Welcome to My Blog!
Before we dive into the content, I’d love for you to join me on my social media platforms where I share more insights, engage with the community, and post updates. Here’s how you can connect with me:
Facebook:https://www.facebook.com/profile.php?id=100090797846538
Now, let’s get started on our journey together. I hope you find the content here insightful, engaging, and valuable.
Table of Contents
Introduction
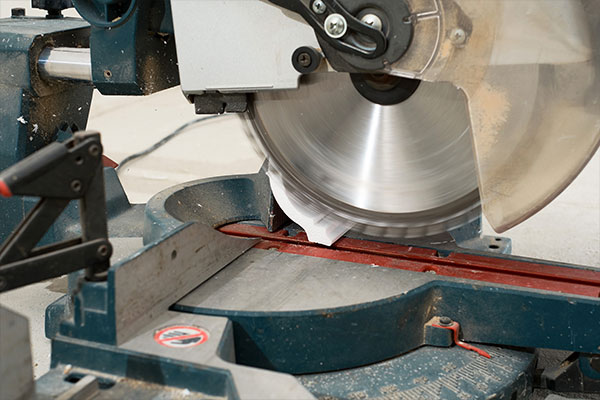
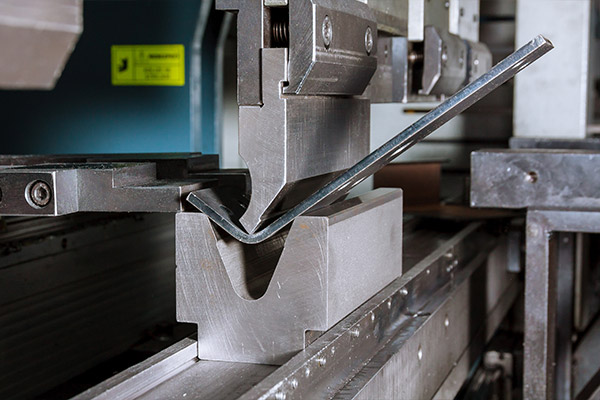
A2 tool steel is a versatile and widely used material in the manufacturing and tooling industries. Known for its excellent balance of hardness, toughness, and wear resistance, this alloy has become a favorite among engineers and toolmakers. Whether you’re crafting cutting tools, dies, or molds, understanding the unique properties of a2 tool steel can help you make informed decisions for your projects. In this blog, we’ll explore the four key properties that make a2 tool steel stand out and why it’s a top choice for demanding applications.
1. Exceptional Hardness
One of the most notable characteristics of this material is its exceptional hardness. This property makes it ideal for applications that require resistance to wear and deformation. Its ability to maintain structural integrity under heavy loads and high stress is a key reason why it is favored in demanding industries.
How Hardness is Achieved
The hardness of this alloy is primarily due to its high carbon and chromium content. When subjected to proper heat treatment, it can achieve a hardness of up to 60-62 HRC (Rockwell Hardness Scale). This level of hardness makes it particularly suitable for cutting tools, dies, and other components that endure significant mechanical stress. The heat treatment process involves heating the material to a specific temperature and then cooling it at a controlled rate to optimize its properties. Additionally, the presence of chromium helps form hard carbides, which further enhance the material’s resistance to wear and deformation.
Applications of Hardness
The exceptional hardness ensures that tools retain their sharp edges and precise shapes even under prolonged and heavy use. This is especially critical in industries like metalworking, where precision and durability are paramount. For example, in CNC machining, the material’s hardness allows for consistent performance and reduced wear, leading to lower maintenance costs and improved operational efficiency. Similarly, in the production of industrial blades, the hardness ensures that the blades can cut through tough materials without losing their edge, thereby increasing their lifespan and reducing the need for frequent replacements.
2. Superior Toughness
While hardness is essential, toughness is equally important for materials used in high-impact applications. This alloy strikes a perfect balance between hardness and toughness, making it resistant to chipping and cracking. This combination of properties is what sets it apart from other materials in its class.
The Role of Chromium and Molybdenum
The addition of chromium and molybdenum enhances the toughness of this material. These elements improve its ability to absorb energy without fracturing, which is crucial for tools subjected to sudden impacts or heavy loads. Chromium contributes to the formation of carbides, which enhance wear resistance, while molybdenum improves the material’s overall strength and stability. The presence of these alloying elements also helps in distributing stress more evenly across the material, reducing the likelihood of cracks or breaks under pressure.
Why Toughness Matters
In applications like stamping dies or punching tools, toughness ensures that the material can withstand repeated impacts without failing. This reduces the need for frequent replacements and lowers operational costs. For instance, in the automotive industry, where components are often subjected to high stress, the toughness of this material ensures long-lasting performance and reliability. Additionally, its ability to resist cracking under pressure makes it a preferred choice for tools used in heavy machinery and construction. In the manufacturing of molds, toughness is particularly important as it allows the molds to endure the repeated stresses of shaping materials without degrading over time.
By understanding these key properties—exceptional hardness and superior toughness—manufacturers can make informed decisions when selecting materials for their tools and components. This ensures optimal performance, durability, and cost-effectiveness in a wide range of industrial applications. The combination of these properties makes this alloy a versatile and reliable choice for industries that demand high-performance materials capable of withstanding extreme conditions.
3. Excellent Wear Resistance
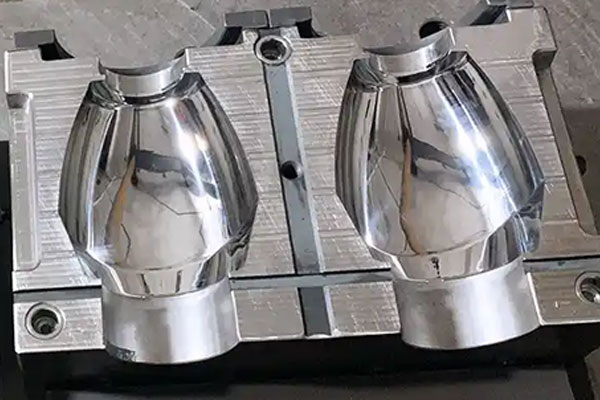
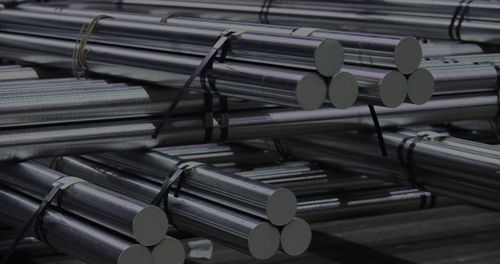
Wear resistance is another standout property of this material, making it a preferred choice for tools and components that endure constant friction and abrasion. This characteristic ensures that tools maintain their performance and longevity, even in demanding environments where wear and tear are significant concerns. Its ability to resist surface degradation under harsh conditions makes it indispensable in industries that rely on durable and reliable equipment.
Factors Contributing to Wear Resistance
The wear resistance of this alloy is primarily attributed to its high carbon content and the presence of alloying elements such as chromium and vanadium. These elements combine to form hard carbides, which act as a protective layer on the material’s surface, shielding it from abrasive forces. Chromium, in particular, enhances the formation of these carbides, while vanadium contributes to their fine distribution, further improving the material’s ability to withstand wear. Additionally, the uniform microstructure of the alloy ensures consistent performance across the entire surface, even under prolonged stress.
Real-World Applications
The exceptional wear resistance of this material makes it invaluable in applications where tools are exposed to abrasive materials or repetitive use. For example, in the manufacturing of cutting tools, the material’s ability to resist wear ensures that blades remain sharp and effective over extended periods, reducing the need for frequent replacements and maintenance. Similarly, in the production of shearing blades, the alloy’s durability allows it to cut through tough materials without losing its edge, enhancing productivity and reducing downtime.
In the field of forming dies, wear resistance is critical to maintaining precision and consistency. Dies made from this material can withstand the abrasive nature of materials like metals and plastics, ensuring that they retain their shape and functionality even after thousands of cycles. This is particularly important in industries such as automotive manufacturing, where precision and reliability are paramount. Additionally, in the mining and construction sectors, tools and components made from this alloy can endure the harsh conditions of abrasive rocks and debris, providing long-lasting performance and reducing operational costs.
4. Good Dimensional Stability
Dimensional stability is a critical property for materials used in precision tools and molds. This alloy exhibits minimal distortion during heat treatment, ensuring that the final product retains its intended shape and size. This property is especially important in applications where even minor deviations can lead to significant performance issues or costly errors.
The Importance of Heat Treatment
Achieving dimensional stability in this material relies heavily on proper heat treatment. The process involves heating the alloy to a specific temperature and then cooling it at a controlled rate to minimize internal stresses. This careful control of temperature and cooling prevents warping or deformation, ensuring that the material maintains its structural integrity and precise dimensions. The heat treatment process also enhances other properties, such as hardness and toughness, making it a critical step in the manufacturing of high-performance tools and components.
Applications in Precision Engineering
In industries like aerospace and automotive manufacturing, dimensional stability ensures that components fit together perfectly and function as intended. This reduces the risk of errors and improves overall efficiency.
Key Properties of A2 Tool Steel: A Summary Table
Property | Description | Applications |
---|---|---|
Exceptional Hardness | High resistance to wear and deformation | Cutting tools, dies |
Superior Toughness | Resistant to chipping and cracking | Stamping dies, punching tools |
Excellent Wear Resistance | Protects against friction and abrasion | Shearing blades, forming dies |
Good Dimensional Stability | Minimal distortion during heat treatment | Precision tools, molds |
Conclusion
A2 tool steel stands out as a premier material in the tooling and manufacturing industries due to its exceptional hardness, superior toughness, excellent wear resistance, and good dimensional stability. These properties make it a reliable choice for a wide range of applications, from cutting tools to precision molds. By understanding the unique characteristics of a2 tool steel, businesses can select the right material for their needs and achieve better performance and longevity in their tools and components.
FAQ
What is the primary use of a2 tool steel?
A2 tool steel is primarily used for making cutting tools, dies, and molds due to its hardness, toughness, and wear resistance.
How does a2 tool steel achieve its hardness?
The hardness of a2 tool steel is achieved through its high carbon and chromium content, along with proper heat treatment.
Can a2 tool steel be used for high-impact applications?
Yes, the superior toughness of a2 tool steel makes it suitable for high-impact applications like stamping dies and punching tools.
What makes a2 tool steel resistant to wear?
The presence of hard carbides formed by carbon, chromium, and vanadium enhances the wear resistance of a2 tool steel.
Why is dimensional stability important in a2 tool steel?
Dimensional stability ensures that tools and molds retain their shape and size during heat treatment, which is critical for precision engineering applications.