Welcome to My Blog! 🌟
Before we dive into the content, I’d love for you to join me on my social media platforms. It’s where I share more insights, engage with our vibrant community, and post regular updates. Here’s how you can stay connected:
📘 Facebook: Connect with me on Facebook
Now, let’s embark on this journey together. I hope you find the content here insightful, engaging, and most importantly, valuable. Let’s explore, learn, and grow together! 🚀
Table of Contents
Introduction
L6 tool steel is a popular material known for its versatility, toughness, and wear resistance. As an oil-hardening tool steel, it offers a unique combination of properties that make it suitable for a wide range of industrial and manufacturing uses. L6 is often chosen for applications requiring a tough, shock-resistant material with the ability to hold an edge or maintain structure under stress. Whether in tools, dies, or specialty parts, its resilience makes it a preferred choice among metallurgists and engineers.
In this article, we will explore six brilliant applications of l6 tool steel. Each use highlights the material’s strengths and offers insights into how its characteristics benefit the end product. Whether you’re new to materials engineering or looking to upgrade components in your production process, understanding how this alloy performs can be a valuable asset.
L6 Tool Steel in Industrial Knives and Blades
One of the most recognized uses of this alloy is in the manufacturing of industrial knives and cutting blades. Thanks to its exceptional toughness, it can endure repeated impact and rigorous cutting tasks without the risk of chipping or cracking. These properties make it highly suitable for shear blades, slitter knives, and a wide range of precision cutting tools employed across various industrial processes.
Its capacity to undergo hardening while still retaining a degree of flexibility offers a distinct advantage over other materials that often become brittle after heat treatment. This rare balance of resilience and rigidity guarantees consistent, long-lasting performance, especially in high-demand production lines. As a result, operators can expect less equipment downtime and reduced maintenance expenses.
This steel’s metallurgical characteristics make it a dependable choice when the durability of blades directly affects production quality and efficiency.
L6 Tool Steel for Dies and Molds
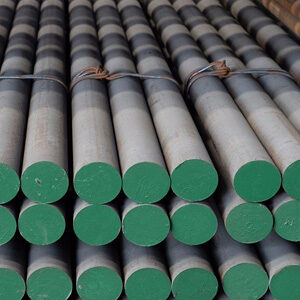
Dies and molds are exposed to high pressure and constant thermal cycling, demanding materials that can endure both mechanical and thermal stress. L6 tool steel excels in such conditions due to its outstanding toughness and resistance to cracking under load. This makes it a reliable choice for applications like plastic injection molds, forging dies, and metal stamping tools.
Its ability to achieve a smooth, high-quality polish is especially valuable in molds that require fine surface finishes and tight dimensional tolerances. This not only enhances the appearance of molded products but also improves mold release and reduces production defects.
L6’s wear resistance contributes to longer tool life, minimizing downtime and maintenance costs. Additionally, it responds well to heat treatment, allowing engineers to tailor its hardness and toughness to specific requirements. These qualities—durability, polishability, and adaptability—make L6 a top performer in modern mold and die applications.
Use of L6 Tool Steel in Automotive Components
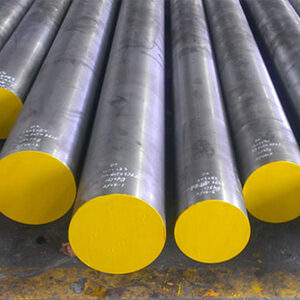
Another notable application for this high-performance steel can be found in the automotive industry, especially in parts that encounter significant mechanical stress or friction. It is commonly used in the production of crankshafts, camshafts, transmission gears, and axle components.
Its superior resistance to impact makes it a trusted material for absorbing sudden shocks and vibrations that are typical in engine and drivetrain operations. Furthermore, its mechanical strength contributes to the overall reliability and longevity of these critical components. When subjected to appropriate thermal processing, the steel’s characteristics can be precisely adjusted to meet the unique performance demands of different automotive systems.
Because of these traits, it remains a favored choice for engineers seeking materials that deliver both durability and performance in challenging vehicular environments.
Table: Key Properties of L6 Tool Steel in Different Applications
Application | Key Properties Utilized | Benefits |
---|---|---|
Industrial Knives | Toughness, Edge Retention | Durable, Chip-Resistant, Long-Lasting |
Dies and Molds | Wear Resistance, Surface Finish | Precision, High Volume Durability |
Automotive Components | Shock Resistance, Strength | Enhanced Safety, Longevity |
Custom Tools | Heat Treatability, Flexibility | Performance-Tuned Applications |
Woodworking Tools | Hardness, Edge Holding | Cleaner Cuts, Fewer Replacements |
Machining Inserts | Dimensional Stability, Toughness | Consistent Tolerances, Low Breakage |
L6 Tool Steel in Custom and Specialty Tools
In custom tooling, where off-the-shelf solutions fail to meet specific requirements, this alloy provides an ideal alternative. Whether in tool-making for niche industrial applications or in maintenance tools that endure frequent use, its combination of machinability and performance is widely valued.
Its compatibility with heat treatment methods allows developers to tailor mechanical properties like hardness, toughness, and elasticity. This adaptability ensures even highly customized components deliver consistent, reliable results over time. Industries that require fine-tuned specifications often turn to this material as their go-to option for custom-built tools.
L6 Tool Steel in Woodworking and Machining
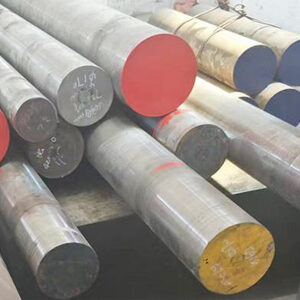
The alloy’s impact goes beyond metalworking into fields like woodworking and precision machining. In these applications, tools such as chisels, carving instruments, and lathe accessories made from this material hold their edges remarkably well while also resisting cracks and wear.
Its inherent hardness makes it ideal for fine, sharp edges required in clean, precise cuts, whereas its toughness protects against chipping during intense use. In CNC and manual machining, it’s often employed in inserts and small components that experience consistent stress or repetitive contact with hard surfaces. Its dimensional stability ensures these parts retain their accuracy and function effectively, even during long production cycles.
Whether shaping wood, metals, or composite materials, this versatile alloy continues to meet the demands of modern craftsmen and manufacturers alike.
Conclusion
The six applications outlined in this article demonstrate the exceptional capabilities of l6 tool steel. Whether you are involved in high-speed manufacturing or custom part fabrication, this material offers a balance of hardness, toughness, and machinability that few others can match.
Its wide-ranging performance in areas such as automotive, tooling, and manufacturing make it a highly adaptable and reliable material. By selecting l6 tool steel for critical components, industries can achieve greater durability, efficiency, and cost-effectiveness.
FAQ
What is the hardness of L6 tool steel?
After proper heat treatment, this alloy can reach a hardness level of approximately 60 HRC (Rockwell Hardness Scale). However, the final hardness can vary based on the exact tempering process and the specific requirements of the application. This level of hardness provides excellent wear resistance while still allowing the material to maintain a degree of toughness, making it suitable for demanding industrial and mechanical tasks. It is this dual property—hardness without brittleness—that makes it especially valued in tools requiring sharp, resilient edges.
Is L6 tool steel corrosion-resistant?
While this material performs exceptionally well in terms of toughness and wear resistance, it is not inherently corrosion-resistant. It contains relatively low chromium content compared to stainless steels, which limits its ability to resist rust and oxidation. For environments where moisture or corrosive elements are present, surface treatments such as coating, plating, or oiling are recommended. Regular maintenance is essential to extend the material’s lifespan in such conditions.
Can L6 steel be welded?
Yes, welding is possible, but it requires caution. Due to its high carbon content and alloy composition, this steel is prone to cracking if welded improperly. Pre-heating the material before welding and applying post-weld tempering are standard practices to reduce the risk of heat-affected zone failure. These measures help relieve internal stresses introduced during the welding process, ensuring structural integrity is maintained.
What makes L6 different from other tool steels?
The standout characteristic of this alloy is its superior toughness and shock resistance, which exceeds that of many other tool steels. It is specifically engineered to endure repeated impact and heavy mechanical loads without fracturing. While many tool steels offer high hardness, they often lack the resilience needed for dynamic applications. This material bridges that gap, making it ideal for tools and components that undergo both hard contact and fluctuating pressures. Its versatility across industries—from die making to automotive and woodworking—further highlights its unique profile.
Is L6 suitable for knife making?
Absolutely. Knife makers often choose this steel for crafting blades that need to hold a sharp edge and resist impact damage. It is especially favored for larger knives, such as machetes, camp knives, and some tactical or survival blades, where both durability and cutting strength are crucial. When properly heat-treated and maintained, knives made from this material can offer a long service life with minimal chipping or deformation. However, due to its limited rust resistance, additional care is necessary to prevent corrosion, especially in outdoor or high-humidity environments.