Revolutionary Tooling Solutions: The Magic of Tool Steel
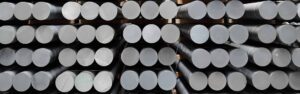
Tool steel is a special type of steel that is designed to withstand the extreme forces and temperatures involved in shaping, cutting, extruding, and forming metal. The unique properties of tool steels make them an indispensable material for toolmakers, allowing them to create precision tools, molds, dies, and machine parts that would be impossible with other materials. From the drills that pull oil and gas from miles underground, to the molds that shape delicate glassworks—tool steels are the unsung heroes behind many of the manufactured items we rely on every day.
In this article, we’ll explore what makes tool steels so exceptional, how they are produced, the different types and their specialized applications, how tooling engineers select the optimal steel, and the future possibilities opened up by advances in tool steel technology. Discover how this versatile metal helps build our world while pushing the boundaries of what’s possible in manufacturing.
An Introduction to Tool Steels
Tool steels refer to a variety of carbon and alloy steels that are specifically formulated to withstand the demands of being made into tools. Their key characteristics include:
- Hardness: Tool steels obtain high hardness and strength through the addition of alloying elements like tungsten, molybdenum, cobalt, and vanadium. This allows them to withstand tremendous cutting forces and retain their shape at high temperatures.
- Wear resistance: They resist abrasion and chipping when sharpened or shaped. This allows tooling made from them to have a long service life before needing replacement.
- Heat resistance: Tool steels retain their hardness and strength even when exposed to high temperatures caused by friction during machining and forming operations.
- Toughness: While hard for wear resistance, tool steels also have enough toughness and shock resistance to survive the dynamic loads and impacts that tools routinely experience.
- Dimensional stability: The materials resist warping or shrinking to hold their precise shapes through repeated heating/cooling cycles.
Tool steels achieve these properties through careful control of their chemistry, as well as proper heat treatment. This balance of hardness, wear resistance, and toughness is what gives finished tool steel components the longevity and performance needed to produce consistent, high-quality workpieces.
A Brief History of Tool Steels
While early civilizations used iron and primitive steels to fashion tools, the history of modern tool steels begins in the 18th century as metallurgy and machining capabilities advanced. Some key developments include:
- 1740s: English clockmaker Benjamin Huntsman pioneers crucible steel, allowing the production of higher quality tool steels.
- 1868: Robert Forester Mushet invents R. Mushet’s Special Steel, considered the first true tool steel. It revolutionizes tooling capabilities.
- 1900s: Advancements in metallurgy and heat treating spawn development of high speed steel. The alloy’s hardness and red hardness allow faster machining.
- 1915: Tungsten carbide is introduced and eventually helps replace high speed steels with a harder material.
- Mid 1900s: Continuous casting makes it possible to produce large uniform billets to create newer grades and types of tool steel.
- Today: Tool steels continue advancing, optimizing compositions and processes to create steels with enhanced properties. Modern powder metallurgy techniques can produce tool steels unattainable through conventional practices.
Tool steel has progressed hand-in-hand with manufacturing and machining capabilities. As techniques like metal cutting and die casting demanded better tooling, metallurgists responded with new steel alloys and processing methods to fill the need. Tool steel sits at the leading edge of what’s possible in manufacturing.
How Tool Steels Are Made
Producing tool steels requires precise control over composition and processing:
Alloying
Tool steel starts with a base of iron and carbon. Various alloying elements are then added to impart desired attributes. Common alloys include:
- Tungsten: Boosts hardness and toughness for wear resistance. Also improves strength at high temps.
- Molybdenum: Increases strength and machinability. Enhances elevated temperature properties.
- Vanadium: Fine-grains the microstructure for hardness and fatigue strength. Improves wear resistance.
- Cobalt: Adds hot hardness and facilitates heat treating.
- Chromium: Improves hardenability, wear/corrosion resistance, and toughness.
- Manganese: Combines with sulfur to remove it during manufacturing. Provides hardenability.
Strict control over the types and amounts of alloys produces tool steels to specification. Different compositions target different tooling applications and requirements.
Melting
Tool steels begin by melting iron and other elements in an electric arc furnace or induction furnace. Most grades use an open hearth or electric furnace with varying temperature controls and protective atmospheres.
Fine-tuned melting controls ensure proper alloy dissolution and a uniform composition. Some higher alloy grades require special processes like vacuum induction melting or vacuum arc remelting to avoid contamination.
Shaping
The molten steel is cast into a rough shape, often a billet. The steel can be cast in:
- Ingot molds – Produces rectangular or round ingot billets for further processing.
- Continuous casters – Forms a continuous strand that is cut into set lengths. Faster than ingot casting.
- Electroslag remelting – Remelts ingot or continuous cast tool steel to remove impurities and improve uniformity.
Forging further shapes the steel into bar stock, rod, or other forms needed for toolmaking. Steel in billet form may also undergo shaping steps like extrusion or drawing.
Heat Treatment
Tool steels derive their key properties from proper heat treatment and tempering after initial wrought processing. Heat treatment involves:
- Hardening – Heated then quenched at a rapid rate to form martensite and desired hardness.
- Tempering – Reheating to a specific temperature to remove brittleness and refine grain size. This fine-tunes hardness, toughness, and ductility.
- Annealing – Extended heating followed by slow cooling to soften the steel for improved machinability.
- Stress relieving – Heating to relax residual stresses in the material before final machining.
Tool steel properties directly correlate to following strict thermal processing instructions. Each grade has optimized hardening and tempering procedures.
Categories of Tool Steels
There are thousands of tool steel grades offering different mixes of properties. They can be grouped into seven major categories:
1. Cold work steels
Best suited for punches, dies, and forming tools that shape metal at room temperature. Excellent wear resistance and hardenability. Grades like A2, A6, D2, and D3 (oil hardening steels) are common for blanking, shear blades, tool holders, and press brakes.
2. Shock resisting steels
Have high toughness and compressive strength for impact loads. Used for chisels, claw bars, percussive tools. S1, S5, and S7 grades (chrome-moly shock steels) are typical choices.
3. Hot work steels
Retain hardness and resist thermal fatigue at high temperatures up to 1000°F (540°C). Used for hot forming, extrusion, and die casting dies. Popular alloys include H11, H12, H13, H19, and H21 (chrome-moly hot work steels).
4. High speed steels
Exhibit hardness and wear resistance even when reaching high temperatures from friction during machining. Allow faster cutting speeds than carbon tool steels. Molybdenum-tungsten M and T series grades are commonly used for cutting tools like drills and saw blades.
5. Mold steels
Feature excellent hardenability for larger cross sections. Polishing and texturing capabilities aid mold details and release. P20 and P30 grades are commonly used. Stainless grades like 420, 440C and PH also make good mold tooling.
6. Water hardening steels
Hardened by quenching in water or brine instead of oil. Used for cutting tools where reaching optimal hardness is more important than toughness. Grades like W1 and W2 contain tungsten and chromium carbides for wear resistance.
7. High carbon, high chromium
Achieve maximum hardness when air cooled instead of quenched. Used for punches, woodworking tools, razor blades. Grades like 52100 and 154CM (bearing steels) exhibit high hardness and compressive strength.
This overview shows the diversity of tool steel grades. Each is formulated with its end use in mind, whether shaping cold metal in a progressive die, or cutting alloys at blinding speeds in a CNC lathe.
Tool Steel Selection Criteria
Choosing the optimal tool steel depends on:
Service Conditions
What temperatures, stresses, and wear will the tooling encounter? Is high red hardness required? Will impact loads be present? This helps narrow suitable grades.
Part Accuracy
How much precision and surface finish is needed on the workpiece? Tighter tolerances and finer finishes require dimensionally stable tooling.
Production Volume
Lower volume production can utilize slower but tougher tooling. High volumes demand maximum tool life and uptime before replacement is needed.
Comparative Costs
The steel is only one component. Consider overall costs of machining, heat treating, processing, maintenance, and tool life during production.
Availability
Selecting readily available bar stock can avoid long lead times. Custom processed grades may require melting and forging specially ordered billets.
Familiarity
Sticking with known tool steels lowers the learning curve. But new grades may outperform a shop’s standards. Testing new alloys in lower risk applications builds experience.
Careful balancing of those factors results in the ideal match between tool steel and application.
Innovating with Tool Steels
Advancing tool steel technology occurs on two fronts—developing superior alloys, and refining production techniques:
New steel alloys
Metallurgists continue formulating tool steel alloys with enhanced properties. Some focus areas:
- Improving heat resistance for accelerating machining speeds and throughput
- Increasing hardness for longer tool life and sharper cutting edges
- Optimizing toughness to withstand heavy interruptions and abuse
- Enhancing corrosion resistance for molding and forming reactive materials
- Reducing specific alloys like cobalt to control material costs
- Microalloying with elements like vanadium and niobium to refine the steel’s grain structure for strength
- Powder metallurgy utilizes fine metal powders to allow highly alloyed compositions impossible through ingot metallurgy. PM process also creates ultra-uniform microstructures.
Production processes
Refining how tool steels are manufactured also produces improved grades. Techniques like:
- Vacuum processing to reduce impurities and pinpoint alloying additions
- Electroslag remelting to remove inclusions and improve homogeneity
- Secondary remelting of ingots to enhance uniformity in larger cross sections
- Direct aging treatments to optimize toughness and ductility
- Computer modeling of cooling rates and microstructures helps perfect heat treating for specific tool steels
Tool steel producers continue honing melting, casting, shaping, and heat treating methods. This elevates steel quality and capabilities over each generation.
Cutting-Edge Tool Steel Applications
Tool steels enable shaping and machining applications not previously possible. Some examples at the leading edge:
Aerospace
Aircraft engines operate under extreme heat and stress. New nickel-based superalloys and hardfacing coatings allow jet engine components to withstand higher temperatures and last longer between overhauls.
Automotive
Automakers demand process improvements and lighter materials. Tool steels shape lighter aluminum and carbon fiber pieces and churn out components faster through high speed machining.
Consumer electronics
Molding the tiny, angled features on smartphone and tablet cases requires highly polished tool steel molds with precision details. Tolerances can be within 5 microns.
Medical
Delicate surgical tools and instruments made from 420 and 440C stainless tool steels ensure precision shaping and cutting of bone, tissue, and body materials.
Die casting
Zinc, aluminum, and magnesium die casting demands tooling that can withstand molten metal while producing millions of complex, high tolerance castings. H13 is a popular die steel choice.
Energy
Drilling miles deep to tap petroleum and natural gas reserves requires specialty drill bits employing high cobalt tool steel alloys and tungsten carbide inserts. The steels withstand tremendous heat and compressive loads.
These examples demonstrate how tool steel sits at the foundation of many leading manufacturing feats. Without tool steels producing the drills, molds, dies, and cutting implements, such processes would be impossible. As tool steels improve, they enable pushing boundaries even further.
The Future of Tool Steels
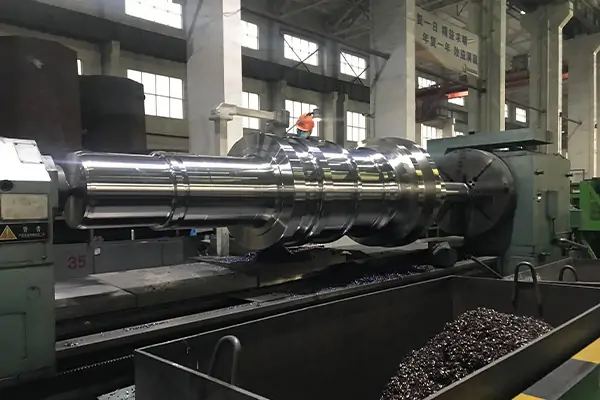
Advancing tool steel technology will open new frontiers in manufacturing capabilities. Some possibilities on the horizon:
Machining at the edge
New tool steel alloys and coatings will push cutting speeds ever faster and handle more aggressive machining parameters. This may enable high speed machining of tougher metals like stainless steel and titanium.
Additive manufacturing
Powder metallurgy tool steel alloys could allow 3D printing of finished tooling components with superior qualities. Complex tool geometries unattainable through machining may be possible.
Nanostructured and gradient tooling
Nano-grained tool steels and compositional gradients could optimize steel properties precisely where needed in a tool. This may lead to fewer necessary alloying elements for cost savings.
Tooling intelligence
Embedding sensors into tooling could enable real-time monitoring of tool health and part quality during production. This opens possibilities for predictive maintenance and adaptive machining.
Shaping any material
More robust tooling could expand materials able to be precision machined or molded. Everything from composites and rubbers to glass and ceramics may become viable workpiece materials.
Tool steels sit in a prime position to enable emerging manufacturing breakthroughs. The future looks bright for leveraging these indispensable metals even further.
Key Takeaways on Tool Steels
Tool steels are invaluable in manufacturing:
- Unique properties like hardness, wear resistance, and dimensional stability allow them to be fashioned into tools.
- Meticulous control over alloying and production yields tool steel grades optimized for different applications.
- Categories are tailored for cold work, hot work, high speed cutting, and molding applications.
- Careful selection considers the service conditions, accuracy needs, production volume, costs, and availability.
- Developing superior alloys and perfecting processing methods continues improving tool steel performance.
- Cutting-edge tools and dies made from tool steels enable emerging miracles in manufacturing.
- Advances promise machining at untapped speeds, 3D printed tooling, nanostructured metals, intelligent components, and expanded material capabilities.
- Tool steels will remain mission-critical in pushing the boundaries of manufacturing possibilities.
The unique properties of tool steel make it a magical material for toolmakers. This versatile metal is ready to support manufacturers in shaping the future. By uncovering the inner workings of tool steel, we gain insight into how it builds the modern world around us. Tool steel truly sits at the leading edge of innovation.
FAQ
What are tool steels?
Tool steels refer to a variety of alloy steels that are designed specifically for use in manufacturing tools and dies, including cutting tools, molds, and dies for shaping other materials. They are engineered to withstand the extreme forces, temperatures, and wear encountered during machining, molding, stamping, and other fabrication work. Key qualities include hardness, wear resistance, toughness, and dimensional stability.
How is tool steel made?
Tool steels start with a base of iron and carbon. Alloying elements like tungsten, chromium, molybdenum, vanadium, and cobalt are added to impart desired properties. The steel is melted and cast into billets or ingots, then forged into bar stock or other shapes. Heat treating steps like quenching and tempering impart the hardness, strength, and microstructure that give tool steels their unique qualities.
What are the main types of tool steels?
Some common categories include:
- Cold work steels – For cutting, punching, bending, shearing at room temperature. (A2, D2, D3)
- Hot work steels – Retain hardness at high temps for die casting and hot forming. (H13, H21)
- High speed steels – Hardness for cutting tools and machining at high speeds. (M2, M4)
- Mold steels – Optimized for mold cavity machining and corrosive resistance. (P20, 420 stainless)
- Shock resisting steels – Withstand impact loads. (S7)
- Water hardening steels – Maximize hardness. (W1, W2)
- High carbon/high chromium steels – Extreme hardness when air cooled. (52100)
How are tool steels used in manufacturing?
Tool steels are used to create all kinds of tooling:
- Cutting tools – Drills, taps, milling cutters, saw blades
- Dies – For stamping, blanking, punching, bending, forming
- Molds – For casting, injection molding, forging, glass molding
- Gauges, jigs, fixtures – For holding and measuring parts
- Extrusion and drawing dies – For creating wire, rod, tubing
- Rolls – For shaping, bending, forming sheet metal and plate
How are tool steels selected for an application?
Important factors when selecting tool steels include:
- Operating temperatures, stresses, and wear mechanisms
- Dimensional accuracy and surface finish requirements