Welcome to My Blog! 🌟
Before we dive into the content, I’d love for you to join me on my social media platforms. It’s where I share more insights, engage with our vibrant community, and post regular updates. Here’s how you can stay connected:
📘 Facebook: Connect with me on Facebook
Now, let’s embark on this journey together. I hope you find the content here insightful, engaging, and most importantly, valuable. Let’s explore, learn, and grow together! 🚀
Table of Contents
Introduction
P20 tool steel is a versatile and widely used material in the manufacturing and tooling industries. Known for its balanced combination of strength, toughness, and machinability, it is primarily used in the production of plastic injection molds, die casting dies, and various tools. This pre-hardened tool steel is an alloy that contains chromium, molybdenum, and nickel, which enhance its mechanical properties and contribute to its wide usage across sectors.
P20 tool steel is typically delivered in a hardened and tempered condition, making it ready for immediate use without the need for additional heat treatment. Its relatively low carbon content also makes it easier to machine and polish, further adding to its appeal in high-precision applications. In this article, we will explore nine proven advantages of P20 tool steel and examine why it remains a go-to choice for many engineers and toolmakers.
Exceptional Machinability
One of the most noteworthy characteristics of this versatile mold steel is its outstanding machinability. Compared with many other grades within the tool steel category, it offers a significantly smoother cutting experience. This results in less wear and tear on cutting tools and equipment, enabling manufacturers to maintain high levels of precision throughout extended production runs.
Thanks to its consistent microstructure, the risk of tool breakage, edge chipping, or surface tearing during machining is greatly reduced. This not only prolongs the service life of cutting instruments but also minimizes downtime and lowers maintenance costs—factors that are especially critical in competitive, high-volume production environments. The improved cutting efficiency contributes directly to shorter production cycles and enhanced throughput, making it a preferred choice for both prototyping and full-scale mold production.
Superior Surface Finish and Polishing Capabilities
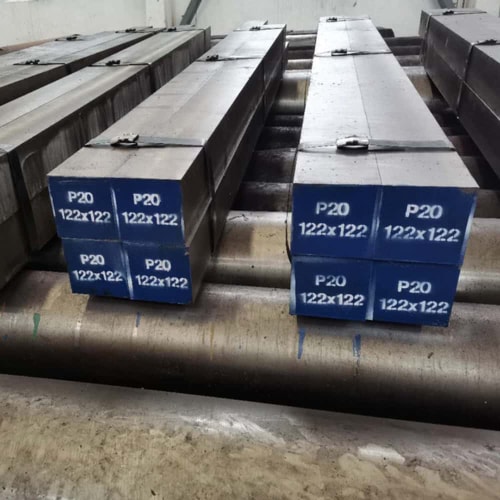
Another major advantage of this mold-grade alloy is its ability to achieve a high-quality surface finish. It excels in applications requiring a mirror-like polish, such as plastic injection molding, where surface smoothness of the mold directly influences the visual and functional quality of finished components.
Thanks to its refined grain structure, the material supports even polishing across complex geometries and fine contours. This uniformity reduces the time spent on post-processing while ensuring consistent optical clarity and minimal surface imperfections in molded products. These attributes are especially valued in industries where aesthetics and precision go hand-in-hand—such as consumer electronics, automotive interiors, and medical device casings.
High Toughness and Mechanical Reliability
Durability is a hallmark of this alloyed steel. Known for its exceptional toughness, it resists cracking, deformation, and fatigue even under repeated mechanical stress or during extended service life. Unlike more brittle alternatives, it offers a well-balanced combination of strength and ductility, making it suitable for tooling that must endure cyclical loading or impact.
Such mechanical reliability ensures that molds retain their shape and integrity over long production runs, which helps maintain part consistency and minimizes the need for frequent retooling. The result is a measurable reduction in operational disruptions and long-term tooling expenditures—two critical concerns for manufacturers striving to optimize their ROI on capital equipment.
Uniform Hardness and Pre-Hardened Structure
One of the most practical benefits of this mold steel grade lies in its pre-hardened condition. Typically supplied with a uniform hardness range of 28 to 32 HRC, it eliminates the need for further heat treatment before use. This pre-treatment ensures consistent performance across the entire block, reducing variables during both machining and final operation.
Such even hardness is particularly advantageous when fabricating complex molds where different zones may encounter varying levels of mechanical stress. Engineers can confidently design and deploy tooling components knowing that hardness—and therefore wear resistance—remains stable throughout the structure, minimizing the risk of premature failure in localized regions.
Enhanced Weldability
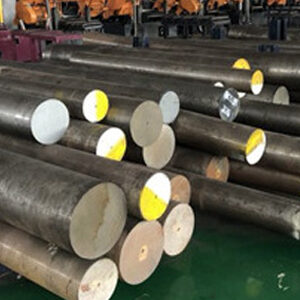
Weldability is often a crucial consideration in tool steel selection, especially for repair and modification purposes. P20 tool steel exhibits good weldability due to its relatively low carbon content and stable alloy composition. This means that repairs or adjustments to molds can be made without compromising the material’s integrity or introducing significant heat-affected zones.
The ability to weld P20 tool steel effectively without requiring pre- or post-weld heat treatment streamlines maintenance procedures and extends the lifespan of valuable tooling.
Comparison Table: P20 Tool Steel vs. Other Common Tool Steels
Property | P20 Tool Steel | H13 Tool Steel | A2 Tool Steel | D2 Tool Steel |
---|---|---|---|---|
Machinability | Excellent | Good | Moderate | Poor |
Surface Finish | High Polish | Moderate | Good | Moderate |
Pre-Hardened | Yes (28-32 HRC) | No | No | No |
Toughness | High | Very High | Moderate | Low |
Weldability | Good | Moderate | Poor | Poor |
Heat Treatment Needed | No | Yes | Yes | Yes |
Common Applications | Molds, Dies | Die Casting | Punches | Shear Blades |
This table highlights the comparative advantages of P20 tool steel over other commonly used tool steels in various industrial applications. Its combination of ease of use, durability, and versatility sets it apart as a highly desirable material.
Cost-Effective Tooling Option
P20 tool steel is often more cost-effective than other tool steels when considering the full tooling lifecycle. Its pre-hardened condition reduces processing steps and associated labor costs. Additionally, its machinability and reduced need for post-processing translate into lower production costs and faster turnaround times.
When evaluating total ownership costs—including maintenance, repair, and downtime—P20 stands out as an economical option. This makes it particularly appealing for companies aiming to optimize both performance and budget.
Versatility in Applications
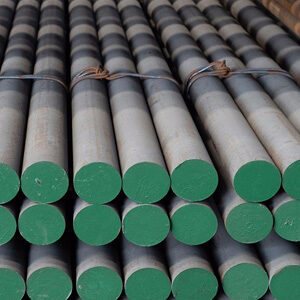
The versatility of P20 tool steel is another key advantage. It is widely used across multiple industries, including automotive, aerospace, consumer electronics, and packaging. Its balanced properties make it suitable for producing a wide range of tools and components, including molds for injection molding, die casting dies, and machine parts.
Whether used in mass production or prototyping, P20 provides reliable performance and adaptability, allowing manufacturers to meet various project requirements without switching materials.
Stable Mechanical Properties
P20 tool steel maintains its mechanical properties under a range of working conditions. This stability is crucial for applications involving repetitive cycles or varying thermal conditions. Unlike some other steels that may suffer from distortion or loss of hardness at elevated temperatures, P20 remains structurally sound, contributing to consistent product quality.
This thermal and mechanical stability is particularly beneficial for industries requiring precision and consistency, such as electronics and automotive component manufacturing.
Conclusion
In summary, P20 tool steel offers a unique combination of properties that make it a smart choice for many tooling applications. From its excellent machinability and polishability to its uniform hardness and versatility, this material supports high-quality production while reducing costs and increasing efficiency.
Its pre-hardened condition, good weldability, and long-lasting durability make it an industry favorite for mold making and tool manufacturing. Companies seeking reliable, cost-effective, and adaptable tool steel solutions will find P20 to be a dependable option.
FAQ
What is the typical hardness of P20 tool steel?
P20 tool steel usually comes pre-hardened to a level between 28 and 32 HRC, which makes it suitable for immediate use in tooling applications.
Can P20 tool steel be welded?
Yes, P20 has good weldability due to its chemical composition. It can be repaired or modified without extensive heat treatment.
What industries commonly use P20 tool steel?
Industries such as automotive, electronics, packaging, and aerospace use P20 tool steel for molds, dies, and various tool components.
Does P20 tool steel require heat treatment?
No, one of the benefits of P20 tool steel is that it is delivered in a pre-hardened state, eliminating the need for additional heat treatment.
How does P20 compare to H13 tool steel?
P20 offers better machinability and polishability, while H13 provides higher heat resistance and toughness, making each suitable for different applications.
Is P20 tool steel good for high-volume production?
Yes, its excellent machinability, polishability, and durability make P20 a reliable choice for high-volume and precision production settings.
Can P20 tool steel be used in die casting?
Yes, P20 is suitable for some die-casting applications, though H13 is often preferred for higher thermal loads.
What is the composition of P20 tool steel?
P20 generally contains carbon, chromium, molybdenum, and nickel, which contribute to its strength, toughness, and machinability.
Is P20 tool steel environmentally friendly?
While not specifically marketed as eco-friendly, its long lifespan and low maintenance contribute to sustainable manufacturing practices.