Welcome to My Blog!
Before we dive into the content, I’d love for you to join me on my social media platforms where I share more insights, engage with the community, and post updates. Here’s how you can connect with me:
Facebook:https://www.facebook.com/profile.php?id=100090797846538
Now, let’s get started on our journey together. I hope you find the content here insightful, engaging, and valuable.
Table of Contents
Introduction
When it comes to selecting the right tool steel for manufacturing, the debate often centers around O1 vs A2 Steel. Both materials are renowned for their unique properties and applications, making them popular choices in various industries. However, they also come with their own set of weaknesses that can significantly impact their performance and suitability for specific tasks. Understanding these hidden drawbacks is crucial for making an informed decision, especially when precision, durability, and cost-effectiveness are critical factors.
O1 vs A2 Steel are often compared due to their distinct hardening processes and alloy compositions. O1 steel, known for its oil-hardening properties, offers excellent hardness and wear resistance, making it a favorite for cutting tools and knives. On the other hand, A2 steel, an air-hardening tool steel, is prized for its dimensional stability and reduced risk of cracking, making it ideal for die-making and precision components. While both materials have their strengths, their weaknesses can be just as important to consider, particularly in high-stress or high-impact applications.
This blog will delve into the weaknesses of O1 vs A2 Steel, comparing their properties, applications, and potential pitfalls. By exploring factors such as brittleness, toughness, dimensional stability, and cost, we aim to provide a comprehensive analysis that will help you choose the best material for your specific needs. Whether you are designing cutting tools, industrial machinery, or precision dies, understanding the limitations of these steels can help you avoid costly mistakes and ensure the longevity and reliability of your products.
What are O1 and A2 Steel?
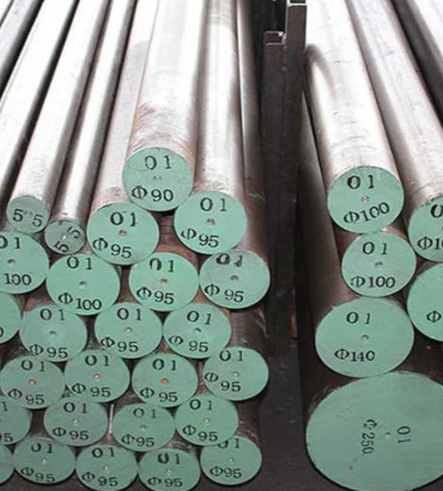
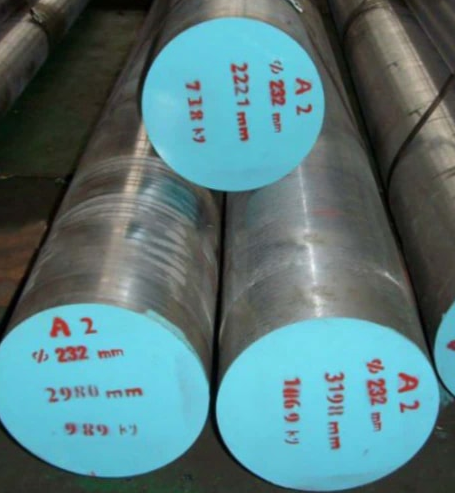
Composition and Properties of O1 Steel
O1 steel is an oil-hardening tool steel that contains a balanced mix of carbon, manganese, chromium, and tungsten. Its composition gives it excellent hardness and wear resistance, making it ideal for cutting tools, knives, and other high-wear applications. However, its oil-hardening process can lead to certain weaknesses, such as brittleness and dimensional instability.
Composition and Properties of A2 Steel
A2 steel is an air-hardening tool steel that contains carbon, chromium, molybdenum, and vanadium. Its air-hardening capability provides better dimensional stability and reduced risk of cracking compared to O1 steel. A2 steel is commonly used in die-making, punches, and other precision tools. Despite its advantages, A2 steel also has its own set of weaknesses, including lower toughness and higher cost.
Key Weaknesses of O1 vs A2 Steel
Brittleness and Dimensional Instability in O1 Steel
One of the primary weaknesses of O1 steel is its brittleness. The oil-hardening process can make the material more prone to cracking and chipping under high stress. Additionally, O1 steel can suffer from dimensional instability during the hardening process, leading to warping or distortion. These issues can compromise the performance and longevity of tools made from O1 steel.
Lower Toughness in A2 Steel
While A2 steel offers better dimensional stability, it is not without its drawbacks. One of the main weaknesses of A2 steel is its lower toughness compared to O1 steel. This reduced toughness can make A2 steel more susceptible to breaking or fracturing under heavy impact or shock loading. As a result, A2 steel may not be the best choice for applications that require high impact resistance.
Cost Considerations
Another factor to consider when comparing O1 vs A2 Steel is cost. A2 steel is generally more expensive than O1 steel due to its complex alloying elements and air-hardening process. This higher cost can be a significant drawback for manufacturers working with tight budgets. On the other hand, while O1 steel is more affordable, its potential for brittleness and dimensional instability can lead to higher long-term costs due to frequent replacements or repairs.
Applications and Performance
When comparing O1 vs A2 Steel, understanding their performance in specific applications is crucial for making the right choice. Both materials have unique strengths and weaknesses that make them suitable for different tasks, ranging from cutting tools to industrial machinery. Below, we explore how O1 vs A2 Steel perform in key applications, highlighting their advantages and limitations.
Cutting Tools and Knives
O1 steel is often used in cutting tools and knives due to its excellent hardness and wear resistance. However, its brittleness can be a significant drawback in these applications, as it may lead to chipping or cracking under heavy use. A2 steel, while not as hard, offers better dimensional stability and can be a more reliable choice for precision cutting tools that require consistent performance.
Die-Making and Punches
A2 steel is commonly used in die-making and punches due to its air-hardening capability and dimensional stability. However, its lower toughness can be a weakness in high-impact applications, where the material may be prone to breaking or fracturing. O1 steel, with its higher toughness, may be a better choice for dies and punches that need to withstand heavy impact, despite its potential for dimensional instability.
Industrial Machinery
Both O1 and A2 steel are used in various industrial machinery applications. O1 steel’s hardness and wear resistance make it suitable for components that experience high wear, but its brittleness can be a drawback in high-stress environments. A2 steel’s dimensional stability and reduced risk of cracking make it a better choice for precision components, though its lower toughness and higher cost can be limiting factors.
By carefully evaluating the strengths and weaknesses of O1 vs A2 Steel in different applications, manufacturers can make informed decisions that optimize performance, durability, and cost-effectiveness. Whether prioritizing hardness, toughness, or dimensional stability, understanding how these materials perform in real-world scenarios is key to selecting the right steel for the job.
Table: Comparison of O1 vs A2 Steel
Property | O1 Steel | A2 Steel |
---|---|---|
Hardness | High | Moderate |
Toughness | High | Low |
Dimensional Stability | Low | High |
Wear Resistance | Excellent | Good |
Cost | Low | High |
Brittleness | Prone to brittleness | Less brittle |
Impact Resistance | High | Low |
Environmental and Sustainability Considerations
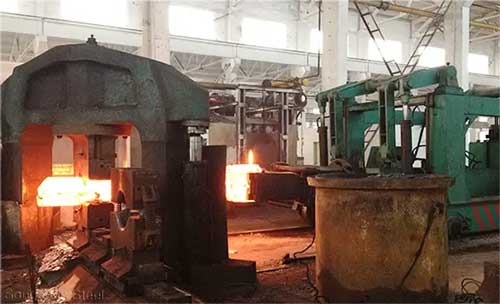
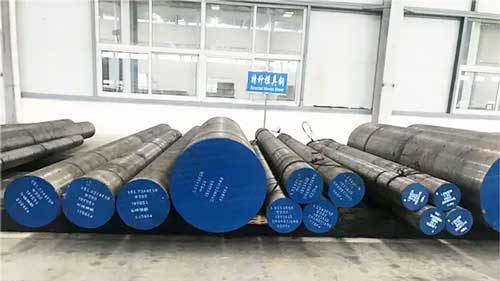
Recyclability
One of the key advantages of both O1 and A2 Steel is their full recyclability. This makes them valuable contributors to sustainable manufacturing practices, as they can be reused without losing their essential properties. Recycling these steels helps reduce waste and conserve natural resources, aligning with global efforts to promote circular economies. However, there are differences in the recycling processes and environmental impact of O1 vs A2 Steel.
O1 steel, with its simpler composition and lower alloying elements, is generally easier to recycle. Its straightforward chemical makeup allows for efficient reprocessing, minimizing energy use and emissions during recycling. On the other hand, A2 steel contains more complex alloying elements, such as molybdenum and vanadium, which can complicate the recycling process. While A2 steel is still recyclable, the additional steps required to separate and reprocess its components can make it less environmentally friendly compared to O1 steel.
Energy Efficiency
Energy consumption during production is another critical factor when comparing O1 vs A2 Steel. The manufacturing process for A2 steel involves air-hardening, which requires precise temperature control and longer cooling times. This, combined with its complex alloying elements, results in higher energy consumption during production. The increased energy use contributes to a larger carbon footprint, making A2 steel less energy-efficient than its counterpart.
In contrast, O1 steel undergoes an oil-hardening process, which is generally less energy-intensive. The simpler composition of O1 steel also reduces the energy required for melting and refining, further lowering its environmental impact. For manufacturers focused on reducing their carbon emissions and energy use, O1 steel may be the more sustainable choice. However, it’s important to weigh this advantage against its potential weaknesses, such as brittleness and dimensional instability.
Conclusion
When comparing O1 vs A2 Steel, it’s essential to consider their respective weaknesses alongside their strengths. O1 steel offers excellent hardness and wear resistance but can be brittle and dimensionally unstable. A2 steel provides better dimensional stability and reduced risk of cracking but suffers from lower toughness and higher cost. Understanding these hidden weaknesses can help you make an informed decision based on your specific application needs and budget constraints. Whether you prioritize toughness, dimensional stability, or cost-effectiveness, both materials have unique advantages and drawbacks that must be carefully weighed.
FAQ
What are the main weaknesses of O1 steel?
The main weaknesses of O1 steel include brittleness and dimensional instability. These issues can lead to cracking, chipping, and warping, compromising the performance and longevity of tools made from this material.
What are the main weaknesses of A2 steel?
The main weaknesses of A2 steel include lower toughness and higher cost. These factors can make A2 steel more susceptible to breaking or fracturing under heavy impact and less economical for manufacturers working with tight budgets.
Which steel is better for high-impact applications?
O1 steel is generally better for high-impact applications due to its higher toughness and impact resistance. However, its brittleness and dimensional instability can be drawbacks in precision applications.
Is A2 steel more expensive than O1 steel?
Yes, A2 steel is generally more expensive than O1 steel due to its complex alloying elements and air-hardening process. This higher cost can be a significant consideration for manufacturers.
Can both O1 and A2 steel be recycled?
Yes, both O1 and A2 steel are fully recyclable, contributing to sustainable manufacturing practices. However, the production of A2 steel requires more energy, resulting in a larger carbon footprint.