Welcome to My Blog!
Before we dive into the content, I’d love for you to join me on my social media platforms where I share more insights, engage with the community, and post updates. Here’s how you can connect with me:
Facebook:https://www.facebook.com/profile.php?id=100087990137347
LinkedIn:https://www.linkedin.com/company/89825762/admin/dashboard/
YouTube:www.youtube.com/@carbonsteelsupply-kj9lw
TikTok:www.tiktok.com/@carbonsteelsupply
Now, let’s get started on our journey together. I hope you find the content here insightful, engaging, and valuable.
Introduction
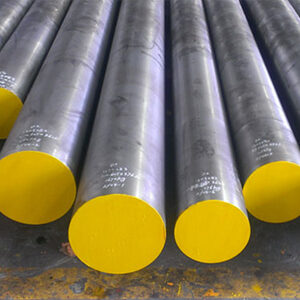
M42 tool steel, known for its exceptional hardness and high-speed cutting capabilities, is one of the most popular choices in tool-making and machining applications. Its outstanding toughness, wear resistance, and heat resistance make it ideal for challenging environments where regular steel might fail. This ultimate guide will walk you through the unique properties, applications, heat treatment process, and maintenance tips for M42 tool steel, providing everything you need to know about this high-performance material.
What is M42 Tool Steel?
M42 tool steel is a type of high-speed steel (HSS) with a high content of cobalt, specifically designed to perform at high speeds in challenging applications. As a member of the T1 and M2 family, M42 tool steel stands out for its enhanced hardness and temperature stability, with approximately 8-10% cobalt content that contributes to its superior performance under high temperatures.
Composition of M42 Tool Steel
M42 tool steel contains several key elements that contribute to its unique properties. The following table provides a breakdown of its typical composition:
Element | Percentage (%) |
---|---|
Carbon | 1.05 |
Tungsten | 1.75 |
Molybdenum | 9.50 |
Vanadium | 1.15 |
Chromium | 4.00 |
Cobalt | 8.00 |
The high cobalt content improves red-hardness, allowing the tool to retain its sharpness and cutting ability even at elevated temperatures.
Key Properties of M42 Tool Steel
The combination of these elements grants M42 tool steel several important properties:
- Hardness: M42 can reach a hardness of up to 68-70 HRC, making it ideal for high-speed cutting tools.
- Red-Hardness: M42 maintains its hardness at temperatures as high as 560°C, which is essential in high-speed operations.
- Wear Resistance: The high vanadium and molybdenum content enhances wear resistance, making M42 tools long-lasting.
- Toughness: Although extremely hard, M42 tool steel has adequate toughness to withstand cutting stresses without cracking.
Common Applications of M42 Tool Steel
M42 tool steel is widely used in applications requiring high-speed, precision cutting. Its ability to withstand heat and maintain sharpness under stress makes it valuable in the following industries:
- Machining and Tooling: Ideal for manufacturing drills, end mills, reamers, and other cutting tools.
- Aerospace: Used for high-strength components and precision cutting.
- Automotive: Common in tooling for automotive part manufacturing where durable, high-speed cutting tools are essential.
- Medical Equipment Manufacturing: Used for producing precise surgical instruments and other medical devices.
In all these applications, M42’s durability and cutting precision help reduce wear and downtime, resulting in longer tool life and higher efficiency.
Heat Treatment Process for M42 Tool Steel
The heat treatment of M42 tool steel is crucial in enhancing its performance and longevity. Here’s a step-by-step overview of the process:
- Preheating: Preheat to 450-500°C and then to 850-900°C.
- Austenitizing: Heat to 1200-1220°C, maintaining this temperature to achieve full hardness.
- Quenching: Quench in oil or air, depending on specific tool requirements.
- Tempering: Temper immediately after quenching at 540-590°C to achieve the desired hardness and toughness.
The following table shows typical hardness outcomes at different tempering temperatures:
Tempering Temperature (°C) | Hardness (HRC) |
---|---|
500 | 68 |
550 | 66 |
600 | 64 |
650 | 62 |
Note: Accurate temperature control during each step is essential to avoid structural defects and maximize M42 tool steel’s performance.
Advantages of Using M42 Tool Steel in High-Speed Cutting
M42 tool steel offers significant advantages for high-speed cutting, including:
- High Wear Resistance: Prolongs tool life, which is crucial in industrial applications.
- Superior Heat Resistance: Can withstand high temperatures without losing its cutting edge, reducing the need for frequent replacements.
- High Efficiency: Enables faster production rates due to its sharpness and durability.
- Cost-Effective: Although more expensive initially, the longer lifespan and reduced downtime make M42 tools economical over time.
Tips for Maintaining M42 Tool Steel Tools
To maximize the life and performance of M42 tool steel tools, follow these maintenance tips:
- Proper Storage: Store tools in a dry, cool place to prevent oxidation or rust.
- Avoid Overheating: Even though M42 tool steel is heat-resistant, excessive heat during grinding or sharpening can damage the tool.
- Regular Inspections: Periodically inspect tools for signs of wear and replace them as needed to ensure consistent performance.
- Lubrication: Apply suitable lubricants when machining to reduce heat build-up and minimize wear.
FAQ
Q1: Is M42 tool steel suitable for low-speed applications?
Yes, although M42 tool steel is optimized for high-speed applications, its toughness and wear resistance also make it suitable for low-speed tasks that require durability.
Q2: How does M42 compare to M2 tool steel?
M42 contains a higher percentage of cobalt, which gives it better red-hardness than M2. This makes M42 more suitable for high-temperature cutting operations.
Q3: Can M42 tool steel be welded?
Welding M42 tool steel is challenging due to its high hardness and brittleness; therefore, it’s generally recommended to avoid welding.
Q4: What industries commonly use M42 tool steel?
Industries such as aerospace, automotive, and medical manufacturing frequently use M42 tool steel for its durability in high-speed cutting applications.
Q5: What is the typical lifespan of an M42 tool?
The lifespan varies based on usage, but M42 tools generally last longer than other HSS tools due to their wear resistance and heat tolerance.
Conclusion
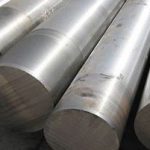
M42 tool steel remains an indispensable material in high-speed cutting and tooling applications. With its unique composition, remarkable hardness, and heat resistance, it serves as an optimal choice for industries that require precision, durability, and efficiency. By following the correct heat treatment procedures and maintaining the tools properly, M42 tool steel can offer exceptional performance and a longer operational lifespan. Whether you’re looking to improve productivity or reduce downtime, investing in M42 tool steel tools is a smart choice for modern manufacturing needs.