Welcome to My Blog! 🌟
Before we dive into the content, I’d love for you to join me on my social media platforms. It’s where I share more insights, engage with our vibrant community, and post regular updates. Here’s how you can stay connected:
📘 Facebook: Connect with me on Facebook
Now, let’s embark on this journey together. I hope you find the content here insightful, engaging, and most importantly, valuable. Let’s explore, learn, and grow together! 🚀
Table of Contents
Introduction
The quality of materials used in manufacturing and industrial applications is paramount. When it comes to high-performance tools and equipment, S7 tool steel stands out as one of the most reliable and versatile options available. Known for its exceptional hardness and durability, S7 tool steel is widely used in industries where precision, toughness, and resistance to wear and tear are crucial. In this blog post, we will explore how S7 tool steel hardness can improve your industrial projects, focusing on the benefits of using this material in different applications, its key properties, and its performance advantages.
What is S7 Tool Steel?
S7 tool steel is a high-performance alloy known for its superior shock resistance and exceptional toughness, which makes it an ideal choice for demanding applications in industries such as manufacturing, construction, and metalworking. This air-hardening tool steel is especially well-suited for use in tools and machinery that must withstand high impact, fatigue, and wear. The alloy is enriched with a combination of key elements, including chromium, molybdenum, and vanadium, each of which contributes to the overall strength, wear resistance, and heat stability of the material.
S7 tool steel is specifically designed to maintain its hardness even at elevated temperatures, which is a critical factor when working with tools exposed to heat during heavy-duty tasks. It is commonly used in environments where tools need to endure significant wear and tear or face constant shock, such as in die manufacturing, stamping, and cutting applications.
One of the standout features of S7 tool steel is its ability to be heat-treated to a hardness level between 57 and 60 on the Rockwell C scale. This range of hardness is ideal for tools that require a balance of both toughness and hardness, allowing the material to perform well under extreme conditions without becoming brittle or prone to breaking. This makes S7 a go-to choice for applications that require a material with both strength and the capacity to resist cracking under stress.
Key Characteristics of S7 Tool Steel
- Hardness: S7 tool steel has a hardness range of 57 to 60 on the Rockwell C scale, making it ideal for producing durable tools that can endure tough working conditions. This hardness helps S7 retain its sharpness and cutting ability even after extended use. Its ability to maintain stable hardness over time is crucial in industrial applications where tools face constant abrasion and friction. This combination of hardness and toughness makes S7 more reliable than many other tool steels in harsh environments.
- Toughness: S7 tool steel is known for its high toughness, which allows it to absorb energy and resist breaking under impact. This property makes it ideal for heavy-duty applications, such as die-casting, hammering, and high-impact cutting. S7’s toughness prevents cracking under mechanical stress, ensuring tools can withstand shock loads without failing. This resilience is why S7 is often used in die and tool making.
- Wear Resistance: S7’s superior wear resistance is directly linked to its hardness. Tools made from S7 maintain their original shape and functionality for longer periods, even under constant friction or abrasion. This wear resistance reduces the need for frequent replacements, leading to cost savings and higher productivity. S7 is an excellent choice for industries like metalworking, where tools face continuous abrasive conditions.
- Machinability: S7 tool steel is easier to machine than other high-hardness steels, such as D2 or M2, making it highly versatile. It can be heat-treated, ground, and polished with ease, allowing it to be shaped for various applications like dies, cutting tools, and punches. This flexibility makes S7 an attractive option for manufacturers seeking both durability and precision in toolmaking.
How S7 Tool Steel Hardness Improves Industrial Projects
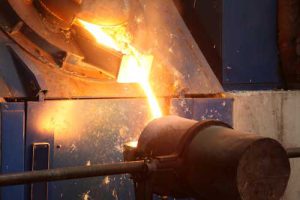
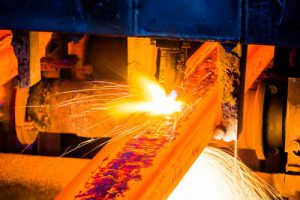
The hardness of S7 tool steel plays a critical role in enhancing the overall performance of industrial projects. Here’s how the S7 tool steel hardness specifically improves different aspects of your operations:
1. Enhanced Durability and Longevity
Durability is a crucial factor for industrial applications that involve continuous use of tools or machinery. S7 tool steel hardness ensures that tools made from this material can endure significant wear over time without requiring frequent replacements. This durability reduces downtime and increases the overall efficiency of industrial operations.
For example, in die manufacturing, the hardness of S7 tool steel ensures that the dies last longer, even under heavy pressure. This means fewer replacements are needed, resulting in significant cost savings.
2. Superior Performance in High-Stress Applications
Industrial projects often involve tools that are exposed to high-impact conditions, such as in metal forming, cutting, or pressing. S7 tool steel hardness provides the shock resistance and toughness needed for tools in these high-stress applications. The ability to withstand extreme pressures without cracking or deforming makes S7 an ideal material for industrial tools and machinery that face constant wear and tear.
For instance, forging tools, stamping dies, and other heavy-duty applications can all benefit from the hardness and shock resistance of S7 tool steel, allowing them to perform consistently under demanding conditions.
3. Improved Precision and Efficiency
The hardness of S7 tool steel doesn’t just contribute to the material’s ability to resist wear and impact; it also enhances the precision and efficiency of tools used in industrial projects. Tools that retain their sharpness and shape over time allow manufacturers to perform tasks more accurately, reducing errors and improving production rates.
In industries where precision is key, like mold manufacturing or cutting tool production, using S7 tool steel ensures that tools remain sharp and effective throughout their lifespan, reducing the need for constant maintenance and adjustments.
Applications of S7 Tool Steel in Industrial Projects
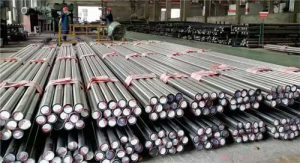
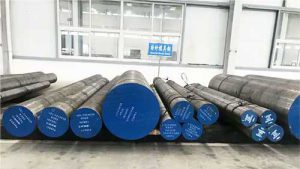
Given its outstanding properties, S7 tool steel hardness makes it ideal for a variety of industrial applications. Here are some of the key areas where this steel is commonly used:
- Die Manufacturing: S7 tool steel hardness is particularly well-suited for die manufacturing, as it can withstand the high forces involved in shaping and molding materials. Whether it’s used for forging dies, extrusion dies, or molding tools, the toughness and durability of S7 steel make it a reliable choice.
- Cutting Tools: Due to its hardness, S7 tool steel is also used for producing cutting tools such as saw blades, punches, and chisels. The hardness ensures a sharp cutting edge, while the toughness helps to maintain this sharpness even under heavy use.
- Press Tools and Hammers: Tools that are subjected to high-impact forces, such as press tools and hammers, benefit greatly from S7 tool steel hardness. The material’s ability to absorb shocks and resist cracking makes it ideal for these applications.
- Molds: In industries like plastic injection molding, where molds need to endure both high temperatures and mechanical stress, S7 tool steel hardness helps maintain the integrity of the mold, ensuring longevity and consistent performance.
Table: Key Properties of S7 Tool Steel
Property | Value |
---|---|
Hardness (Rockwell C) | 57-60 |
Tensile Strength | 1,600 MPa |
Impact Toughness | 50 Joules at -40°C |
Machinability | Moderate, easily machinable with carbide tools |
Yield Strength | 1,300 MPa |
Conclusion
In conclusion, S7 tool steel hardness plays a significant role in improving the performance, durability, and cost-effectiveness of industrial projects. The S7 tool steel hardness provides exceptional shock resistance, wear resistance, and longevity, making it the material of choice for industries that rely on high-performance tools. Whether it’s die manufacturing, cutting tools, press tools, or molds, the S7 tool steel hardness ensures that industrial operations run smoothly, efficiently, and cost-effectively. The ability to maintain S7 tool steel hardness even under extreme conditions helps extend the lifespan of tools, reducing downtime and replacement costs. Its unique combination of S7 tool steel hardness and toughness makes it an invaluable material for any industrial project that demands precision, reliability, and long-term durability.
FAQ
Why is S7 tool steel ideal for high-impact applications?
The S7 tool steel hardness allows it to absorb heavy impacts and shocks without cracking or deforming. This makes it ideal for applications like forging, hammers, and stamping tools.
Can S7 tool steel be further hardened for specific applications?
Yes, S7 tool steel can be heat-treated to achieve different hardness levels. However, it’s essential to maintain a balance between hardness and toughness to prevent brittleness.
How does the machinability of S7 tool steel compare to other steels?
S7 tool steel, despite its hardness, is easier to machine than many other tool steels like D2 or M2. This makes it a more versatile option for projects that require precision.
In what industries is S7 tool steel most commonly used?
Industries such as automotive manufacturing, aerospace, construction, and heavy machinery manufacturing commonly use S7 tool steel hardness due to its toughness, durability, and wear resistance.