Introduction
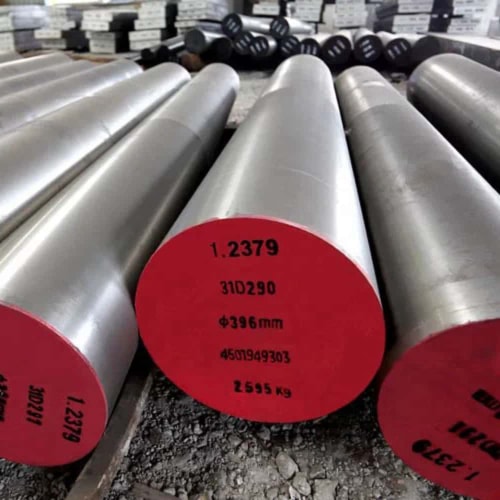
Welding tool steel is an indispensable material in a myriad of industrial applications, from the construction of towering skyscrapers to the precision manufacturing of intricate components. Its exceptional durability, characterized by its resistance to wear, heat, and mechanical stress, is the cornerstone of its widespread use in welding operations. This comprehensive exploration delves into the intricacies of tool steel, examining its composition, properties, applications, and the factors that contribute to its remarkable durability.
Understanding Welding Tool Steel
Welding tool steel is a specialized alloy steel meticulously engineered to withstand the rigorous conditions encountered during welding processes. These steels are fortified with a carefully balanced blend of alloying elements, each contributing unique properties that enhance the overall performance of the material. Key alloying elements commonly found in tool steel include:
- Chromium: This element significantly improves the steel’s hardness and resistance to corrosion, making it more durable in harsh environments.
- Tungsten: Known for its ability to enhance red hardness and wear resistance, tungsten is crucial for maintaining the steel’s performance at elevated temperatures.
- Vanadium: This element refines the grain structure of the steel, leading to increased toughness and improved mechanical properties.
- Molybdenum: Molybdenum contributes to the steel’s strength and toughness, particularly at elevated temperatures, making it suitable for high-stress applications.
Key Properties of Welding Tool Steel
Hardness: A paramount property of welding tool steel, hardness determines the material’s resistance to indentation and abrasion. A harder steel can withstand greater forces and maintain its shape and integrity under heavy loads. The hardness of tool steel is typically measured on the Rockwell C scale, with higher values indicating greater hardness.
Toughness: Toughness is the measure of a material’s ability to absorb energy and deform plastically before fracturing. A tough welding tool steel can withstand impact loads and sudden changes in stress without catastrophic failure. This property is crucial for applications where the steel may be subjected to shock or vibration.
Wear Resistance: Wear resistance is the ability of a material to resist the gradual loss of material due to friction and abrasion. A high degree of wear resistance is essential for welding tools that are subjected to continuous contact with other materials.
Heat Resistance: Welding tool steel must retain its mechanical properties at elevated temperatures, as welding processes generate significant heat. This heat resistance ensures that the tool can maintain its shape and function without experiencing significant degradation.
Factors Affecting the Durability of Welding Tool Steel
The durability of tool steel is influenced by a variety of factors, including:
- Alloy Composition: The specific combination and proportions of alloying elements in the steel significantly impact its properties. Different alloying elements impart distinct characteristics, such as hardness, toughness, and wear resistance.
- Heat Treatment: Heat treatment processes, such as quenching and tempering, are critical for achieving the desired mechanical properties. These processes involve heating the steel to a specific temperature, holding it for a certain time, and then cooling it at a controlled rate to modify its microstructure.
- Manufacturing Process: The manufacturing process, including casting, forging, and machining, can influence the final properties of the steel. Careful control of these processes is essential to ensure the desired level of durability.
- Operating Conditions: The operating conditions, including temperature, load, and environment, can affect the performance and longevity of welding tool steel. High temperatures, heavy loads, and corrosive environments can accelerate wear and degradation.
Applications of Welding Tool Steel
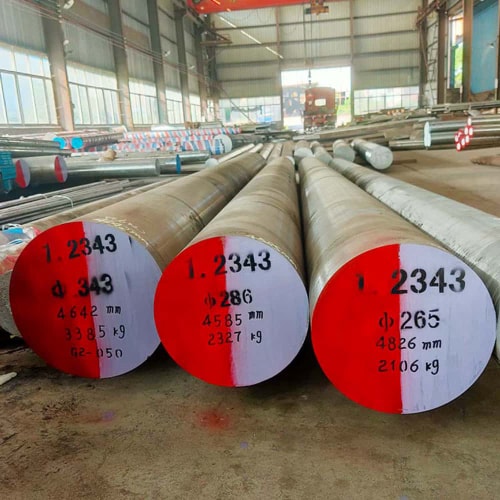
Welding tool steel finds extensive application in various industries, including:
- Automotive: The automotive industry relies on welding tool steel for the manufacturing of critical components such as engine blocks, transmission housings, and suspension parts.
- Aerospace: In the aerospace industry, tool steel is used to fabricate aircraft components, tooling, and dies.
- Construction: The construction industry utilizes tool steel for the fabrication of steel structures, bridges, and other infrastructure projects.
- Tool and Die Making: Welding tool steel is essential for the manufacturing of cutting tools, dies, and molds, which are used to shape and form various materials.
Grade | Hardness (HRC) | Toughness | Wear Resistance | Heat Resistance | Typical Applications |
---|---|---|---|---|---|
A2 | 62-64 | High | Excellent | Good | General-purpose tooling, dies, and punches |
D2 | 58-62 | High | Very good | Good | Cold work tools, plastic molds, and cutting tools |
H13 | 50-55 | Good | Excellent | Very good | Hot work tools, die casting dies, and forging dies |
M2 | 62-65 | High | Excellent | Good | High-speed cutting tools, drills, and reamers |
Conclusion
Welding tool steel is a testament to the ingenuity of metallurgical engineering, offering exceptional durability and performance in demanding applications. By understanding the factors that contribute to its durability and selecting the appropriate grade for specific needs, engineers and manufacturers can optimize their processes and achieve superior results. As technology continues to evolve, we can anticipate further advancements in welding tool steel, pushing the boundaries of what is possible in various industries.
FAQ
Q: What is the difference between welding tool steel and stainless steel?
A: Welding tool steel is primarily designed for strength and durability, while stainless steel is known for its corrosion resistance.
Q: How is tool steel hardened?
A: Heat treatment processes, such as quenching and tempering, are used to harden tool steel.
Q: What are the common heat treatments for welding tool steel?
A: Common heat treatments include quenching, tempering, annealing, and normalizing.
Q: How can I select the right grade of welding tool steel for my application?
A: Consider factors like hardness, toughness, wear resistance, and heat resistance, as well as the specific requirements of your application.
Q: What are the common challenges associated with welding tool steel?
A: Common challenges include tool wear, heat cracking, and difficulty in machining.