Welcome to My Blog! 🌟
Before we dive into the content, I’d love for you to join me on my social media platforms. It’s where I share more insights, engage with our vibrant community, and post regular updates. Here’s how you can stay connected:
📘 Facebook: Connect with me on Facebook
Now, let’s embark on this journey together. I hope you find the content here insightful, engaging, and most importantly, valuable. Let’s explore, learn, and grow together! 🚀
Table of Contents
Introduction
S7 tool steel is known for its excellent toughness and high-impact resistance, making it a preferred choice for manufacturing tools that must endure repeated stress. However, even with its desirable properties, improper handling, application, or maintenance can lead to premature failure. Understanding why s7 tool steel fails and how to prevent such issues is essential for extending tool life and improving operational efficiency. This blog will explore common mistakes that contribute to the failure of s7 tool steel and provide practical solutions to maximize its performance.
What Makes S7 Tool Steel Unique?
S7 tool steel is an air-hardening, shock-resistant grade widely utilized in demanding applications involving cold work and high-impact forces. Its chemical composition, which includes significant amounts of chromium, molybdenum, and vanadium, provides an impressive combination of durability and strength. Compared to other alloys in the same category, this material offers a unique balance of hardness and impact resistance, making it a go-to choice for fabricating tools like punches, dies, chisels, and similar components.
Key features of s7 tool steel:
- High resistance to impact loading
- Moderate capability to resist wear
- Ability to harden in air, reducing distortion risks
- Exceptional machinability in its annealed form
4 Common Mistakes That Lead to Material Failure
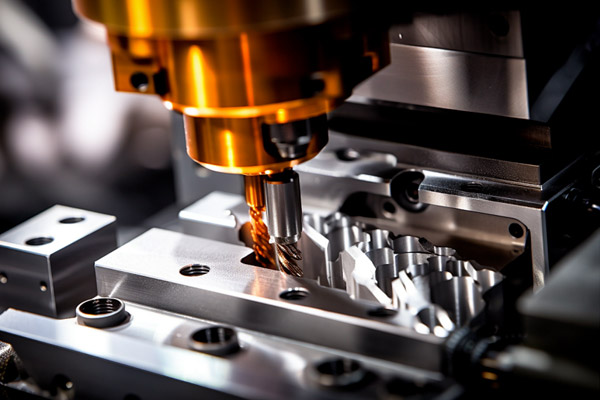
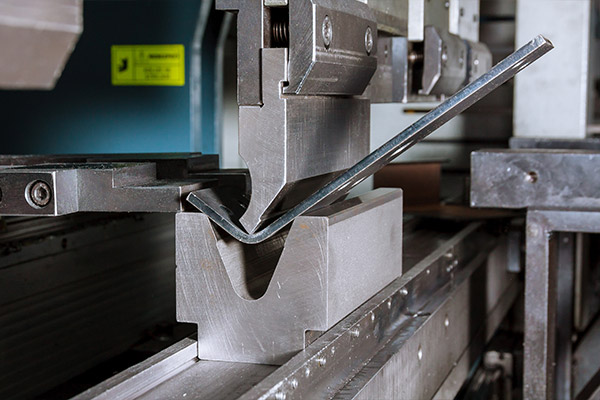
1. Improper Heat Treatment Procedures
One of the most frequent causes of tool degradation with this alloy arises from flawed heat treatment methods. Proper hardening and tempering require adherence to specific temperature ranges and cooling protocols. Deviating from recommended procedures can cause brittleness, reduced hardness, loss of dimensional accuracy, or even structural deformation.
Heat treatment plays a vital role in determining the final properties of any shock-resistant steel, particularly in demanding applications. If overheating occurs, the microstructure may become coarse, significantly lowering impact resistance. Likewise, inadequate soaking time during the austenitizing phase may lead to non-uniform hardness across the tool, weakening its structural integrity.
Mistake Details:
- Excessive temperature during the hardening phase, leading to grain growth and reduced ductility
- Inadequate soaking time at the austenitizing temperature, resulting in uneven hardness
- Incorrect tempering range selection, which may either over-soften or leave the tool too brittle
Solution: Strictly adhere to guidelines provided by manufacturers or metallurgical standards. Use calibrated furnaces and advanced temperature monitoring systems to ensure precision. It’s also crucial to monitor the part’s temperature during the quenching process and employ proper cooling mediums and rates suited for this steel’s characteristics.
2. Using the Wrong Tool Design
Even when crafted from a robust material, tools can fail if the underlying design is flawed. Design issues such as sharp internal corners, thin cross-sections, or inadequate support geometry often act as stress risers. Under operational stress, these areas become prone to cracking or structural failures.
Tools made from this alloy must be designed with its specific mechanical properties in mind. Overlooking proper geometrical transitions or loading conditions may render even high-quality tools ineffective.
Mistake Details:
- Lack of radius or fillets in critical areas, concentrating stress
- Insufficient material in load-bearing sections, compromising structural integrity
- Design not suited to the operational stresses, such as torsion or repeated impact
Solution: Collaborate with skilled tool designers familiar with this alloy’s behavior under different stress conditions. Leverage CAD-based stress simulations to identify and reinforce vulnerable areas. Design features should include proper radii at all corners, uniform section thicknesses, and adequate support structures to distribute loads evenly.
3. Poor Surface Finish and Machining Practices
Rough surfaces and suboptimal machining methods can introduce surface flaws that evolve into cracks when subjected to repetitive stress. This is particularly concerning in tools exposed to cyclic loading, impact, or vibration.
Improper machining can cause the formation of micro-cracks or residual stresses, which may act as initiation sites for fatigue failure. Using dull tools or applying improper cutting speeds without coolant can generate excessive heat, leading to surface hardening or material pullout.
Mistake Details:
- Employing blunt or worn-out cutting tools, causing uneven or rough cuts
- Omitting essential finishing processes like polishing or stress-relief treatments
- Machining at high speeds without adequate cooling, resulting in thermal damage or warping
Solution: Choose machining parameters that match the material’s hardness and toughness. Always complete the fabrication process with polishing or surface conditioning techniques suitable for high-performance alloys. Apply sufficient lubrication and cooling fluids during high-speed operations to minimize thermal effects and improve surface integrity.
4. Ignoring Maintenance and Tool Wear
Even materials engineered for resilience degrade over time. Neglecting inspections or routine upkeep leads to fatigue-related failures that could have been prevented with proactive maintenance. The harsh environments in which impact-resistant steels are used tend to subject tools to repeated mechanical and thermal stress, eventually leading to fatigue, wear, or microstructural changes.
Tool failure often begins with minor damage such as edge chipping, pitting, or surface fatigue. If left unaddressed, these defects can propagate into cracks or catastrophic failure during service.
Mistake Details:
- Skipping routine inspections, allowing minor flaws to escalate
- Continuing use despite visible wear like cracks, dull edges, or deformation
- Lack of reconditioning processes to restore tool surfaces and edge geometry
Solution: Implement regular inspection schedules using visual, ultrasonic, or magnetic particle testing, especially in high-impact applications. Document wear patterns to forecast tool lifespan and determine the optimal time for reconditioning. Establish tool maintenance protocols that include surface regrinding, stress-relief treatments, and timely replacement of worn-out parts to ensure consistent performance.
Common Applications and Recommended Conditions for S7 Tool Steel
To better understand where s7 tool steel works best and how it can fail, the following table outlines common applications and their ideal working conditions:
Application | Operating Conditions | Potential Failure Causes | Recommended Practice |
---|---|---|---|
Punching Tools | High shock, low wear | Brittle fracture from poor temper | Use correct tempering range |
Shear Blades | Moderate wear, high load | Edge cracking | Ensure sharp edges and finish |
Chisels | Repetitive impacts | Deformation due to overheating | Controlled heat treatment |
Injection Molds | Cyclic thermal stress | Thermal fatigue cracking | Preheating before usage |
Forging Dies | Extreme pressure, heat cycles | Surface spalling | Routine inspection and polishing |
How to Prevent S7 Tool Steel Failures
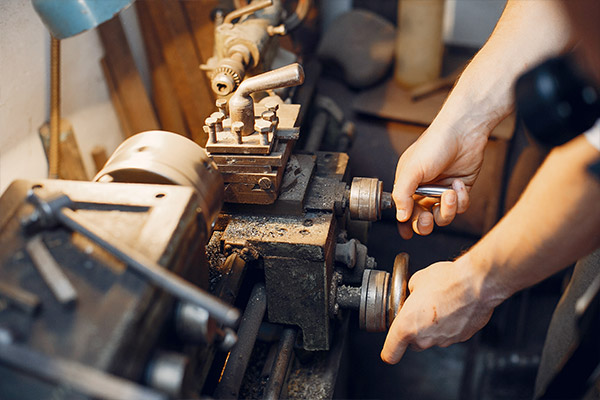
Understanding the root causes of failure is the first step toward enhancing the reliability and longevity of any tool made from this high-performance alloy. By addressing the common oversights that lead to premature wear or catastrophic failure, manufacturers and machinists can greatly improve operational efficiency and reduce downtime.
Successful prevention begins with a commitment to best practices in every phase of the tool’s lifecycle—from design to maintenance.
- Strict adherence to heat treatment protocols
- Well-thought-out design considering load and geometry
- High-quality machining with final surface enhancement
- Regular maintenance and tracking wear over time
Training operators and engineers on material-specific characteristics also reduces human error in tool handling.
Conclusion
S7 tool steel offers outstanding benefits in tough working environments, but to fully harness its potential, users must avoid the common mistakes that lead to failure. Whether it’s refining the heat treatment process, optimizing tool design, or establishing a maintenance routine, each step contributes to the overall longevity and effectiveness of tools made from s7 tool steel. By understanding its behavior and handling it correctly, industries can maximize both safety and productivity while minimizing tool replacement costs.
This knowledge not only improves your results but also ensures you get the most from one of the most reliable materials available in modern tool engineering.
FAQ
What is the ideal hardness for s7 tool steel after heat treatment?
Typically, s7 tool steel reaches 54–56 HRC after proper heat treatment, depending on the cooling rate and tempering cycle used.
Can s7 tool steel be welded?
Yes, but preheating and post-weld heat treatment are necessary to reduce the risk of cracking due to the steel’s high hardenability.
What makes s7 tool steel different from other tool steels?
Its unique combination of impact resistance and toughness distinguishes it from other grades, making it suitable for shock-loading applications.
How often should tools made from s7 tool steel be inspected?
Inspection intervals depend on usage, but a weekly visual inspection and monthly detailed check are recommended for high-impact tools.
Is s7 tool steel corrosion resistant?
Not inherently. For applications exposed to moisture, additional surface treatments or coatings are advised.