Welcome to My Blog! 🌟
Before we dive into the content, I’d love for you to join me on my social media platforms. It’s where I share more insights, engage with our vibrant community, and post regular updates. Here’s how you can stay connected:
📘 Facebook: Connect with me on Facebook
Now, let’s embark on this journey together. I hope you find the content here insightful, engaging, and most importantly, valuable. Let’s explore, learn, and grow together! 🚀
Table of Contents
Introduction
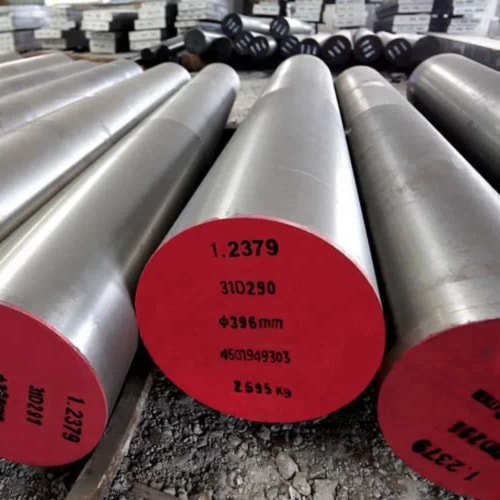
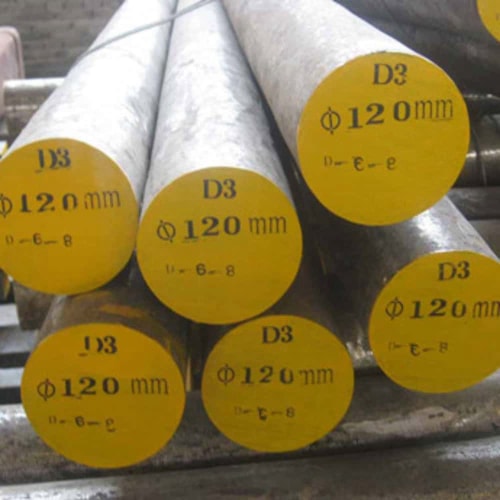
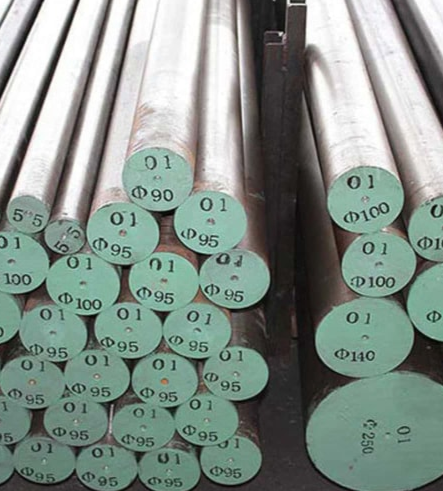
W1 tool steel has long been a popular material in various industries due to its unique properties and versatility. However, like many specialized materials, it is often surrounded by misconceptions and myths. These misunderstandings can lead to improper use, missed opportunities, or even costly mistakes. In this blog, we will debunk four common myths about W1 tool steel, providing clarity and insights to help you make informed decisions. Whether you’re a seasoned professional or a curious beginner, this guide will shed light on the true nature of W1 tool steel.
What is W1 Tool Steel?
W1 tool steel is a high-carbon, water-hardening material known for its exceptional wear resistance and ability to achieve high hardness levels through heat treatment. Its simple composition, primarily iron and carbon, makes it easy to work with when proper techniques are applied. This steel is commonly used in applications requiring sharp, durable edges, such as cutting tools, knives, punches, and dies.
A key feature of W1 tool steel is its water-hardening process, where it is quenched in water after heating to achieve rapid hardness. However, this requires careful control to avoid issues like cracking or warping. When handled correctly, it strikes a balance between hardness and toughness.
Despite its advantages, W1 tool steel is sometimes misunderstood, with misconceptions about its workability and versatility. In reality, it remains a cost-effective and reliable choice for toolmakers, especially in applications demanding sharpness and durability. By understanding its properties and proper handling, manufacturers can fully utilize its potential for creating high-performing tools.
Myth 1: This Material is Difficult to Work With
One of the most persistent myths surrounding this particular type of steel is that it is challenging to machine or shape. While it is true that this metal requires specific techniques during processing, it is far from impossible to work with. With the right tools and knowledge, it can be machined, ground, and heat-treated effectively.
For instance, proper cooling during machining is essential to prevent overheating, which can affect the material’s properties. Additionally, annealing the metal before machining can significantly improve its workability. By following these guidelines, manufacturers can harness the full potential of this steel without unnecessary difficulties.
Myth 2: This Steel is Not Durable
Another common misconception is that this steel lacks durability due to its water-hardening process. In reality, it is highly durable when used in the right applications. Its high carbon content allows it to achieve exceptional hardness, making it resistant to wear and abrasion.
However, durability depends on proper heat treatment and application. For example, this steel is not ideal for high-temperature environments, as it may lose hardness. But for room-temperature applications, such as cutting tools or blades, it performs exceptionally well. Understanding its limitations and strengths is key to maximizing its durability.
Myth 3: This Steel is Outdated
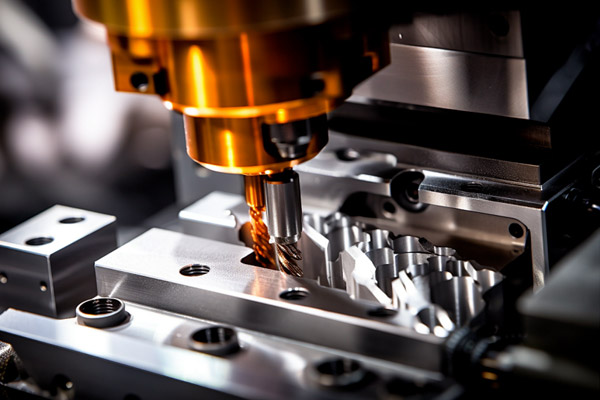
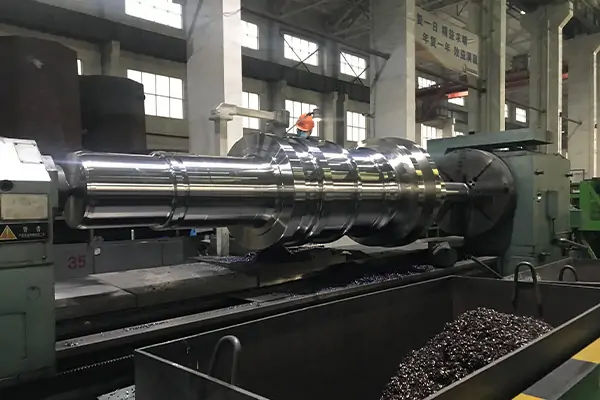
Some believe that this steel is an outdated material, overshadowed by modern alternatives. While it’s true that newer steels have been developed, this metal remains relevant due to its unique properties. Its ability to achieve high hardness and maintain a sharp edge makes it indispensable in certain applications.
Moreover, this steel is often more cost-effective than newer materials, making it an attractive option for budget-conscious projects. Its simplicity in composition and heat treatment also appeals to those who prefer traditional methods. Rather than being outdated, this steel continues to hold its own in the ever-evolving world of materials science.
Myth 4: This Steel is Only Suitable for Small Projects
A prevalent myth is that this steel is only suitable for small-scale projects or delicate tools. In fact, it is versatile and can be used in a wide range of applications, from small precision tools to larger industrial components.
For example, this steel is commonly used in the production of punches, dies, and cutting tools, which can vary significantly in size. Its ability to achieve high hardness and maintain sharp edges makes it suitable for both intricate and robust applications. The key is to design and heat-treat the material according to the specific requirements of the project.
Applications of W1 Tool Steel
To better understand the versatility of W1 tool steel, let’s explore its common applications:
Application | Description |
---|---|
Cutting Tools | W1 tool steel is widely used in knives, scissors, and other cutting instruments. |
Punches and Dies | Its hardness makes it ideal for creating precise punches and dies. |
Woodworking Tools | Chisels and plane blades benefit from W1 tool steel’s sharpness and durability. |
Industrial Components | Larger components, such as gears, can also be made from W1 tool steel. |
This table highlights the diverse uses of W1 tool steel, debunking the myth that it is limited to small projects.
How to Properly Heat Treat W1 Tool Steel
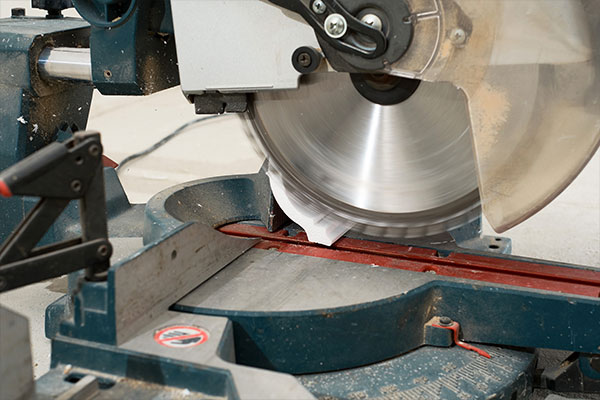
Heat treatment is a critical process for unlocking the full potential of high-carbon steels like W1. Properly executed, it enhances the material’s hardness, toughness, and overall performance. Here’s a detailed guide to the essential steps involved in heat treating this type of steel:
- Annealing: Annealing is the first step in preparing the material for machining or shaping. This process involves heating the steel to a specific temperature, typically between 1450°F and 1550°F (790°C to 840°C), and then allowing it to cool slowly in a controlled environment, such as in a furnace or insulated medium. The purpose of annealing is to soften the metal, making it easier to work with while reducing internal stresses. This step is particularly important for improving machinability and ensuring that the material can be shaped without cracking or warping.
- Hardening: Once the steel has been machined or shaped to its desired form, the next step is hardening. This involves heating the material to a high temperature, usually between 1450°F and 1600°F (790°C to 870°C), depending on the specific composition and desired outcome. After reaching the optimal temperature, the steel is rapidly quenched, typically in water or brine, to achieve maximum hardness. The quenching process locks in the hardened structure, which is essential for applications requiring wear resistance and durability. However, it’s important to note that rapid quenching can also introduce brittleness, which is why the next step is crucial.
- Tempering: Tempering is the final step in the heat treatment process and is essential for balancing hardness and toughness. After hardening, the steel is reheated to a lower temperature, typically between 300°F and 600°F (150°C to 315°C), and then allowed to cool slowly. This process reduces the brittleness introduced during quenching while maintaining a significant level of hardness. The exact tempering temperature and duration depend on the intended application of the steel. For example, tools that require high hardness with moderate toughness may be tempered at a lower temperature, while components needing greater toughness may undergo tempering at a higher temperature.
Additional Considerations
- Preheating: Before hardening, it’s often beneficial to preheat the steel to a moderate temperature to minimize thermal shock during the final heating phase.
- Cooling Rate: The cooling rate during quenching plays a vital role in determining the final properties of the steel. Water quenching provides rapid cooling, which is ideal for achieving high hardness, but other media like oil or air can be used for less severe cooling rates.
- Surface Finish: After heat treatment, the steel may require additional finishing processes, such as grinding or polishing, to achieve the desired surface quality and dimensional accuracy.
By following these steps, you can ensure that W1 tool steel performs optimally in its intended application.
Conclusion
W1 tool steel is a remarkable material with a rich history and a wide range of applications. By debunking these common myths, we hope to provide a clearer understanding of its properties and potential. Whether you’re working on a small project or a large industrial component, W1 tool steel can be a valuable asset when used correctly. Remember, the key to success lies in proper heat treatment, application, and a willingness to explore its capabilities.
FAQ
Q1: Can W1 tool steel be used for high-temperature applications?
A1: No, W1 tool steel is not suitable for high-temperature environments. Due to its water-hardening properties, it may lose hardness and structural integrity when exposed to elevated temperatures. For such conditions, other tool steels designed for heat resistance, such as H-series or high-speed steels, are more appropriate.
Q2: Is W1 tool steel more cost-effective than other tool steels?
A2: Yes, W1 tool steel is generally more affordable compared to newer, specialized tool steels. Its straightforward composition and ease of heat treatment make it a budget-friendly option for many applications, especially where high hardness and wear resistance are required without the need for advanced alloying elements.
Q3: What is the best way to machine W1 tool steel?
A3: The best approach to machining W1 tool steel involves annealing it first to soften the material, making it easier to work with. Additionally, using proper cooling techniques during machining is essential to prevent overheating, which can affect the steel’s properties. These steps ensure smoother machining and reduce the risk of tool wear or material damage.
Q4: Can W1 tool steel be used for large industrial components?
A4: Yes, W1 tool steel is versatile and can be used for both small and large applications when properly heat-treated.
Q5: How does W1 tool steel compare to modern tool steels?
A5: While modern tool steels often offer specialized advantages, such as improved toughness, heat resistance, or wear performance, W1 tool steel remains relevant due to its high hardness, ease of heat treatment, and cost-effectiveness. It is particularly valued in applications where sharpness and wear resistance are critical, and where the simplicity of its composition and processing is advantageous.