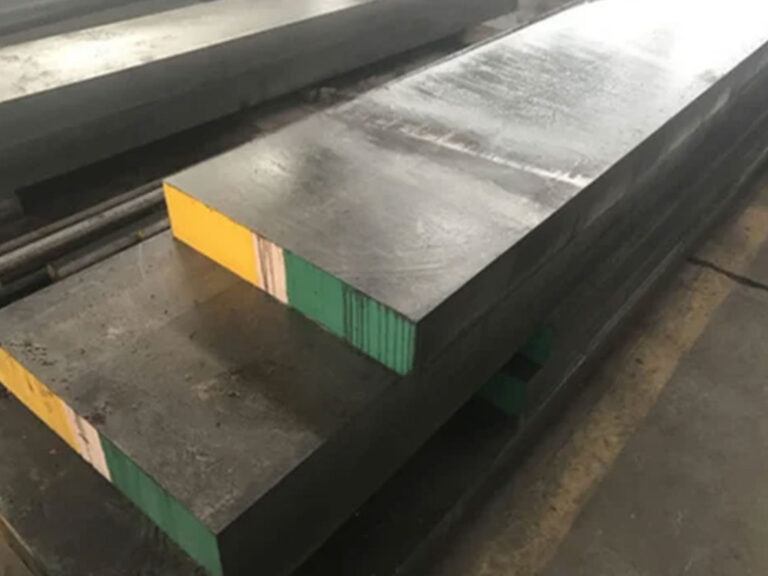
In the world of industrial manufacturing and engineering, tool steel plate plays a critical role. These high-performance materials are the backbone of tooling applications, including cutting, forming, stamping, and die-making. However, to ensure these plates deliver maximum performance, certain practices and enhancements must be applied. This article explores four powerful ways to significantly improve the performance and longevity of tool steel plate while keeping operational efficiency and cost-effectiveness in mind.
NO 1. Optimal Heat Treatment Techniques for Enhanced Durability
Heat treatment is a vital process that directly influences the mechanical properties of tool steel plate. This process modifies the microstructure of the steel, optimizing its hHeat treatment is a vital process that directly influences the mechanical properties of tool steel plate. This process modifies the microstructure of the steel, optimizing its hardness, strength, toughness, and wear resistance. Implementing the right heat treatment technique can greatly improve the lifespan and reliability of tooling components.
Key Considerations:
- Preheating: Gradual heating before hardening reduces thermal shock and minimizes the risk of cracking.
- Austenitizing: Heating to a high temperature to form austenite ensures uniform hardness throughout the material.
- Quenching: Rapid cooling in mediums like oil, air, or a salt bath locks the desired microstructure into place.
- Tempering: Reheating to a lower temperature relieves internal stresses and balances hardness with toughness.
Advantages:
- Improved wear resistance, enabling longer service life in abrasive environments
- Increased toughness to withstand impact and mechanical stress
- Reduced risk of cracking or deformation during high-load operations
Proper control of the heat treatment cycle ensures that the tool steel plate maintains its intended performance level, even in high-stress industrial environments. Additionally, using precision-controlled furnaces and tracking thermocouple data can improve consistency in large production runs.
At QiLu Special Steel, our expert metallurgists apply tightly controlled heat treatment protocols tailored to each tool steel grade, ensuring every batch meets the highest performance standards.
NO 2. Surface Treatments to Extend Tool Steel Plate Life
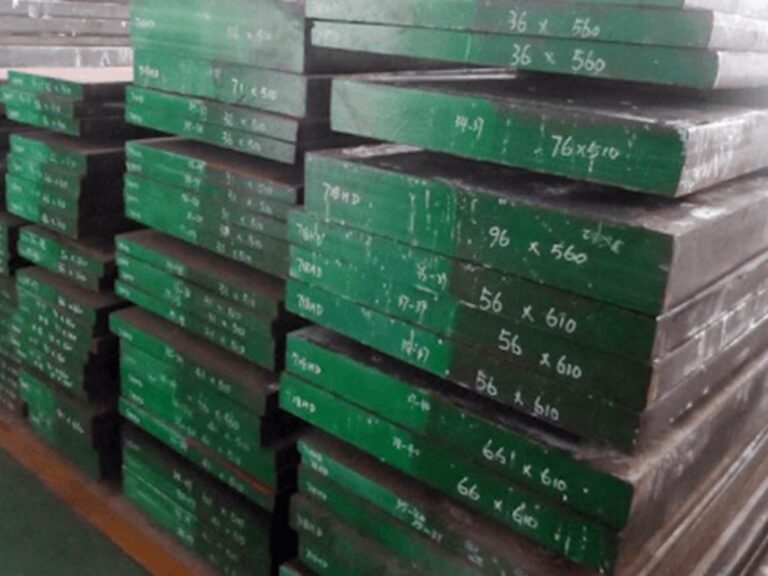
Surface modification is another effective way to enhance the functionality of tool steel plate. Applying advanced surface treatments improves the resistance to friction, wear, and corrosion, all of which are common failure modes in tooling applications.
These surface enhancements act as a barrier, protecting the core steel from premature wear and maintaining tight tolerances over prolonged use. Whether for cutting tools, molds, or dies, an appropriate surface treatment can yield remarkable performance improvements.
Popular Surface Treatments:
Treatment Method | Benefits | Application Suitability |
---|---|---|
Nitriding | Increases surface hardness, improves fatigue resistance | Ideal for forming tools |
PVD Coating | Enhances wear resistance, adds lubricity | Suitable for cutting tools |
Carburizing | Deep case hardening, enhances load capacity | Used in stamping dies |
Each method comes with its specific benefits. Nitriding forms a hard surface layer without the need for quenching, reducing distortion. PVD coatings, often applied in vacuum chambers, deposit ultra-hard films of materials like titanium nitride. Carburizing, on the other hand, diffuses carbon into the surface for deeper hardening, ideal for applications that involve high contact stress.
Emerging surface treatments such as CVD (Chemical Vapor Deposition) and duplex coatings (a combination of nitriding followed by PVD) are also gaining popularity in high-performance tooling environments. These offer multi-functional benefits by combining different surface engineering principles. For instance, a duplex coating can improve both adhesion and overall hardness of the top layer, leading to better durability.
Applying the right surface treatment not only increases the longevity of tool steel plate but also improves its performance in demanding environments. Careful consideration should be given to the intended use, load cycles, and required surface finish. Collaborating with coating specialists and conducting real-world performance tests can also help determine the most cost-effective and suitable treatment for specific production scenarios. Additionally, ensuring proper surface preparation before applying treatments—such as polishing or grit blasting—can enhance bonding and coating consistency. use, load cycles, and required surface finish.
NO 3. Proper Material Selection and Alloy Composition
Not all tool steel plates are created equal. Choosing the right grade based on the intended application is crucial. The chemical composition of alloying elements such as chromium, vanadium, molybdenum, and tungsten influences the plate’s hardness, wear resistance, heat resistance, and machinability.
A well-informed material selection process can ensure optimal tool performance, reduce maintenance frequency, and improve efficiency. The wrong choice, however, could result in underperformance or early failure.
Common Tool Steel Grades:
- A2: Balanced wear resistance and toughness; used in blanking and forming operations where dimensional stability is important.
- D2: Offers high wear resistance; preferred for long production runs where abrasive wear is a concern.
- M2: Excellent red hardness makes it ideal for high-speed machining and cutting applications.
- O1: Oil-hardening tool steel suitable for general-purpose tools; easy to machine and commonly used in knives and cutting dies.
Each of these grades comes with trade-offs between machinability, hardenability, and toughness. For example, A2 provides decent machinability with good dimensional stability after heat treatment. D2 offers superior wear resistance but is more challenging to grind and machine. M2 is best for high-heat applications, though it demands specialized equipment due to its hardness.
The right selection should be based on detailed analysis of the operating environment, cutting speeds, loads, exposure to thermal cycling, and part geometry. Tooling engineers often perform simulations or rely on past application data to match grades to real-world needs.
Additionally, alloy composition impacts the material’s response to heat treatment and surface enhancement techniques. For instance:
- Chromium improves corrosion and oxidation resistance.
- Vanadium enhances wear resistance and refines grain structure.
- Molybdenum increases toughness and reduces risk of embrittlement.
- Tungsten supports red hardness and high-speed strength.
Choosing a steel grade with the right alloy mix ensures consistent performance and avoids premature tool failure. Beyond chemistry, factors like available stock sizes, dimensional tolerances, and ease of post-machining (e.g., grinding or EDM) should also influence selection. Working closely with steel suppliers and metallurgists can further enhance the decision-making process.
NO 4. Regular Maintenance and Condition Monitoring
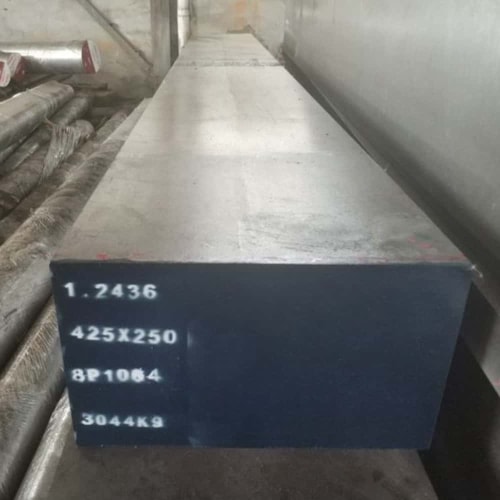
Even the best-quality tool steel plate will underperform without proper maintenance. Over time, stress, heat, and friction can degrade material properties, resulting in performance losses and failures. Regular inspection, lubrication, and monitoring can identify potential issues before they escalate into costly downtime or damage.
Maintenance Practices:
- Routine Inspection: Periodically examine the tool steel plate for signs of wear, cracking, surface pitting, or distortion. Visual and ultrasonic methods can reveal hidden defects. Digital inspection logs and checklists improve consistency across teams.
- Regrinding: Helps maintain edge geometry and restore the sharpness needed for precise tooling operations. This can reduce material waste and improve output consistency. Scheduled regrinding programs should be based on actual tool use cycles.
- Lubrication: Regular and proper lubrication reduces metal-to-metal contact, lowers operating temperatures, and prevents galling or seizure. Using the correct lubricant type for the application ensures effectiveness and minimizes buildup.
- Condition Monitoring: Advanced techniques include installing sensors or using digital software to track wear levels, temperature changes, and vibration data over time. These insights enable predictive maintenance decisions.
Incorporating predictive maintenance strategies, such as condition-based monitoring, helps detect failure patterns early. This minimizes unplanned downtime and optimizes resource allocation. Maintenance documentation and operator training are also critical components for sustaining peak performance. Companies should invest in cross-functional training for operators and technicians to recognize early warning signs and perform basic diagnostics.
A proactive maintenance schedule can significantly extend the life of tool steel plate, ensuring consistent performance and reducing downtime. When maintenance is seen as a value-generating activity rather than a cost center, it becomes a cornerstone of operational excellence.ensuring consistent performance and reducing downtime.
Conclusion
Improving tool steel plate performance is not a one-size-fits-all approach. It requires a combination of advanced heat treatment, surface enhancements, strategic material selection, and diligent maintenance. When these four powerful methods are implemented, industries benefit from increased productivity, reduced downtime, and long-lasting tooling solutions. As manufacturing technologies evolve, staying updated with these best practices becomes increasingly important.
FAQ
How does heat treatment affect tool steel plate?
It enhances hardness, wear resistance, and durability by modifying the internal structure of the steel.
Which surface treatment is best for cutting tools?
PVD coating is ideal due to its ability to reduce friction and improve wear resistance.
Can all tool steel plates be nitrided?
No, nitriding is suitable only for specific alloy compositions. Always check compatibility before applying.
How often should tool steel plates be maintained?
Maintenance frequency depends on usage, but routine inspections every few weeks are recommended.
What is the biggest mistake in tool steel plate usage?
Incorrect material selection without considering application requirements can lead to premature failure.