Welcome to My Blog!
Before we dive into the content, I’d love for you to join me on my social media platforms where I share more insights, engage with the community, and post updates. Here’s how you can connect with me:
Facebook:https://www.facebook.com/profile.php?id=100090797846538
Now, let’s get started on our journey together. I hope you find the content here insightful, engaging, and valuable.
Table of Contents
Introduction
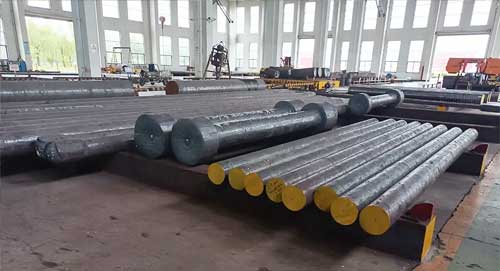
In the evolving world of manufacturing, efficiency and precision are at the forefront of innovation. One method revolutionizing this landscape is laser welding tool steel. This technology combines accuracy with durability, offering unmatched benefits for manufacturers. This blog will delve into the key advantages of laser welding tool steel, helping you understand why it is becoming a staple in industrial applications.
What Makes Laser Welding Tool Steel Unique?
Laser welding stands out for its ability to provide high-precision joints without compromising the integrity of the material. Tool steel, known for its toughness and wear resistance, pairs seamlessly with laser welding technology, resulting in superior performance in demanding environments. Here’s what makes it unique:
- Minimal heat distortion preserves material properties.
- High-speed processing enhances productivity.
- Compatibility with complex geometries ensures versatile applications.
Key Advantages of Laser Welding Tool Steel
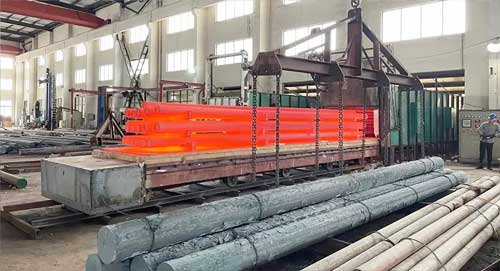
Exceptional Precision and Accuracy
Laser welding uses a focused laser beam, enabling manufacturers to achieve minute details with unmatched accuracy. This precision minimizes the need for post-weld machining, saving both time and resources. For intricate tool steel components, such as molds or dies, laser welding is a game-changer.
Reduced Heat-Affected Zone
Traditional welding methods often cause significant heat distortion, which can weaken tool steel. With laser welding, the heat-affected zone (HAZ) is minimal, preserving the structural integrity of the material. This ensures longer-lasting components and fewer production failures.
Enhanced Joint Strength
The concentrated heat input of laser welding creates strong, durable welds in tool steel. These joints are capable of withstanding high stress and wear, making them ideal for heavy-duty applications in industries such as automotive and aerospace.
Versatility in Applications
Laser welding tool steel is suitable for various applications, including repair, joining, and precision assembly. Its ability to work on complex shapes and hard-to-reach areas makes it a versatile solution for modern manufacturing challenges.
Comparison of Laser Welding and Traditional Welding Methods
Feature | Laser Welding | Traditional Welding |
---|---|---|
Heat-Affected Zone | Minimal | Significant |
Precision | High | Moderate |
Speed | Fast | Moderate |
Material Distortion | Minimal | Higher |
Post-Weld Machining | Often unnecessary | Frequently required |
Applicability to Tool Steel | Excellent | Moderate |
Cost-Effectiveness in the Long Term
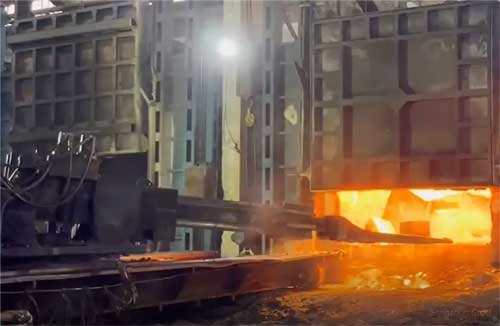
Although the initial setup for laser welding can be higher, the long-term savings outweigh the investment. The reduced need for repairs, post-weld processing, and material waste results in significant cost efficiency over time.
Environmentally Friendly Process
Laser welding tool steel generates less waste and consumes less energy compared to traditional welding methods. This makes it a sustainable choice for manufacturers looking to reduce their environmental footprint.
Faster Production Times
The speed of laser welding is unparalleled. With fewer defects and minimal need for rework, manufacturers can meet tight deadlines and increase overall productivity.
Conclusion
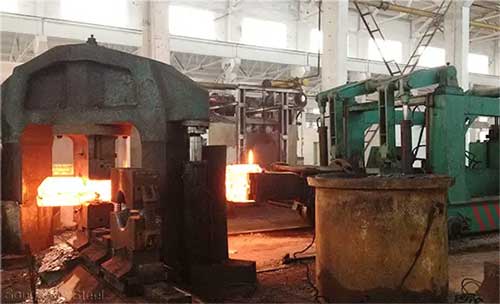
Laser welding tool steel is transforming the manufacturing industry with its precision, durability, and efficiency. Its ability to reduce costs, minimize waste, and deliver superior results makes it a valuable asset for modern manufacturers. Whether you’re dealing with intricate molds or heavy-duty components, investing in laser welding technology for tool steel ensures quality and reliability.
FAQ
What types of tool steel are suitable for laser welding?
Most grades of tool steel, including H13, D2, and P20, are compatible with laser welding. The key is to select the appropriate welding parameters for each grade.
Is laser welding better than traditional welding for tool steel?
Yes, laser welding offers better precision, reduced heat distortion, and faster processing times, making it superior for many tool steel applications.
What industries benefit the most from laser welding tool steel?
Industries such as automotive, aerospace, and mold manufacturing benefit significantly due to the need for precision and durable components.