Welcome to My Blog! 🌟
Before we dive into the content, I’d love for you to join me on my social media platforms. It’s where I share more insights, engage with our vibrant community, and post regular updates. Here’s how you can stay connected:
📘 Facebook: Connect with me on Facebook
Now, let’s embark on this journey together. I hope you find the content here insightful, engaging, and most importantly, valuable. Let’s explore, learn, and grow together! 🚀
Table of Contents
Introduction
High speed steel (HSS) has earned its place as a go-to material in the manufacturing and cutting industries. Known for its durability and ability to retain hardness at high temperatures, this alloy is commonly used for making cutting tools such as drills, saw blades, taps, and end mills. When people ask what is high speed steel, they often hear about its excellent heat resistance, machinability, and overall reliability.
However, while high speed steel is favored in many applications, it’s not without its limitations. There are several drawbacks associated with this material that professionals should consider before selecting it for their projects. In this blog, we will dive into four surprising drawbacks of what is high speed steel, exploring the material’s downsides to provide a balanced view.
Whether you’re a machinist, engineer, or a hobbyist, understanding the lesser-known challenges of high speed steel will help you make informed choices for tool selection and application.
The High Cost of High Speed Steel
One of the most surprising drawbacks of what is high speed steel lies in its cost. High speed steel, often abbreviated as HSS, is considerably more expensive than other tool-making materials like carbon steel or basic alloy steel. This makes what is high speed steel a less accessible option for smaller workshops or operations with limited budgets.
The main reason behind this higher price is the inclusion of expensive alloying elements such as tungsten, chromium, vanadium, and molybdenum. These elements improve tool performance by enhancing wear resistance and heat tolerance, but they also significantly increase production costs. As a result, industries often hesitate when considering what is high speed steel for general-purpose applications.
The high initial investment in tools made from HSS can be justifiable for precision manufacturing, but not always for short runs or low-demand operations. Before adopting HSS tooling, it’s important to evaluate whether what is high speed steel truly adds enough value to offset the added expenses.
Key Points:
- More costly than carbon steel and basic tool steel
- Alloying materials drive up production expenses
- Investment in what is high speed steel may not suit small-scale users
- Not the most economical choice for non-precision machining
Limited Toughness in Specific Applications
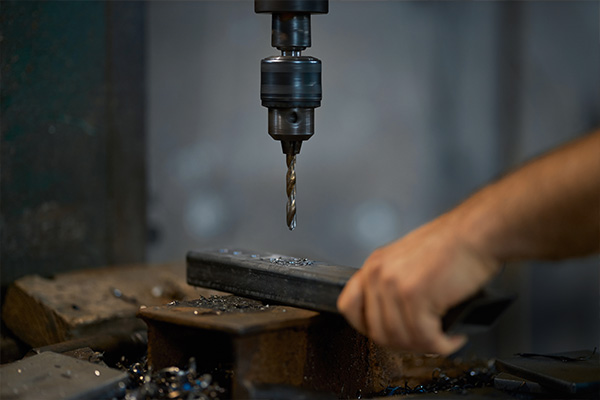
Another critical aspect to consider when asking what is high speed steel is its performance under tough and unpredictable conditions. Although HSS boasts high hardness and excellent wear resistance, it lacks superior toughness in scenarios involving sudden force or repeated impact. In high-stress environments such as interrupted cutting, heavy-duty milling, or operations with uneven surfaces, high speed steel tools can become vulnerable to fractures, cracks, or premature wear.
This relative brittleness limits the versatility of what is high speed steel in dynamic machining environments. The material’s inherent hardness, while excellent for holding a sharp edge, makes it more prone to chipping under mechanical shocks or vibrations. This is particularly concerning in industries such as automotive, aerospace, or heavy equipment repair, where operations often deal with irregular or unpredictable loads.
In comparison, materials like cemented carbide or powder metallurgy steels offer higher impact resistance and longer life under heavy-duty use. For applications that demand more flexibility or shock absorption, these alternatives are often more suitable.
Considerations:
- Susceptible to brittle failure under heavy impact
- Not ideal for rough or interrupted cutting
- May require frequent replacement in tough conditions
Heat Resistance Comes With Trade-offs
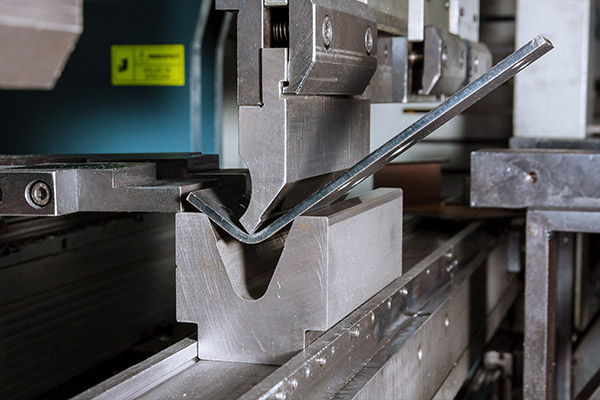
When discussing what is high speed steel, its excellent heat resistance is often highlighted. While this is a strength, it comes with some notable trade-offs. HSS can withstand high operating temperatures, but only up to a certain point—usually around 600°C (1,112°F). Beyond that, its properties begin to degrade, which limits its application in ultra-high-speed or dry cutting environments.
Additionally, heat resistance can lead to slower cooling rates, making the tool more susceptible to thermal fatigue over time. In environments where cooling is minimal or where heat dissipation is crucial, HSS may not be the best option.
Downsides:
- Performance degradation beyond 600°C
- Not suitable for extreme-speed cutting
- Risk of thermal fatigue over time
Maintenance and Regrinding Requirements
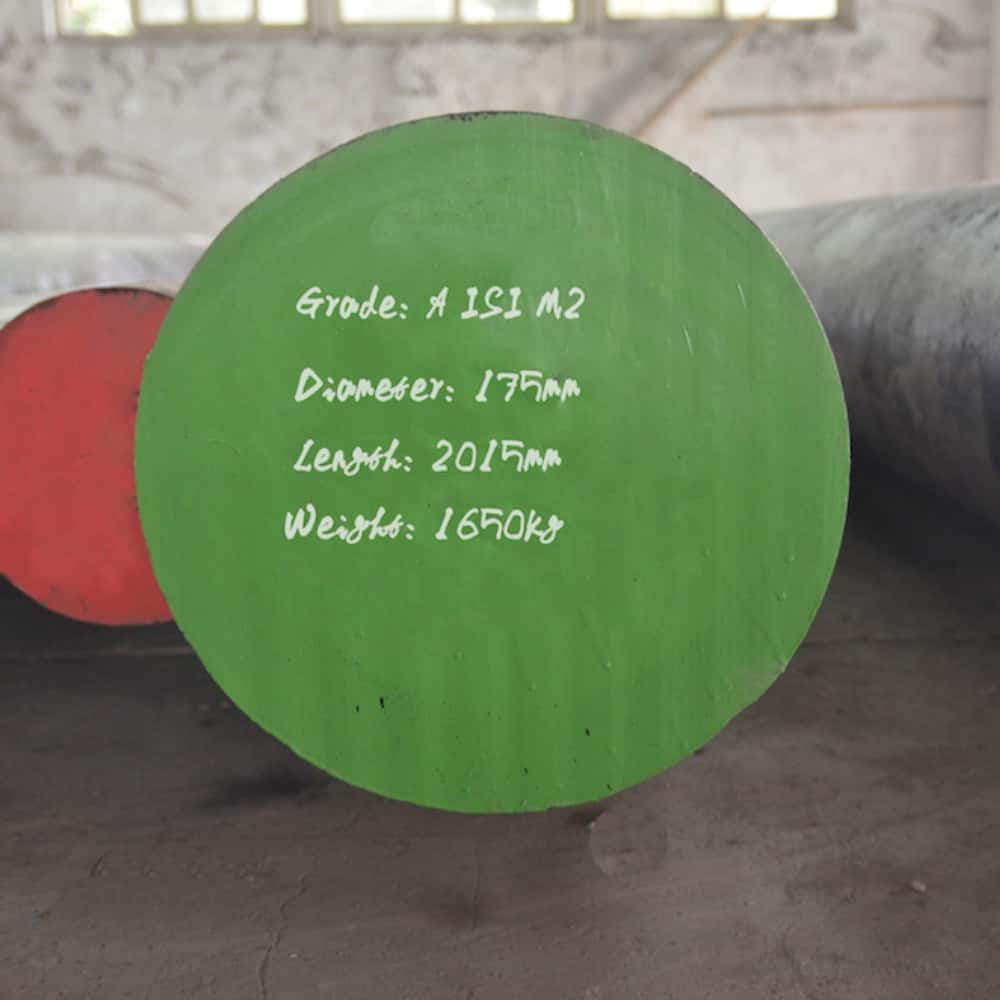
A commonly overlooked drawback of what is high speed steel is the amount of maintenance required to keep tools in optimal condition. HSS tools, while durable, tend to dull more quickly than carbide alternatives. This necessitates frequent regrinding and sharpening, especially in high-use environments.
These maintenance routines add to both labor and equipment costs. In industries with high output demands, the downtime required for tool sharpening can significantly affect productivity.
Challenges:
- Requires frequent regrinding
- Higher labor and equipment cost for maintenance
- Potential downtime in high-volume operations
Table: Comparing HSS With Other Tool Materials
Property | High Speed Steel (HSS) | Carbide | Tool Steel | Carbon Steel |
---|---|---|---|---|
Heat Resistance | Up to 600°C | Up to 1000°C | Moderate | Low |
Toughness | Moderate | Low | High | Moderate |
Wear Resistance | Good | Excellent | Fair | Poor |
Regrinding Frequency | High | Low | Moderate | High |
Cost | High | Very High | Moderate | Low |
Conclusion
Understanding what is high speed steel includes recognizing both its strengths and its limitations. While it’s a preferred choice for many due to its heat resistance and cutting ability, it is not always the best option depending on the specific application.
Its high cost, limited toughness in some environments, susceptibility to thermal fatigue, and frequent maintenance needs can outweigh its benefits in certain scenarios. However, for jobs requiring precision, speed, and high-temperature resilience, HSS remains a valuable asset.
Professionals and hobbyists alike should evaluate the full picture, weighing the pros and cons based on their operational needs. Exploring alternatives and knowing when to use or avoid HSS is key to maximizing efficiency and return on investment.
FAQ
What is high speed steel primarily used for?
High speed steel is commonly used to manufacture cutting tools like drills, taps, saw blades, and milling cutters due to its hardness and heat resistance.
Is high speed steel better than carbide?
It depends on the application. Carbide offers better wear resistance and heat tolerance, while HSS is tougher and easier to sharpen.
Can high speed steel be used for wood?
Yes, high speed steel tools are frequently used for woodworking, particularly in lathe operations and high-speed cutting.
How can I maintain high speed steel tools?
Regular regrinding and proper storage are essential. Avoid excessive heat and inspect tools frequently for wear or damage.
Does high speed steel rust easily?
It can rust if exposed to moisture, but many HSS tools are coated to prevent corrosion. Always store in a dry, clean environment.