Welcome to My Blog! 🌟
Before we dive into the content, I’d love for you to join me on my social media platforms. It’s where I share more insights, engage with our vibrant community, and post regular updates. Here’s how you can stay connected:
📘 Facebook: Connect with me on Facebook
Now, let’s embark on this journey together. I hope you find the content here insightful, engaging, and most importantly, valuable. Let’s explore, learn, and grow together! 🚀
Table of Contents
Introduction
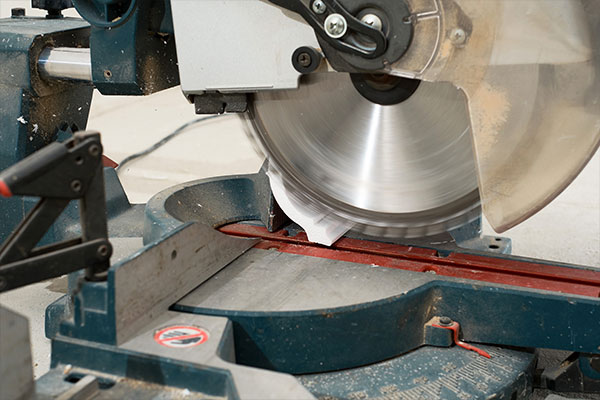
Choosing the right tool steel for knives is critical to ensuring performance, durability, and user satisfaction. Tool steel is a broad category of carbon and alloy steels particularly suited for cutting and shaping materials. However, not all tool steel is created equal. Some types may look good on paper but underperform in real-world applications, particularly in knife making. Whether you’re a custom bladesmith, a manufacturer, or an enthusiast, knowing which tool steel for knives to avoid can save time, money, and frustration.
In this article, we will explore three types of tool steel for knives that you should steer clear of. Each has significant drawbacks in terms of wear resistance, toughness, corrosion resistance, or overall usability. We will provide a detailed explanation of each steel’s properties, typical applications, and why they may not be ideal for knives.
Tool Steel for Knives Overview
Tool steels are a group of carbon and alloy steels specifically designed for high-performance tasks like cutting, shaping, and machining materials. For knife making, tool steels are often selected for their hardness, toughness, and edge retention—traits vital to a quality blade. They are generally categorized into several groups based on their properties and intended applications:
- High-Speed Steels (e.g., M2, T15): Designed for cutting tools operating at high speeds and temperatures.
- Cold-Work Steels (e.g., D2, A2, O1): Used for shaping materials at room temperature, often known for excellent wear resistance.
- Hot-Work Steels (e.g., H13): Intended for high-temperature applications like forging dies.
- Shock-Resistant Steels (e.g., S7): Engineered to absorb high impact forces without cracking.
Among these, steels like D2, A2, and O1 have earned their place in knife making due to their favorable combination of edge retention, toughness, and ease of heat treatment. However, some tool steels—despite performing well in industrial contexts—can underperform or even fail when used in knives.
Key Factors in Evaluating Tool Steel for Knives
When assessing whether a tool steel is appropriate for knife making, several critical criteria must be considered:
- Hardness and Edge Retention: A harder steel generally holds its edge longer, but excessive hardness can lead to brittleness and chipping.
- Toughness and Resistance to Chipping: Toughness allows a blade to resist impact and lateral forces without cracking.
- Corrosion Resistance: Essential for knives used in humid, wet, or acidic environments. Low corrosion resistance can lead to rust and blade degradation.
- Ease of Sharpening: While ultra-hard steels may stay sharp longer, they are often more difficult to sharpen with standard abrasives.
- Heat Treating Requirements: The steel’s response to heat treatment affects its final performance. Some steels require precise temperature control and specialized equipment, making them challenging for hobbyists or small-scale makers.
Understanding these criteria is crucial when selecting or avoiding certain tool steels for knives. Even a steel that excels in one area might be unsuitable overall if it lacks balance across all categories.
NO 1. T15 High-Speed Steel: Too Hard to Handle
T15 is a high-speed tool steel often praised for its extremely high hardness and excellent wear resistance. While these traits may sound beneficial, they present serious disadvantages when used in knives.
Why Avoid T15 for Knives?
- Excessive Hardness: T15 is so hard that it becomes brittle, leading to edge chipping or breakage.
- Difficult Sharpening: The steel’s hardness makes it extremely hard to sharpen using standard tools.
- Expensive Processing: It requires precise heat treatment and specialized equipment.
- Limited Flexibility: Not suitable for knives expected to undergo impact or lateral stress.
T15 may be appropriate for machining tools, but for knife blades that require a balance of strength, toughness, and usability, this steel is usually a poor choice.
NO 2. W1 Tool Steel: Great for Tools, Poor for Knives
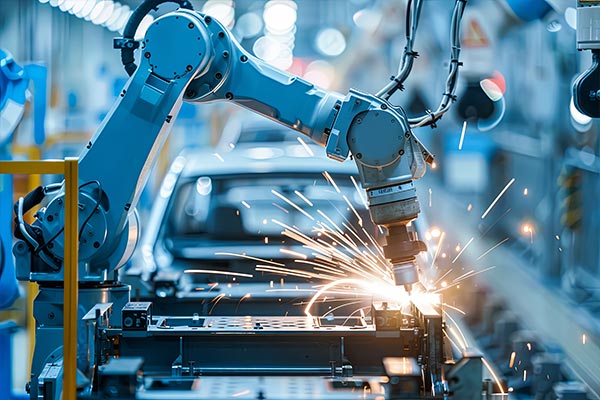
W1 tool steel is water-hardening steel often used in making drills and cutting tools. It’s readily available and easy to machine, which tempts some novice knife makers into using it.
Why Avoid W1 Tool Steel for Knives?
- Low Toughness: W1 lacks the toughness necessary for reliable knife performance.
- Highly Prone to Cracking: The water-quenching process increases the risk of cracking during heat treatment.
- Poor Corrosion Resistance: W1 rusts easily unless meticulously maintained.
- Inconsistent Quality: Being inexpensive, W1 is often less controlled in composition.
While W1 might seem like a cost-effective option, its weaknesses far outweigh the benefits in knife-making applications.
NO 3. S7 Tool Steel: Impact-Resistant but Unfit for Blades
S7 tool steel is known for its shock resistance and is commonly used in tools like chisels, jackhammer bits, and punches. However, these properties don’t translate well to knife blades.
Why Avoid S7 Tool Steel for Knives?
- Too Soft for Edge Retention: S7 does not hold an edge well compared to other tool steels.
- Hard to Heat Treat Precisely: Achieving consistent hardness is difficult without high-end equipment.
- Bulky Microstructure: The steel’s structure hinders fine edge geometry.
- Not Ideal for Precision Cutting: Lacks the sharpness needed for refined cutting tasks.
S7’s shock resistance is commendable, but in the context of tool steel for knives, it lacks the necessary attributes for a reliable blade material.
Comparative Table: Problematic Tool Steel for Knives
Tool Steel | Primary Application | Major Drawback in Knives | Edge Retention | Corrosion Resistance | Sharpening Difficulty |
---|---|---|---|---|---|
T15 | Machining tools | Too hard, brittle, expensive | High | Moderate | Very High |
W1 | Cutting tools | Cracks easily, rusts quickly | Low | Very Low | Medium |
S7 | Impact tools | Poor edge retention, bulky | Very Low | Low | High |
How to Choose Better Tool Steel for Knives
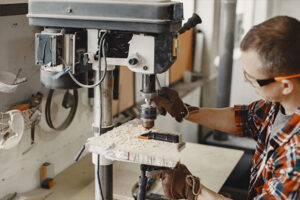
Instead of selecting tool steel for knives that have well-documented issues such as brittleness, poor edge retention, or difficulty in sharpening, it’s far more beneficial to opt for steels that have stood the test of time in both laboratory testing and real-world use. Selecting the right material is not just a matter of preference—it’s a crucial decision that impacts the performance, durability, and maintenance requirements of your knife.
Well-regarded steels like D2, A2, and the CPM series (such as CPM S30V, CPM M4, and CPM 3V) have earned a solid reputation for reliability, making them common choices among custom knife makers and production knife manufacturers. These tool steels offer an ideal balance between edge retention, toughness, and wear resistance. They are engineered to handle both everyday cutting tasks and more specialized functions like bushcraft, hunting, or culinary use.
Key Qualities to Look For When Choosing Tool Steel for Knives:
- Balanced hardness and toughness: The best knife steels maintain a keen edge while resisting chipping or cracking under stress.
- Good corrosion resistance: Especially important for knives used in humid, coastal, or wet environments where rust can be an issue.
- Consistent and reliable heat treatability: A steel that responds well to heat treatment allows manufacturers to bring out the best performance from the alloy.
- Sharpening ease: While ultra-hard steels can hold an edge longer, they often require specialized sharpening tools. A good tool steel should strike a balance between edge longevity and ease of maintenance.
It’s also vital to align your steel choice with how the knife will be used. A field knife designed for survival applications will benefit from a tougher steel with high impact resistance, such as CPM 3V or A2. In contrast, a chef’s knife needs excellent wear resistance and good food safety performance, making stainless tool steels like CPM S35VN or D2 more suitable.
In summary, choosing better tool steel for knives involves understanding both the technical properties of the steel and the practical demands of your intended tasks. This informed approach ensures not only superior cutting performance but also long-term satisfaction with your knife.
Conclusion
Choosing the wrong tool steel for knives can lead to disappointing performance, frequent maintenance, and reduced lifespan. T15, W1, and S7 may be excellent for their industrial uses, but they are not ideal for knife blades due to their brittleness, rust-proneness, or poor edge retention. When selecting tool steel for knives, prioritize balanced properties tailored to your needs. Invest in materials that offer a harmonious blend of hardness, toughness, and ease of maintenance.
By understanding which tool steels to avoid, you place yourself in a better position to craft or purchase a knife that will perform reliably and last longer.
FAQ
What makes a tool steel bad for knives?
A tool steel that is too brittle, prone to corrosion, or hard to sharpen generally performs poorly as a knife blade.
Can you still use T15, W1, or S7 for knives?
While it’s technically possible, the resulting knives will likely have significant drawbacks, making them unsuitable for most users.
What are some good alternatives to these steels?
D2, A2, and CPM-3V are popular choices among knife makers due to their durability, edge retention, and relative ease of maintenance.
Is high hardness always a good thing?
Not necessarily. Too much hardness can lead to brittleness and chipping, which is why a balance with toughness is crucial.
Should beginners avoid tool steel altogether?
Not at all. Beginners should simply choose proven steels with good documentation and community support to ease the learning curve in heat treatment and sharpening.