Introduction
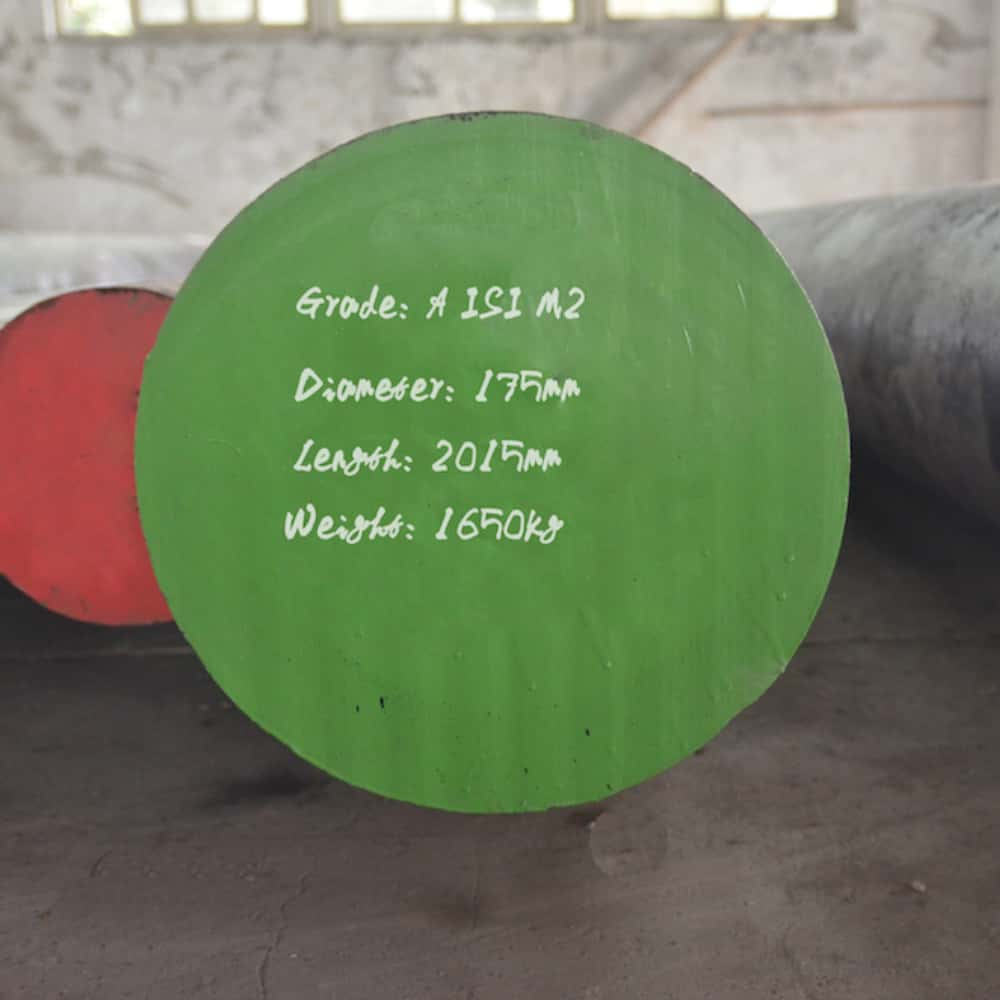
M2 tool steel, a high-speed steel alloy, has long been a cornerstone in the manufacturing industry. Renowned for its exceptional hardness, wear resistance, and toughness, M2 steel finds applications in a diverse range of industries. Its ability to withstand extreme conditions and maintain cutting edge performance has made it a preferred choice for engineers and manufacturers worldwide. This article delves into the intricacies of M2 tool steel, exploring its properties, applications, and best practices for optimal utilization.
Understanding M2 Tool Steel: A Closer Look
M2 tool steel is a molybdenum-based high-speed steel alloy, meticulously engineered to deliver outstanding performance. Its composition, carefully balanced with tungsten, chromium, vanadium, and carbon, contributes to its unique properties. The high carbon content imparts exceptional hardness, while the alloying elements enhance toughness, wear resistance, and red hardness. This synergistic combination of properties makes M2 steel a versatile and reliable material for demanding applications.
Key Properties of M2 Tool Steel: A Deep Dive
- Hardness: M2 tool steel can achieve extraordinary levels of hardness, making it highly resistant to wear and abrasion. This property is crucial in applications where tools are subjected to continuous contact with the workpiece, such as drilling, milling, and turning.
- Toughness: Despite its exceptional hardness, M2 steel retains excellent toughness, minimizing the risk of chipping or breaking. This balance of hardness and toughness is essential for maintaining tool integrity and preventing premature failure.
- Red Hardness: M2 steel exhibits remarkable red hardness, enabling it to maintain its cutting edge performance at elevated temperatures. This property is particularly beneficial in high-speed machining operations where heat generation can significantly impact tool life.
- Wear Resistance: The combination of hardness and toughness in M2 steel results in exceptional wear resistance. This property is critical in applications where tools are subjected to prolonged contact with abrasive materials, ensuring long tool life and consistent performance.
Applications of M2 Tool Steel: A Wide Range of Possibilities
M2 tool steel is a versatile material with a wide range of applications across various industries:
- Cutting Tools: M2 steel is widely used in the manufacturing of cutting tools, including drills, mills, reamers, and taps. Its exceptional hardness, toughness, and wear resistance make it ideal for machining a variety of materials, from soft metals to hard alloys.
- Molds and Dies: M2 steel is employed in the creation of molds and dies for forming and shaping metals and plastics. Its ability to withstand high pressures and temperatures, coupled with its excellent dimensional stability, ensures the production of high-quality components.
- Punches and Shears: M2 steel is well-suited for punching and shearing operations due to its high wear resistance and impact toughness. Its ability to withstand repeated stress cycles and maintain sharp edges makes it a reliable choice for these demanding applications.
- Other Applications: M2 steel finds applications in various other industries, including the aerospace, automotive, and medical sectors. Its exceptional properties make it suitable for components that require high strength, durability, and precision, such as surgical instruments, engine components, and aerospace hardware.
Factors Affecting the Performance of M2 Tool Steel: A Comprehensive Analysis
Several factors can influence the performance of M2 tool steel, including:
- Heat Treatment: The heat treatment process plays a crucial role in determining the final properties of M2 steel. Proper heat treatment is essential to achieve the desired hardness, toughness, and wear resistance.
- Cutting Conditions: Cutting parameters such as speed, feed rate, and depth of cut significantly impact tool wear and performance. Optimizing these parameters is essential to maximize tool life and productivity.
- Coolant: The use of a suitable coolant can help to reduce tool temperature, improve lubrication, and enhance chip evacuation. Proper coolant selection and application are crucial for maintaining tool performance.
Comparison of M2 Tool Steel with Other Alloys: A Detailed Analysis
Alloy | Composition | Hardness | Toughness | Wear Resistance | Typical Applications |
---|---|---|---|---|---|
M2 | Mo-W-Cr-V-C | High | Good | Excellent | Cutting tools, molds, dies, punches, shears |
M3 | Mo-W-Cr-V-C | High | Good | Excellent | High-speed machining, aerospace components |
T1 | W-Mo-Cr-V-C | High | Good | Excellent | High-speed machining, cutting tools |
H13 | Cr-Mo-V | High | Good | Good | Hot work tools, plastic molds, dies |
Best Practices for Using M2 Tool Steel: Maximizing Performance

To maximize the performance of M2 tool steel, consider the following best practices:
- Proper Heat Treatment: Ensure that M2 steel is heat-treated according to the manufacturer’s recommendations to achieve optimal properties.
- Select the Right Cutting Tool Geometry: Choose a cutting tool geometry that is appropriate for the material being machined and the desired cutting conditions.
- Optimize Cutting Conditions: Experiment with different cutting speeds, feed rates, and depths of cut to find the optimal settings for the specific application.
- Use a Suitable Coolant: Select a coolant that is compatible with the material being machined and the cutting conditions. Proper coolant application can significantly improve tool life and surface finish.
Conclusion
M2 tool steel is a high-performance alloy that offers exceptional hardness, toughness, wear resistance, and red hardness. Its versatility and reliability make it a valuable asset in various industries. By understanding its properties, applications, and best practices, engineers and manufacturers can effectively utilize M2 steel to improve productivity, reduce costs, and enhance product quality.
FAQ
What is the difference between M2 and M3 tool steel?
M2 and M3 tool steels are similar, but M3 has higher vanadium content, leading to improved toughness and wear resistance.
How is M2 tool steel heat treated?
M2 tool steel is typically heat treated through a process involving austenitizing, quenching, and tempering.
Can M2 tool steel be welded?
While M2 tool steel can be welded, it requires specialized welding techniques and post-welding heat treatment to maintain its properties.
What are some common applications for M2 tool steel?
M2 tool steel is commonly used in cutting tools, molds and dies, punches and shears, and various other industrial applications.