Welcome to My Blog!
Before we dive into the content, I’d love for you to join me on my social media platforms where I share more insights, engage with the community, and post updates. Here’s how you can connect with me:
Facebook:https://www.facebook.com/profile.php?id=100087990137347
LinkedIn:https://www.linkedin.com/company/89825762/admin/dashboard/
YouTube:www.youtube.com/@carbonsteelsupply-kj9lw
TikTok:www.tiktok.com/@carbonsteelsupply
Now, let’s get started on our journey together. I hope you find the content here insightful, engaging, and valuable.
Introduction
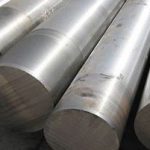
M2 high speed steel is renowned for its superior properties and versatility in machining applications. As a high-performance tool steel, M2 offers excellent wear resistance, toughness, and heat resistance, making it a preferred choice for various industrial applications. This blog will delve into the benefits of using M2 high speed steel in machining, supported by relevant data and analysis.
Understanding M2 High Speed Steel
M2 high speed steel is an alloy steel that contains significant amounts of tungsten and molybdenum, giving it the ability to withstand high temperatures without losing hardness. Its unique composition and heat treatment process enhance its performance, making it ideal for cutting tools, drills, and other machining applications.
Key Properties of M2 High Speed Steel
Property | Description |
---|---|
Hardness | Excellent hardness after heat treatment |
Wear Resistance | High resistance to wear, reducing tool replacement costs |
Toughness | Good toughness, minimizing breakage during operations |
Heat Resistance | Maintains hardness at elevated temperatures |
Machinability | Fair machinability, suitable for various cutting operations |
Benefits of M2 High Speed Steel in Machining
1Superior Wear Resistance
One of the most significant advantages of M2 high speed steel is its superior wear resistance. This property allows tools made from M2 to maintain their cutting edges longer, reducing the frequency of tool changes and increasing overall productivity. In high-speed machining environments, this translates to lower operational costs and improved efficiency.
Excellent Toughness
M2 high speed steel exhibits excellent toughness, which is crucial for tools subjected to impact loads. This toughness helps prevent chipping and breakage, ensuring that machining operations can proceed without interruptions. For industries that require reliability and durability in their cutting tools, M2 is an ideal choice.
High Heat Resistance
M2 retains its hardness even at elevated temperatures, making it suitable for high-speed applications where other steels might lose their effectiveness. This heat resistance ensures that tools can operate at higher speeds without degrading, enabling faster production rates and improved machining efficiency.
Versatility in Applications
M2 high speed steel is used across various industries, including automotive, aerospace, and manufacturing. Its versatility allows for the production of various cutting tools, such as drill bits, taps, and milling cutters, making it a valuable asset in any machining environment.
Cost-Effectiveness
While M2 high speed steel may have a higher initial cost compared to other materials, its longevity and reduced maintenance costs make it a cost-effective solution in the long run. The decreased frequency of tool replacement and the improved efficiency of machining operations contribute to significant savings over time.
Improved Surface Finish
Machining with M2 high speed steel often results in a better surface finish on the workpiece. The fine microstructure of M2 enables smoother cutting, which reduces the need for secondary finishing processes. This benefit is especially important in industries where surface quality is critical.
Easy Availability and Fabrication
M2 high speed steel is widely available, and its fabrication process is well understood in the industry. This availability ensures that manufacturers can easily source the material and produce the required tools without delays, streamlining production processes.
Applications of M2 High Speed Steel
M2 high speed steel is utilized in various applications, including:
- Drill Bits: Ideal for high-speed drilling applications due to its wear resistance and toughness.
- End Mills: Provides excellent performance in milling operations, maintaining sharp edges for extended periods.
- Taps: Commonly used for threading materials, M2 taps offer durability and precision.
- Reamers: Ensures smooth finishes and accurate dimensions in reaming operations.
Heat Treatment Process for M2 High Speed Steel
The heat treatment process plays a critical role in enhancing the properties of M2 high speed steel. The typical process involves:
- Austenitizing: Heating the steel to a temperature where its structure transforms into austenite.
- Quenching: Rapidly cooling the steel to lock in the austenitic structure, resulting in increased hardness.
- Tempering: Reheating the steel to reduce brittleness while retaining hardness, improving toughness.
Heat Treatment Parameters for M2 High Speed Steel
Treatment Step | Temperature (°C) | Duration (Minutes) |
---|---|---|
Austenitizing | 1200-1260 | 30-60 |
Quenching | Water or Oil | Immediate |
Tempering | 540-600 | 2-4 hours |
Conclusion
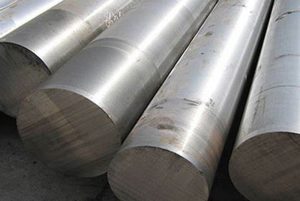
High speed steel M2 stands out as a superior choice for machining applications due to its excellent wear resistance, toughness, and heat resistance. Its versatility and cost-effectiveness make it an ideal material for a wide range of cutting tools. By leveraging the benefits of M2 high speed steel, manufacturers can enhance productivity, reduce operational costs, and achieve high-quality results in their machining processes.
FAQ
What is M2 high speed steel?
High speed steel M2 is an alloy steel that offers exceptional hardness, wear resistance, and heat resistance, making it suitable for cutting tools and machining applications.
How is M2 high speed steel treated?
M2 is typically heat-treated through a process of austenitizing, quenching, and tempering to enhance its properties.
What are the advantages of using M2 high speed steel in machining?
The primary advantages include superior wear resistance, excellent toughness, high heat resistance, versatility, cost-effectiveness, improved surface finish, and easy availability.
Where is M2 high speed steel commonly used?
M2 is widely used in the production of drill bits, end mills, taps, and reamers across various industries, including automotive and aerospace.
How does M2 compare to other tool steels?
While M2 is known for its high performance, it is important to evaluate specific requirements to choose the most suitable tool steel for particular applications.