Welcome to My Blog! 🌟
Before we dive into the content, I’d love for you to join me on my social media platforms. It’s where I share more insights, engage with our vibrant community, and post regular updates. Here’s how you can stay connected:
📘 Facebook: Connect with me on Facebook
Now, let’s embark on this journey together. I hope you find the content here insightful, engaging, and most importantly, valuable. Let’s explore, learn, and grow together! 🚀
Table of Contents
Introduction
When it comes to selecting the right tool steel for demanding applications, A2 tool steel and D2 tool steel are often the go-to materials. Both of these tool steels offer excellent properties, but understanding the key differences between A2 vs D2 tool steel is crucial in making the best choice for your project. Whether you’re considering A2 vs D2 tool steel for manufacturing precision tools, die-cuts, or industrial machinery, the strength, wear resistance, and durability of each material will significantly impact performance.
In this blog, we will delve into the critical aspects of A2 vs D2 tool steel, comparing their composition, properties, benefits, and suitability for various industrial applications. By the end, you’ll have a better understanding of which steel, A2 vs D2 tool steel, will offer you the maximum strength needed for your specific tasks. Whether you prioritize toughness or wear resistance, this comparison will provide insights into how A2 vs D2 tool steel can impact your decisions and lead to optimal performance in your tools and machinery.
Understanding A2 Tool Steel
A2 tool steel is an air-hardening steel known for its versatility and toughness. It falls under the category of cold work tool steels and is widely used in applications where high wear resistance and good toughness are required. A2 tool steel is a medium carbon, chromium-based steel that offers a good balance between hardness and strength.
Key Properties of A2 Tool Steel
- Hardness: A2 tool steel can achieve a Rockwell hardness of 57-62 HRC, making it highly resistant to wear and abrasion.
- Toughness: Compared to D2 tool steel, A2 offers superior toughness, making it less likely to crack under extreme pressure.
- Machinability: A2 is easier to machine than D2, which makes it a preferred choice when fine-tuning precision parts.
- Wear Resistance: A2 offers good wear resistance but does not outperform D2 when subjected to harsh abrasion.
What Makes D2 Tool Steel Stand Out?
D2 tool steel, often referred to as “high carbon, high chromium tool steel,” is designed to offer exceptional wear resistance and hardness. This makes it particularly ideal for applications requiring high strength and the ability to withstand severe wear. While it may not have the same level of toughness as A2, D2’s edge retention and resistance to abrasion make it a strong contender for long-term, high-stress use.
Key Properties of D2 Tool Steel
- Hardness: D2 tool steel has a higher hardness than A2, achieving a Rockwell hardness of 58-62 HRC, which makes it excellent for applications involving prolonged wear.
- Wear Resistance: D2 excels in wear resistance, particularly when used in applications where tools are exposed to extreme friction.
- Toughness: Although D2 is tough, it is more likely to crack under sudden impacts or pressure compared to A2.
- Corrosion Resistance: D2 offers better corrosion resistance compared to A2, thanks to its higher chromium content.
A2 vs D2 Tool Steel: Key Differences
To understand which material is best suited for your specific needs, it’s important to compare A2 vs D2 tool steel based on their physical properties, performance, and suitability for various industrial applications. The table below outlines some of the significant differences between A2 and D2 tool steel.
Property | A2 Tool Steel | D2 Tool Steel |
---|---|---|
Hardness | 57-62 HRC | 58-62 HRC |
Wear Resistance | Good | Excellent |
Toughness | High | Moderate |
Corrosion Resistance | Moderate | Good |
Machinability | Good | Moderate |
Applications | Dies, Forming Tools | Punches, Blades, Dies |
Which Tool Steel Is Best for Your Needs?
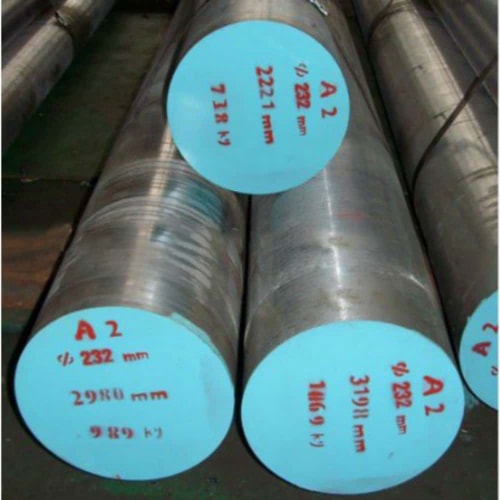
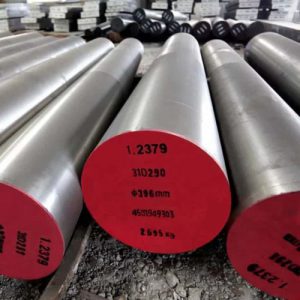
Now that we’ve explored the properties of A2 and D2 tool steels, it’s time to understand how each performs in various applications. Choosing between A2 vs D2 tool steel depends largely on the specific demands of your project. Whether you’re selecting steel for precision tools, cutting equipment, or heavy-duty machinery, the right choice will hinge on your priorities—whether that’s wear resistance, toughness, machinability, or overall performance in high-stress environments.
To make an informed decision, it’s important to evaluate how the distinct characteristics of A2 vs D2 tool steel affect performance under different conditions. Let’s look at how these steels compare when applied in specific industrial uses.
A2 Tool Steel in Action
A2 tool steel is a highly versatile material commonly used in cold work applications where toughness and wear resistance are critical. The key to A2’s effectiveness is its ability to resist cracking under sudden impacts, making it ideal for tools and components that will experience stress or fatigue. This steel has a medium carbon content, coupled with high chromium levels, making it both durable and capable of withstanding abrasive forces.
Applications of A2 Tool Steel:
- Dies and Molds: A2 is an excellent choice for manufacturing dies and molds, especially in industries like automotive and aerospace where precision and durability are key. Its good machinability allows for detailed shaping and fine-tuning during the manufacturing process.
- Cutting Tools: A2 is often used for cutting tools, such as blades and punches, because it combines wear resistance with toughness. It is particularly effective in situations where tools will experience shock or moderate heat.
- Forming Tools: A2’s ability to maintain its integrity under pressure makes it suitable for producing forming tools. These tools are used to shape and mold materials, and A2’s toughness ensures they can handle the repeated stresses without failure.
A2 vs D2 tool steel: A2 excels in applications where a balance of hardness and toughness is essential. Its superior toughness makes it better at absorbing shock and resisting cracking, which is crucial when dealing with high-impact tasks.
D2 Tool Steel in Action
D2 tool steel, with its higher carbon and chromium content, is designed for applications that demand exceptional wear resistance and hardness. The steel’s ability to hold an edge for extended periods of time makes it ideal for cutting tools, dies, and blades that will be exposed to continuous abrasion. However, despite its hardness, D2 is less tough than A2 and can crack or break under sudden impact, which limits its use in applications where impact resistance is critical.
Applications of D2 Tool Steel:
- Cutting Blades and Knives: D2 is commonly used for manufacturing cutting blades, knives, and other high-wear components. Its ability to retain a sharp edge makes it ideal for applications that require prolonged cutting or shearing without frequent sharpening.
- Punches and Dies: Due to its high hardness, D2 is frequently used in punch and die manufacturing, where resistance to wear is critical. The material’s durability ensures that tools last longer in high-stress, high-abrasion environments.
- Shear Blades: D2’s wear resistance is also highly valued in the production of shear blades, which are used in a variety of cutting and processing tasks. D2’s hardness enables it to handle the significant stresses and abrasions involved in cutting thick materials.
In terms of A2 vs D2 tool steel, D2 is the go-to material for applications requiring superior wear resistance and edge retention. Its higher hardness gives it an advantage when it comes to maintaining sharpness, making it highly effective in high-abrasion environments. However, its toughness is not as strong as A2’s, and under extreme conditions, it can crack.
A2 vs D2 Tool Steel: Choosing the Right Steel for Your Needs

When deciding between A2 vs D2 tool steel, consider the specific demands of your project. If your application requires a steel that balances toughness with wear resistance, A2 tool steel may be the better option. A2 vs D2 tool steel is often compared in scenarios where materials are subjected to impact or varying loads, such as in manufacturing processes or tooling used in complex machinery. A2’s superior toughness makes it an ideal choice for such applications.
On the other hand, if your focus is on applications where wear resistance and edge retention are paramount, D2 tool steel might be the ideal choice. When comparing A2 vs D2 tool steel, D2 provides exceptional hardness and resists wear better than A2, making it suitable for high-wear environments. However, it’s important to note that D2 is more prone to cracking under impact. If your project involves applications where extreme toughness and shock resistance are crucial, A2 tool steel may outperform D2.
In short, A2 vs D2 tool steel comes down to your project’s priorities. Do you need a steel that withstands heavy impacts and maintains integrity under pressure, as A2 does? Or are you looking for a material, like D2, that retains its edge under continuous abrasion? Both A2 vs D2 tool steel options have their merits, and your choice should align with the specific demands of your industry and applications.
Conclusion
The battle between A2 and D2 tool steels boils down to their strengths and weaknesses. A2 tool steel offers superior toughness and better machinability, making it ideal for tools exposed to sudden impacts or requiring complex shaping. On the other hand, D2 tool steel excels in applications that prioritize wear resistance, hardness, and edge retention.
When deciding between A2 vs D2 tool steel, consider the specific needs of your project. If your tools are exposed to high wear, D2 may be the better option. However, if you need better toughness and resistance to sudden impacts, A2 tool steel might be your best choice.
FAQ
What is the main difference between A2 and D2 tool steel?
The main difference lies in their wear resistance and toughness. A2 offers better toughness, while D2 excels in wear resistance and hardness.
Which steel is better for cutting tools?
D2 is often preferred for cutting tools due to its high hardness and wear resistance, especially in applications involving prolonged friction.
Can A2 tool steel be used for high-stress applications?
Yes, A2 tool steel is excellent for high-stress applications that require toughness, such as forming tools, punches, and dies.
Is D2 tool steel more corrosion-resistant than A2?
Yes, D2 tool steel has better corrosion resistance due to its higher chromium content compared to A2.
Which tool steel is easier to machine, A2 or D2?
A2 tool steel is easier to machine than D2, making it a better option for applications where precision machining is required.