Welcome to My Blog! 🌟
Before we dive into the content, I’d love for you to join me on my social media platforms. It’s where I share more insights, engage with our vibrant community, and post regular updates. Here’s how you can stay connected:
📘 Facebook: Connect with me on Facebook
Now, let’s embark on this journey together. I hope you find the content here insightful, engaging, and most importantly, valuable. Let’s explore, learn, and grow together! 🚀
Table of Contents
Introduction
Stainless steel is known for its durability, corrosion resistance, and versatility. However, there are different grades of stainless steel, each tailored to specific environments and uses. A2 vs A4 stainless steel are two such grades that often come up in comparison, particularly when discussing fasteners, hardware, and other industrial applications. Understanding the distinctions between A2 vs A4 stainless steel will help you choose the material that best fits your requirements. This article will cover the properties, advantages, and ideal uses of both materials.
What is A2 Stainless Steel?
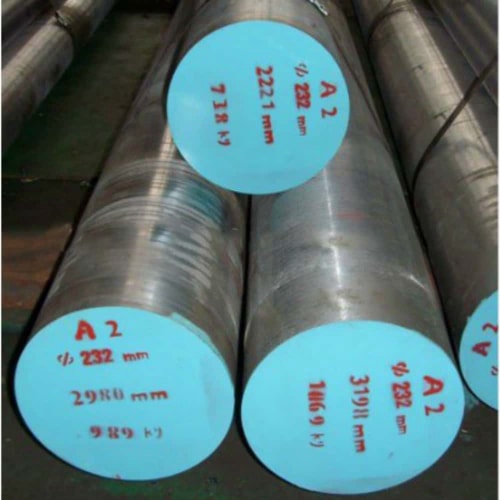
A2 stainless steel, also known as 304 stainless steel, is one of the most common grades in the austenitic family. It is widely used in a range of applications where corrosion resistance and strength are important. A2 stainless steel is made with a combination of iron, chromium, and nickel, providing a balance of durability, strength, and resistance to rust and corrosion.
Key Characteristics of A2 Stainless Steel
- Composition: Contains around 18% chromium and 8% nickel.
- Corrosion Resistance: Provides good corrosion resistance in many environments, though it is less resistant to certain chemicals and seawater.
- Strength: Strong enough for most applications, but not ideal for highly corrosive environments.
- Magnetic Properties: A2 stainless steel is magnetic, which can be important in specific applications.
Ideal Uses for A2 Stainless Steel
A2 stainless steel is often used in industries such as construction, automotive, food processing, and general manufacturing. Its resistance to rust makes it suitable for applications where exposure to moisture or mild chemicals is expected.
What is A4 Stainless Steel?
A4 stainless steel, also known as 316 stainless steel, is another common grade in the austenitic family. A4 stainless steel is often considered the next step up from A2 in terms of corrosion resistance. It is particularly known for its ability to withstand more aggressive environments, including exposure to seawater and harsh chemicals.
Key Characteristics of A4 Stainless Steel
- Composition: Contains around 16% chromium, 10% nickel, and 2% molybdenum.
- Corrosion Resistance: Excellent resistance to corrosion, particularly in chloride environments such as seawater.
- Strength: Similar to A2 stainless steel in terms of strength but better suited for more demanding environments.
- Magnetic Properties: A4 stainless steel is also non-magnetic, which may be important for certain industrial uses.
Ideal Uses for A4 Stainless Steel
Due to its superior corrosion resistance, A4 stainless steel is used in industries such as marine, chemical processing, pharmaceuticals, and food processing where exposure to harsh chemicals or saltwater is a concern.
A2 vs A4 Stainless Steel: A Comparison
Property | A2 Stainless Steel (304) | A4 Stainless Steel (316) |
---|---|---|
Corrosion Resistance | Good, but can be affected by chemicals | Excellent, highly resistant to chemicals and seawater |
Composition | 18% chromium, 8% nickel | 16% chromium, 10% nickel, 2% molybdenum |
Magnetic Properties | Magnetic | Non-magnetic |
Strength | Strong, suitable for most applications | Stronger in harsh environments |
Cost | Generally more affordable | Higher cost due to added molybdenum |
Common Applications | Food processing, automotive, construction | Marine, pharmaceuticals, chemical processing |
Advantages of A2 Stainless Steel
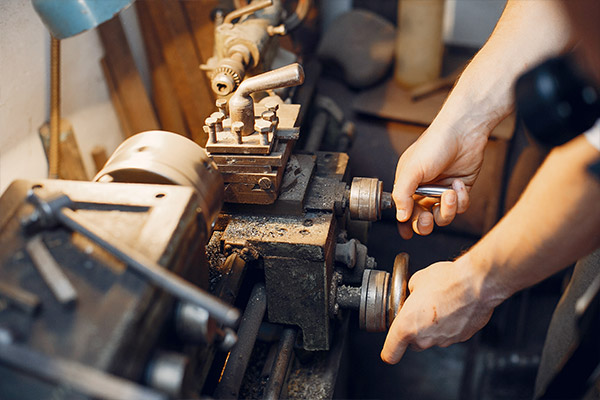
A2 stainless steel offers several benefits, making it a popular choice for many applications.
- Affordable: A2 stainless steel is typically less expensive than A4, making it a budget-friendly option for many applications.
- Versatile: It can be used in a wide range of environments and industries.
- Easy to Fabricate: A2 stainless steel is easier to work with in terms of cutting, welding, and machining.
Advantages of A4 Stainless Steel
A4 stainless steel provides distinct advantages in certain environments, especially when corrosion resistance is a critical factor.
- Superior Corrosion Resistance: The addition of molybdenum in A4 stainless steel significantly enhances its ability to resist corrosion, particularly in harsh conditions like marine environments.
- Longevity: A4 stainless steel is better suited for long-term use in aggressive conditions, reducing the need for replacements or repairs.
- Non-Magnetic: Its non-magnetic nature can be beneficial in specific industrial applications.
A2 vs A4 Stainless Steel: Which One Should You Choose?
The choice between A2 vs A4 stainless steel largely depends on the specific requirements of your project.
- Choose A2 Stainless Steel if:
- You need a versatile material that can be used in various industries.
- You are working in environments with mild exposure to chemicals or moisture.
- Budget is a significant concern, and you don’t need the highest level of corrosion resistance.
- Choose A4 Stainless Steel if:
- Your application involves exposure to harsh environments, such as seawater or aggressive chemicals.
- You require the best possible corrosion resistance for long-term use.
- Cost is less of a concern, and durability is a priority.
Conclusion
In the debate of A2 vs A4 stainless steel, both materials offer unique properties that make them suitable for different applications. A2 stainless steel is an excellent all-rounder that is cost-effective and versatile, making it ideal for most general applications. On the other hand, A4 stainless steel is the preferred choice for demanding environments where superior corrosion resistance is essential, especially in marine and chemical industries. By considering the specific needs of your project, whether it’s budget constraints or the need for high resistance to corrosion, you can make an informed decision about which stainless steel grade—A2 vs A4 Stainless Steel—is right for you.
FAQ
What is the main difference between A2 vs A4 stainless steel?
The primary difference is in their corrosion resistance. A2 stainless steel offers good corrosion resistance but is not as resistant to aggressive environments as A4 stainless steel, which has enhanced resistance due to the addition of molybdenum.
Is A2 stainless steel magnetic?
Yes, A2 stainless steel is magnetic. This is a key factor to consider when choosing between A2 vs A4 stainless steel for certain industrial applications. The magnetic properties of A2 stainless steel arise from its composition, which includes iron as a primary component. This feature can be advantageous in applications where magnetic properties are needed, such as in certain machinery or magnetic fasteners. In contrast, A4 stainless steel (316 stainless steel) is typically non-magnetic, which might be more suitable for specific uses where magnetism could interfere with the operation of sensitive equipment or machinery.
Is A4 stainless steel more expensive than A2?
Yes, A4 stainless steel is generally more expensive than A2 stainless steel. The price difference between A2 vs A4 stainless steel primarily stems from the inclusion of molybdenum in the A4 grade, which enhances its corrosion resistance and makes it better suited for more demanding environments. The addition of molybdenum increases the production costs, resulting in A4 stainless steel being more expensive compared to A2. However, the superior corrosion resistance offered by A4 stainless steel justifies the higher price for applications where long-term durability in aggressive environments is essential.
Can I use A2 stainless steel in marine applications?
While A2 stainless steel can be used in marine applications, it is generally not the ideal choice for environments that experience prolonged exposure to seawater. In the A2 vs A4 stainless steel comparison, A4 stainless steel (316 stainless steel) is the preferred option for marine applications due to its enhanced resistance to corrosion caused by chloride ions, which are prevalent in seawater. A2 stainless steel, although durable in many environments, is more susceptible to pitting and crevice corrosion in marine settings. Therefore, if your project involves exposure to seawater or other highly corrosive environments, A4 stainless steel would be a more reliable and long-lasting material.
Which stainless steel is better for food processing?
Both A2 vs A4 Stainless Steel are commonly used in food processing, but A2 (304) stainless steel is generally sufficient for most food-related applications. It offers good corrosion resistance and is easy to clean, making it an ideal choice for a wide range of food processing environments. However, if the environment is highly corrosive, such as exposure to acidic foods, harsh cleaning chemicals, or saltwater, A4 (316) stainless steel may be preferred. A4 stainless steel provides superior resistance to corrosion, ensuring durability and reliability in more aggressive food processing environments. Therefore, when considering A2 vs A4 Stainless Steel for food processing, A2 is typically adequate for most applications, but A4 should be selected for more demanding conditions.