Welcome to My Blog! 🌟
Before we dive into the content, I’d love for you to join me on my social media platforms. It’s where I share more insights, engage with our vibrant community, and post regular updates. Here’s how you can stay connected:
📘 Facebook: Connect with me on Facebook
Now, let’s embark on this journey together. I hope you find the content here insightful, engaging, and most importantly, valuable. Let’s explore, learn, and grow together! 🚀
Table of Contents
Introduction
High-speed steel, commonly referred to as hss material, continues to play a significant role across various manufacturing industries in 2025. Known for its durability, hardness, and versatility, this material is particularly favored in machining, drilling, and cutting applications. While there are numerous advanced materials available today, hss material still maintains its relevance due to its exceptional performance-to-cost ratio. This blog explores the top 10 advantages of using hss material in the modern era and explains why it remains a preferred choice.
NO 1. Superior Wear Resistance in HSS Material
One of the standout advantages of this high-performance steel is its remarkable resistance to wear. This characteristic is vital for tools operating at elevated speeds, where they endure significant levels of friction, intense heat, and mechanical stress. The presence of alloying components such as tungsten, molybdenum, and vanadium enhances the tool’s ability to maintain its form and sharpness even under constant abrasion. These qualities make it an excellent option for manufacturing environments that demand both consistency and precision over extended periods of operation. Whether it’s cutting, drilling, or milling, the wear resistance of this alloy ensures that tools maintain accuracy and durability far longer than many conventional alternatives.
NO 2. Cost-Effectiveness Compared to Alternatives
Although advanced materials like carbide and ceramic composites have gained popularity in certain sectors, high-speed steel still holds a strong position when it comes to balancing cost with performance. It provides reliable results without the premium price tag, which is a crucial consideration for businesses that are mindful of operational budgets. Small and medium-sized enterprises, in particular, often benefit from choosing this type of tooling because of its affordability and solid track record. Furthermore, the extended tool life associated with this alloy results in fewer replacements and lower overall maintenance costs, making it a smart investment over time.
NO 3. High Toughness for Demanding Applications
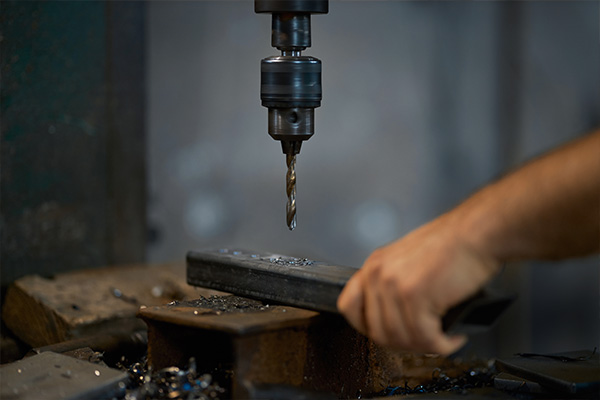
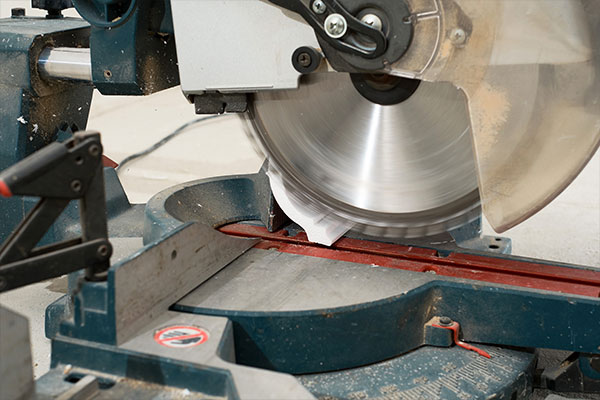
Another major strength of this steel category lies in its impressive toughness. This refers to the material’s ability to absorb impact and resist cracking or fracturing during use—especially important in operations where cutting is not continuous. Applications like interrupted turning or rough milling can put a lot of strain on tools, but thanks to its robust structure, this alloy holds up exceptionally well. That resilience not only extends the working life of the equipment but also enhances safety for machine operators, reducing the risk of sudden breakage during critical jobs. It’s especially suitable for machining harder metals that require strength and shock resistance.
NO 4. Excellent Heat Resistance
A major factor contributing to the popularity of this engineering material is its performance at elevated temperatures. Unlike some other tool steels, it retains its hardness even when exposed to intense heat, which is common in high-speed machining environments. This heat resistance means tools won’t easily lose their cutting edge or structural integrity, even during extended runs. As a result, users can expect higher efficiency, reduced wear and tear, and longer operational periods between maintenance or replacement cycles. The ability to remain stable under thermal stress is one of the reasons why it’s favored in demanding industrial settings.
NO 5. Versatility Across Multiple Applications
Few materials match the broad usability of this alloy in modern machining. Its flexibility makes it a staple across a wide range of industries including automotive, aerospace, and general manufacturing. Whether used in drill bits, taps, reamers, or end mills, its adaptability allows it to serve multiple roles with high reliability. This kind of universal application reduces the need for stocking numerous specialty tools, streamlining production processes and simplifying procurement. Because of its balanced properties and dependable results, it continues to be a preferred choice in both large-scale operations and smaller workshops alike.
Comparative Properties of HSS Material
Below is a table comparing hss material with other commonly used tool materials in terms of key performance indicators:
Property | HSS Material | Carbide | Ceramic | CBN |
---|---|---|---|---|
Wear Resistance | High | Very High | Moderate | Excellent |
Toughness | Very High | Low | Very Low | Moderate |
Heat Resistance | High | Very High | High | Excellent |
Cost | Moderate | High | Very High | Very High |
Ease of Resharpening | Easy | Difficult | Very Difficult | Difficult |
NO 6. Easy to Sharpen and Regrind
A practical but sometimes overlooked benefit of this cutting material is how easily it can be sharpened. Compared to harder and more brittle alternatives like carbide, this steel can be resharpened multiple times without compromising its integrity. That means when the tool begins to dull, it doesn’t have to be discarded—it can simply be reground and reused, maintaining its original performance. This feature is especially advantageous in workshops and manufacturing environments where in-house tool maintenance is standard practice. Over the tool’s lifespan, the ability to regrind it multiple times translates to significant cost savings and greater resource efficiency.
NO 7. Enhanced Surface Finish
Tools made from this alloy offer more than just durability—they also contribute to a cleaner, smoother surface on the finished part. The material’s cutting capabilities are characterized by stable performance and low vibration during use, which reduces imperfections on the workpiece. As a result, operators benefit from an improved surface finish that often eliminates the need for additional post-machining processes such as polishing or grinding. This not only shortens production times but also helps preserve dimensional accuracy, which is essential in industries that demand precision, such as aerospace and medical device manufacturing.
NO 8. Availability and Global Standardization
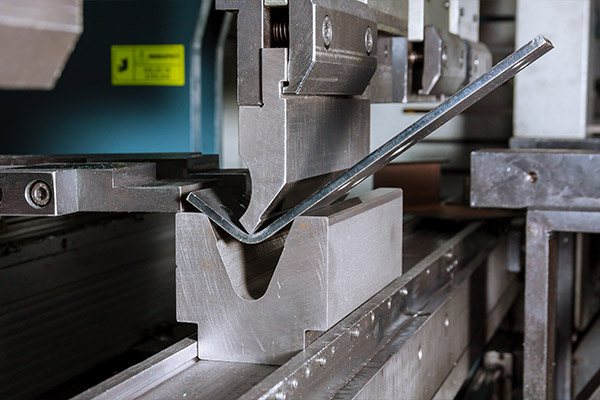
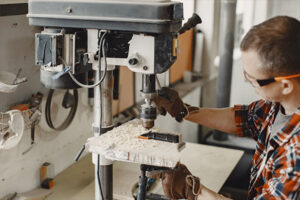
Another advantage is the widespread availability and standardization of this tool-grade steel. It is manufactured in compliance with international specifications, which ensures consistency in quality no matter where it’s sourced. Whether you’re operating in North America, Europe, or Asia, finding compatible replacements or supplementary tooling made from the same composition is straightforward. This universality simplifies inventory management and procurement, making it easier for global companies to maintain tooling standards across multiple facilities. For procurement teams, this predictability means fewer surprises in supply chain operations and better long-term planning.
NO 9. Compatibility with Coatings
Modern hss material can be enhanced with various coatings like titanium nitride (TiN) or aluminum titanium nitride (AlTiN), which improve tool life, reduce friction, and enhance performance in demanding tasks. This makes the material even more adaptable to high-tech environments.
NO 10. Environmentally Friendly Option
Sustainability is becoming increasingly important across all industries, and this material offers clear environmental benefits. Not only is it recyclable, but it also requires relatively less energy during manufacturing compared to more exotic alloys. Once a tool reaches the end of its service life, it can be collected, melted down, and repurposed into new tools or components, reducing landfill waste and supporting circular economy practices. Additionally, the long service life and ability to regrind mean fewer tools are produced and disposed of over time, minimizing environmental impact. Companies striving for greener production will find this steel to be a conscious and responsible choice.
Conclusion
In 2025, hss material remains a compelling choice for a wide array of applications. From its excellent wear and heat resistance to its cost-effectiveness and environmental benefits, this material delivers a comprehensive set of advantages that meet the evolving needs of modern industries. While newer materials may offer specific benefits in niche applications, the overall performance, reliability, and availability of hss material ensure its ongoing relevance and demand.
FAQ
What does HSS material stand for?
HSS stands for High-Speed Steel, a category of tool steel known for its hardness, toughness, and heat resistance.
Is HSS material better than carbide?
It depends on the application. HSS is more affordable and tougher, while carbide offers higher wear resistance but is more brittle.
Can HSS material be used for stainless steel?
Yes, with the right coatings and speeds, HSS tools can efficiently cut stainless steel and other tough metals.
How long does HSS material last?
Tool life depends on usage, but HSS tools can last a long time, especially when properly maintained and resharpened.
Is HSS material recyclable?
Yes, HSS material is recyclable, which contributes to its eco-friendly profile and sustainability in industrial use.