Introduction
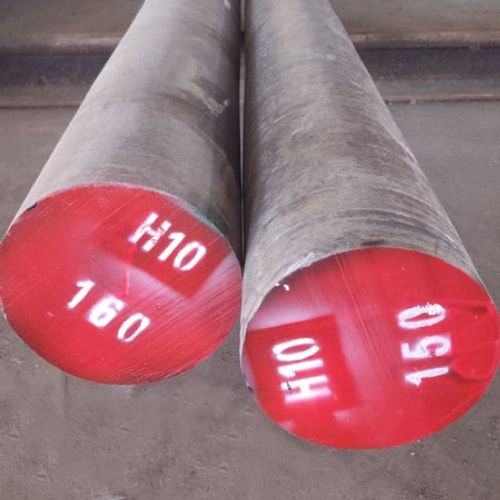
Alloy tool steel is a class of steel specifically engineered for demanding applications that require exceptional hardness, wear resistance, and toughness. These steels are meticulously crafted by incorporating specific alloying elements, such as chromium, vanadium, tungsten, and molybdenum, into the steel matrix. This strategic alloying process endows the steel with a unique combination of properties that sets it apart from conventional carbon steels.
The versatility of alloy tool steel is evident in its wide range of applications across various industries. From the precision cutting tools that shape intricate components to the durable dies and molds that form complex shapes, alloy tool steel plays a crucial role in driving manufacturing processes forward.
This comprehensive guide delves into the intricacies of alloy tool steel, exploring its composition, types, properties, heat treatment, and diverse applications. By the end of this exploration, you will gain a profound understanding of why tool steel is an indispensable material in modern manufacturing.
Understanding Alloy Tool Steel
What is Alloy Tool Steel?
Alloy tool steel is a specialized type of steel that undergoes meticulous alloying to achieve a precise balance of properties. By strategically introducing specific alloying elements into the steel matrix, metallurgists can fine-tune the steel’s performance to meet the stringent demands of various applications.
These alloying elements, such as chromium, vanadium, tungsten, and molybdenum, impart a unique set of characteristics to the steel. Chromium, for instance, enhances the steel’s hardness, wear resistance, and corrosion resistance. Vanadium refines the grain structure, leading to improved toughness and wear resistance. Tungsten, a potent alloying element, significantly boosts the steel’s hardness, wear resistance, and red hardness, enabling it to retain its hardness at elevated temperatures. Molybdenum, on the other hand, contributes to enhanced toughness, wear resistance, and hardenability.
Composition and Properties
The specific composition of tool steel varies depending on the intended application. However, certain alloying elements are commonly employed to impart specific properties.
- Chromium: A versatile alloying element, chromium enhances the steel’s hardness, wear resistance, and corrosion resistance. By forming hard chromium carbides, it significantly improves the steel’s ability to withstand abrasive wear and resist corrosion, making it ideal for applications in harsh environments.
- Vanadium: Vanadium plays a crucial role in refining the steel’s microstructure. It promotes the formation of fine-grained structures, which contribute to enhanced toughness and wear resistance. Additionally, vanadium carbides, which are extremely hard, further improve the steel’s wear resistance.
- Tungsten: Tungsten is renowned for its ability to impart exceptional hardness, wear resistance, and red hardness to steel. By forming tungsten carbides, it significantly increases the steel’s resistance to deformation and wear, even at elevated temperatures. This makes tungsten-alloyed steels particularly suitable for high-speed cutting tools and hot work tools.
- Molybdenum: Molybdenum is a valuable alloying element that enhances the steel’s toughness, wear resistance, and hardenability. It forms molybdenum carbides, which contribute to improved wear resistance and strength. Additionally, molybdenum aids in the formation of a fine-grained microstructure, further enhancing the steel’s toughness.
Alloy Tool Steel Type | Primary Alloying Elements | Hardness | Wear Resistance | Toughness | Applications |
---|---|---|---|---|---|
High-speed steel | Tungsten, chromium, vanadium | Very high | Very high | Moderate | Cutting tools, drills, reamers, milling cutters |
Cold work tool steel | Chromium, vanadium, tungsten | Very high | High | Low | Cold forming tools, punches, dies, shear blades |
Hot work tool steel | Chromium, molybdenum, tungsten | High | High | Moderate | Hot forming tools, forging dies, extrusion dies |
Shock-resistant tool steel | Chromium, nickel, molybdenum | High | Moderate | High | Chisels, punches, hammers, other impact tools |
Heat Treatment
Heat treatment is a critical process that involves subjecting alloy tool steel to precise temperature cycles to achieve the desired microstructure and properties. This process involves a series of steps, including heating, cooling, and sometimes reheating, to manipulate the steel’s crystalline structure.
- Quenching: Involves rapidly cooling the steel from a high temperature to induce a hard, martensitic microstructure. This process significantly enhances the steel’s hardness and wear resistance.
- Tempering: A subsequent heat treatment process that involves reheating the quenched steel to a lower temperature. This process relieves internal stresses and reduces brittleness, resulting in a more balanced combination of hardness and toughness.
- Carburizing: A heat treatment process that involves exposing the steel to a carbon-rich environment at elevated temperatures. This process allows carbon atoms to diffuse into the steel’s surface, creating a hard, wear-resistant layer.
Applications of Alloy Tool Steel
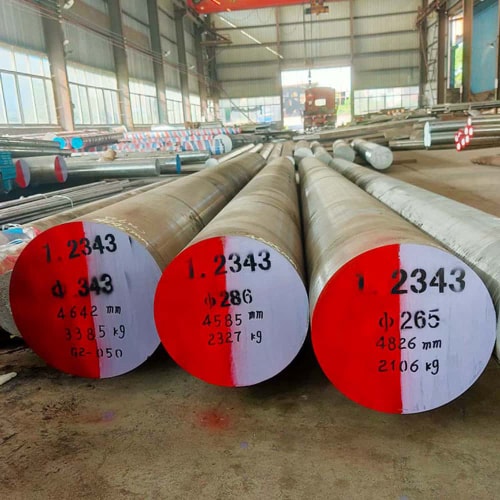
Alloy tool steel, with its exceptional properties, finds extensive use in a wide range of industries.
- Metalworking: Alloy tool steel is the backbone of the metalworking industry, powering a variety of cutting, forming, and shaping processes. High-speed steel (HSS) tools, renowned for their ability to maintain cutting edges at high speeds, are widely used in machining operations. Cold work tool steels, characterized by their exceptional hardness and wear resistance, are employed in cold forming processes such as stamping, drawing, and bending. Hot work tool steels, with their ability to withstand high temperatures and pressures, are indispensable in hot forming processes like forging and extrusion.
- Automotive: The automotive industry relies heavily on alloy tool steel for the production of critical components. From engine valves and cylinder heads to transmission gears and suspension components, alloy tool steel ensures the durability and reliability of these components. Additionally, alloy tool steel is used extensively in the manufacturing of automotive tools and dies, enabling the precise shaping of complex components.
- Aerospace: The aerospace industry demands materials that can withstand extreme conditions, and alloy tool steel excels in meeting these stringent requirements. High-speed steel cutting tools are used to machine intricate aerospace components, while hot work tool steels are employed in the forging and extrusion of turbine blades and other critical components.
- Medical: Alloy tool steel plays a vital role in the medical industry, particularly in the manufacturing of surgical instruments. Its exceptional hardness, wear resistance, and corrosion resistance ensure the precision and durability of these instruments, enabling delicate surgical procedures. Additionally, alloy tool steel is used in the production of medical implants and prosthetics, providing reliable and long-lasting solutions for patients.
Conclusion
Alloy tool steel, a testament to human ingenuity and metallurgical expertise, is a versatile and indispensable material in modern manufacturing. Its unique combination of properties, coupled with advanced heat treatment techniques, makes it the ideal choice for a diverse range of applications. By understanding the composition, properties, and applications of alloy tool steel, engineers and manufacturers can select the most suitable material to meet their specific needs, ensuring optimal performance and efficiency.
FAQ
What is the difference between alloy tool steel and carbon steel?
Alloy tool steel is superior to carbon steel due to its enhanced hardness, wear resistance, and toughness, achieved through the addition of specific alloying elements.
How is alloy tool steel made?
Alloy tool steel is produced through a complex process involving melting, alloying, casting, forging, and heat treatment to achieve the desired properties.
What are the common problems associated with alloy tool steel?
Common problems include improper heat treatment, excessive wear, and thermal fatigue.
How can I select the right alloy tool steel for my application?
Consider factors such as required hardness, wear resistance, toughness, and operating conditions when selecting the appropriate alloy tool steel.