Welcome to My Blog! 🌟
Before we dive into the content, I’d love for you to join me on my social media platforms. It’s where I share more insights, engage with our vibrant community, and post regular updates. Here’s how you can stay connected:
📘 Facebook: Connect with me on Facebook
Now, let’s embark on this journey together. I hope you find the content here insightful, engaging, and most importantly, valuable. Let’s explore, learn, and grow together! 🚀
Table of Contents
Introduction
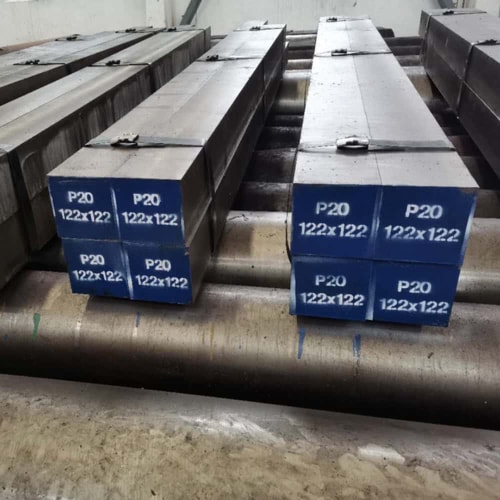
In the world of manufacturing and tooling, P20 tool steel has carved out a solid reputation for its versatility, durability, and cost-effectiveness. Known for its balanced combination of hardness, toughness, and machinability, it has become a mainstay in a wide range of mold-making and die-casting applications. Most notably, P20 tool steel is widely used in plastic injection molding, where its pre-hardened condition allows for easier machining and faster production cycles.
However, like any widely used material, P20 tool steel is surrounded by its fair share of myths and misunderstandings. These misconceptions, if left unchallenged, can lead to the wrong selection of steel grades, inadequate tooling performance, and increased operational costs. Whether you’re a tool designer, mold maker, production manager, or procurement specialist, understanding these common pitfalls can be the difference between smooth operations and costly rework.
In this article, we delve into five of the most prevalent and financially damaging misconceptions about P20 tool steel—clearing the air with facts and practical insights to help you make smarter decisions.
Misconception 1: P20 Tool Steel Is Suitable for All Mold Types
A prevalent yet costly assumption in the mold manufacturing industry is that this versatile alloy fits all molding scenarios. Its balanced combination of strength, machinability, and polishability makes it an excellent option for many standard plastic injection mold projects. However, that doesn’t make it a catch-all solution for every mold-making need.
While it performs admirably in many general-use applications, problems arise when it’s used outside its ideal range. For instance, it lacks the necessary properties to endure the extreme thermal cycling and abrasive contact associated with high-temperature or high-volume molding processes. In these demanding situations, alternative materials with enhanced wear resistance or thermal stability would offer better long-term results.
When It Works Best:
- General-purpose plastic injection molding
- Die casting operations involving low pressure
- Short-run or prototype mold designs
When to Be Cautious:
- Molding operations involving glass-filled or abrasive plastics
- Projects requiring sustained high precision at elevated temperatures
- Tools expected to endure a high number of cycles over a long period
Overlooking the performance limitations of this steel variant can lead to mold deformation, increased wear rates, and unplanned maintenance—undermining production timelines and profitability.
Misconception 2: P20 Tool Steel Does Not Require Heat Treatment
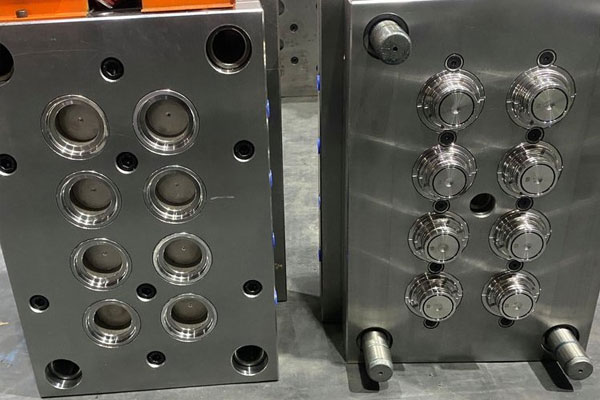
Another common misunderstanding is that this material needs no additional thermal processing due to its pre-hardened nature. Most suppliers provide it with a Rockwell hardness rating between 28 and 32 HRC, making it suitable for immediate use in many cases. However, this default state doesn’t make it universally optimal for all types of tooling.
In fact, many specialized applications—especially those involving high-volume runs or aggressive molding materials—benefit from post-supply treatment. Techniques such as nitriding, tempering, or even cryogenic processing can significantly boost resistance to surface wear and dimensional distortion. These enhancements contribute to longer mold life and improved consistency in product quality.
It’s worth noting that although further heat treatment may represent an upfront cost, the return on investment can be substantial. Reduced tool maintenance, fewer production interruptions, and prolonged performance can justify the extra steps involved.
Heat Treatment Options That May Enhance Performance:
- Nitriding – Improves surface hardness and wear resistance
- Cryogenic Treatment – Stabilizes internal structure, enhances dimensional stability
- Stress Relieving – Reduces internal stresses, improving structural integrity
By understanding the conditions where additional processing makes a difference, manufacturers can make smarter decisions that pay dividends over time.
Misconception 3: All P20 Tool Steel Grades Are the Same
This assumption can be one of the most misleading in tool selection. While “P20” is often treated as a catch-all label, various grades under this designation exhibit noticeably different performance characteristics. These differences stem from subtle adjustments in chemical composition and heat treatment history.
Here is a helpful comparison of common variants:
Grade Variant | Key Alloying Elements | Notable Features | Ideal Applications |
---|---|---|---|
Standard P20 | Carbon, Chromium | General-purpose, good machinability | Plastic molds, base plates |
P20+Ni | Nickel enhanced | Improved toughness, better polishability | Mirror finish molds, complex shapes |
P20+S | Sulfur added | Enhanced machinability | High-speed machining molds |
718 or 718H | Chromium, Nickel, Molybdenum | Superior hardness and polishability | Precision mold cavities, high-end parts |
These tailored versions are developed to meet distinct operational needs—whether it’s faster machining, improved toughness, or high-end surface finishes. Using the wrong grade can lead to compatibility issues, performance degradation, or increased material costs over time.
Before committing to a specific steel type, engineers should match the grade’s properties with the functional requirements of the application. A deeper understanding of each variant’s strengths helps optimize results and reduce post-processing work.
Misconception 4: P20 Tool Steel Is Maintenance-Free
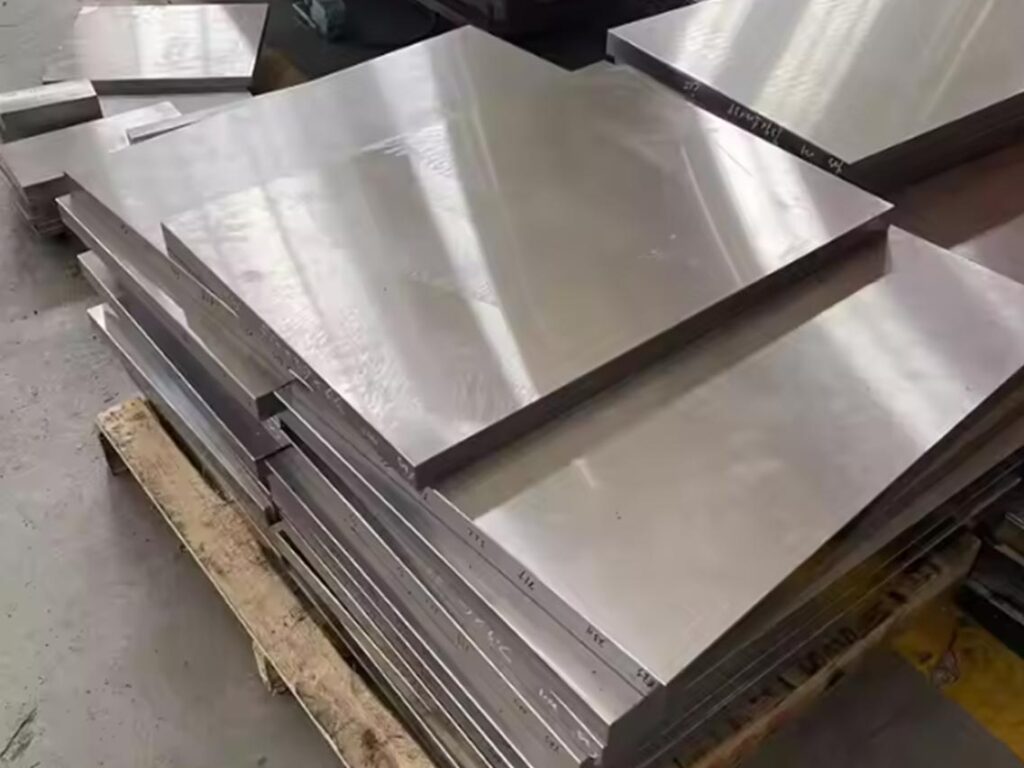
Some manufacturers mistakenly assume that once a mold is constructed with P20 tool steel, it can operate indefinitely with minimal upkeep. While its excellent machinability and toughness make it a user-friendly option during the production phase, P20 is far from immune to degradation over time.
The reality is that extended use, especially under repetitive cycles or when exposed to corrosive molding compounds, can lead to a number of detrimental issues such as oxidation, surface pitting, and micro-fractures. These issues may not be immediately obvious, but they can have a significant impact on mold performance if left unchecked. Over time, even the toughest alloys experience wear and tear, and ignoring maintenance can lead to unplanned downtime and costly repairs.
Why Maintenance Matters: The misconception of P20 being maintenance-free stems from its initial ease of use. However, this overlooks the fact that all materials, including tool steel, are subject to wear and environmental factors that degrade performance. Extended operation without proper care can result in a significant drop in quality, such as defects in molded parts or failures that require expensive repairs.
Essential Maintenance Practices Include:
- Routine Cleaning: Prevents buildup of contaminants and resins that can cause corrosion or part defects
- Proper Lubrication: Minimizes friction and mechanical wear on moving parts
- Periodic Inspections: Identifies early-stage damage, such as micro-cracks or scaling
- Surface Treatments: Polishing or recoating helps restore lost polishability and performance
Ignoring these basic steps increases the likelihood of unexpected tool failure and elevated repair costs. Building a proactive maintenance plan into your production schedule is a smart way to extend tool longevity and ensure uninterrupted operation.
Misconception 5: P20 Tool Steel Is Always the Economical Choice
At first glance, this steel type appears to be a cost-efficient choice, especially for low- to medium-volume production runs. However, this perception often overlooks the total cost of ownership (TCO).
When used in conditions it wasn’t designed for—such as high-volume, abrasive, or precision-intensive operations—the material may wear out faster or fail prematurely. This leads to frequent downtimes, expensive mold refurbishments, or complete replacements.
Factors That Influence Long-Term Cost:
- Cycle Count: Higher volume usually equals faster wear
- Tool Complexity: Intricate shapes may require tighter tolerances and polishability
- Material Compatibility: Use with filled or corrosive plastics accelerates degradation
- Maintenance Needs: The more frequent the maintenance, the higher the lifecycle cost
Conducting a TCO analysis before choosing a mold material helps in comparing not just the purchase cost but also the ongoing expenses related to tool performance, repairs, and downtime. In some cases, an initially more expensive alloy could yield better returns through longer life and lower maintenance.
By weighing both short- and long-term costs, businesses can make well-informed choices that align with project goals and budget constraints.
Conclusion
While P20 tool steel continues to be a dependable and widely used material across various industries, especially in plastic injection molding, it is not a one-size-fits-all solution. Misconceptions—whether about its universal suitability, lack of heat treatment needs, or assumptions around its cost-effectiveness—can lead to suboptimal performance and even premature tool failure. These misunderstandings not only drive up production costs but also introduce unnecessary risks to quality and operational uptime.
In modern tooling environments where competition is fierce and production downtime is costly, knowledge truly is power. Manufacturers and decision-makers who educate themselves about materials like P20 tool steel can make more informed choices—balancing cost, performance, and longevity in a way that benefits the bottom line.
FAQ
What is the typical hardness of p20 tool steel?
P20 tool steel is usually supplied in a pre-hardened state with a hardness range of 28–32 HRC.
Can p20 tool steel be welded?
Yes, it can be welded, but proper preheating and post-weld heat treatment are recommended to avoid cracking and retain structural integrity.
Is p20 tool steel corrosion-resistant?
It offers moderate corrosion resistance. However, for corrosive environments or water-cooling channels, additional surface treatment is advised.
What industries commonly use p20 tool steel?
Primarily used in plastic injection molding, die casting, and prototyping for industries like automotive, consumer goods, and packaging.
How does p20 tool steel compare to H13?
P20 is pre-hardened and easier to machine, while H13 offers higher hardness and is more suitable for high-temperature applications like die casting.