Welcome to My Blog!
Before we dive into the content, I’d love for you to join me on my social media platforms where I share more insights, engage with the community, and post updates. Here’s how you can connect with me:
Facebook:https://www.facebook.com/profile.php?id=100087990137347
LinkedIn:https://www.linkedin.com/company/89825762/admin/dashboard/
YouTube:www.youtube.com/@carbonsteelsupply-kj9lw
TikTok:www.tiktok.com/@carbonsteelsupply
Now, let’s get started on our journey together. I hope you find the content here insightful, engaging, and valuable.
Introduction
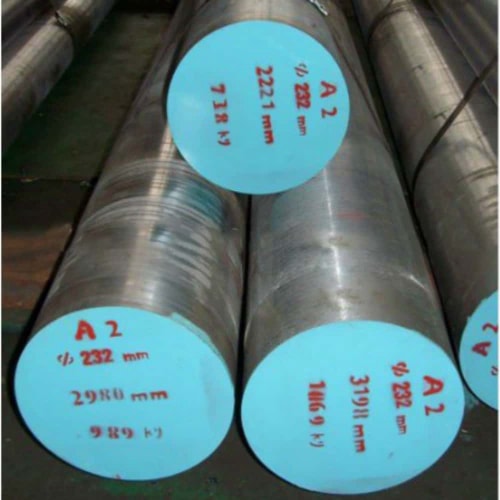
A2 tool steel is a versatile and widely used air-hardening steel known for its balance of toughness, wear resistance, and machinability. The hardness of A2 tool steel plays a critical role in determining its performance and suitability for various applications. In this comprehensive guide, we will explore how A2 tool steel hardness influences its effectiveness, benefits, and use cases. We will also cover the processes to achieve the desired hardness and provide tips on optimizing A2 tool steel hardness for specific needs.
What Is A2 Tool Steel Hardness?
A2 tool steel hardness refers to the material’s ability to resist deformation when subjected to external forces, specifically indentation, wear, and cutting stresses. The hardness is measured using the Rockwell C scale (HRC), which indicates the steel’s strength. Typically, A2 tool steel can achieve a hardness level ranging from 57 to 62 HRC, depending on the heat treatment and quenching processes used.
Achieving the correct hardness for A2 tool steel is vital to ensure optimal performance. If it is too soft, the steel may not be suitable for applications that require high wear resistance. Conversely, if it is too hard, it could become brittle, increasing the risk of fractures.
Importance of Hardness in A2 Tool Steel Performance
The hardness of A2 tool steel directly impacts its performance in several ways:
- Wear Resistance: Higher hardness levels enhance the steel’s ability to resist abrasion, making it suitable for cutting and shaping tools.
- Toughness and Durability: Maintaining the right balance between hardness and toughness is crucial. A2 tool steel with appropriate hardness can withstand high impact and stress without cracking.
- Machinability: While A2 tool steel is known for its machinability, increasing its hardness may reduce this aspect. Finding the right balance between hardness and ease of machining is essential.
- Thermal Stability: Properly treated A2 tool steel retains its hardness even at elevated temperatures, which is crucial for applications like die casting and forging.
Factors Influencing A2 Tool Steel Hardness
Several factors influence the hardness of A2 tool steel, including:
- Heat Treatment: Heating and quenching A2 tool steel in a controlled environment determines its hardness level. Heat treatment enhances the molecular structure, making it more resistant to wear and impact.
- Tempering: After quenching, tempering is performed to adjust the hardness and improve toughness. The tempering temperature and duration impact the final hardness level.
- Alloy Composition: The presence of elements like carbon, chromium, and molybdenum in A2 tool steel contributes to its hardening ability. These elements form carbides that increase wear resistance and hardness.
- Air Hardening Process: A2 tool steel hardens in the air, allowing for uniform hardness throughout the material, which is advantageous for consistent performance.
Achieving Optimal Hardness for A2 Tool Steel
To optimize A2 tool steel hardness, manufacturers and machinists must follow specific heat treatment and tempering procedures. Below is a table summarizing the recommended heat treatment process and corresponding hardness levels:
Process Step | Temperature (°F) | Duration | Hardness (HRC) Range |
---|---|---|---|
Preheating | 1200 – 1300 | 15 – 30 minutes | N/A |
Heating to Austenitizing Temperature | 1775 – 1825 | 20 – 45 minutes | N/A |
Air Cooling (Quenching) | Room Temperature | Until cooled | 57 – 62 |
Tempering (1st Cycle) | 400 – 1100 | 1 – 2 hours | Adjusts toughness and hardness |
Tempering (2nd Cycle) | Same as above | 1 – 2 hours | Final hardness level |
Interpreting the Table
- Preheating: Reduces thermal shock during the hardening process.
- Austenitizing: This stage sets up the steel’s structure for hardening by heating it to a specific temperature range.
- Air Cooling (Quenching): Unlike other tool steels that require oil or water quenching, A2 tool steel is air-hardened, leading to consistent hardness levels.
- Tempering: Multiple tempering cycles may be necessary to reach the desired balance between hardness and toughness.
Applications of A2 Tool Steel Based on Hardness
The hardness level of A2 tool steel determines its suitability for various applications:
- Cutting Tools: A2 tool steel hardened to 60-62 HRC is ideal for cutting tools that need high abrasion resistance.
- Punches and Dies: When tempered to 57-60 HRC, A2 tool steel is tough enough for stamping dies and punches, providing durability and extended service life.
- Mold Components: For molds that require high impact resistance, A2 tool steel with moderate hardness levels (around 57-59 HRC) offers the right balance of toughness and wear resistance.
- Shear Blades and Chisels: A hardness range of 60-62 HRC is perfect for shear blades and chisels that demand both sharpness and durability.
Common Challenges in Achieving the Desired A2 Tool Steel Hardness
While A2 tool steel is versatile, achieving the perfect hardness requires careful attention to several challenges:
- Heat Treatment Precision: Variations in temperature and timing during heat treatment can lead to inconsistent hardness levels. This issue can affect performance, leading to premature wear or fractures.
- Tempering Adjustment: If tempering is not done correctly, the steel may either remain too brittle or become too soft. Both scenarios can compromise its effectiveness.
- Workpiece Size and Thickness: Larger pieces of A2 tool steel may cool at different rates, causing variations in hardness across the material. Controlling these variables is crucial for achieving uniform hardness.
Testing and Verifying A2 Tool Steel Hardness
Ensuring that A2 tool steel meets the desired hardness levels requires testing methods like:
- Rockwell Hardness Test: This is the most common method to measure the hardness of A2 tool steel. The Rockwell C scale (HRC) is used for accuracy and consistency.
- Microhardness Testing: For smaller components, microhardness testing provides precise measurements, ensuring that the entire piece has uniform hardness.
- Non-Destructive Testing (NDT): NDT methods, such as ultrasonic testing, can verify the integrity and hardness of the steel without causing damage, which is essential for ensuring quality in critical applications.
FAQ: Frequently Asked Questions About A2 Tool Steel Hardness
1. What is the typical hardness range for A2 tool steel?
The typical hardness range for A2 tool steel, after proper heat treatment, is between 57 and 62 HRC.
2. How does tempering affect the hardness of A2 tool steel?
Tempering adjusts the hardness by relieving internal stresses, which increases toughness while maintaining the desired hardness level.
3. Can A2 tool steel hardness be increased without compromising toughness?
Yes, careful tempering and controlled cooling during the heat treatment process can increase hardness while maintaining toughness.
4. How is A2 tool steel hardness measured?
It is measured using the Rockwell C scale (HRC) through indentation testing, which provides an accurate measure of its resistance to deformation.
5. Is A2 tool steel suitable for applications requiring extreme hardness?
While A2 tool steel is tough and can reach high hardness levels, it may not be suitable for extreme conditions where higher hardness tool steels like D2 are required.
Conclusion
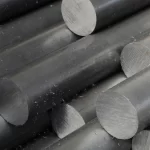
A2 tool steel hardness significantly affects its performance in various applications. Achieving the correct hardness involves precise heat treatment and tempering processes that influence the steel’s wear resistance, toughness, and machinability. Understanding the relationship between hardness and performance allows machinists and manufacturers to optimize A2 tool steel for specific uses, ensuring the longevity and efficiency of tools and components.
By following proper procedures and testing methods, A2 tool steel can be tailored to meet exact requirements, providing a reliable material for industrial applications that demand strength and durability.